The value of a vapour barrier when installing floor coverings
Spring is something special in South Africa as we take a collective breath of fresh air and look forward to the return of warmer weather. It also means that we need to start thinking about how to manage the risk of rising moisture levels in substrates with the return of summer rains across most of the country.
Most flooring installers are aware that the substrate must be fully cured and have attained the moisture content stipulated by the manufacturer of the floor covering before installing the final floor covering. This is because excessive moisture in the substrate, or high moisture vapour emission rates, will most certainly result in an installation failure, for example, vinyl flooring ‘bubbling’ or delaminating from the substrate.
If there is no damp-proof membrane below a surface bed, or if moisture levels do not attain 3% (75% RH) or less, a suitable moisture, or vapour barrier should be installed such as TAL VaporStop HB. This is not to be confused with a surface sealant, which is applied as a protective layer over a floor substrate or covering.
Manufacturers of floor coverings stipulate moisture levels for their materials, to ensure a successful end result. Ordinarily, 28-days are required for a concrete or sand/cement screed topping to cure and the construction moisture to dry out, prior to installing the floor coverings. However, it can happen that even though the floor surface may appear to be dry at the time of installation, when tested, moisture levels within the surface are higher than the manufacturers recommendations. This can be due to not enough time allowed for curing / drying out of the substrate, or the moisture levels may remain too high because of seasonal fluctuations, changes in geographic surface run-off and structural changes in and around the building. It is therefore recommended that TAL VaporStop HB be installed as part of the installation system, to prevent the passage of water vapour and moisture through the concrete slab into the final floor covering.
Whilst the additional cost may seem an unnecessary addition to the flooring system, the cost of repairing a failed flooring installation far outweighs the costs of the vapour barrier. Using a multi-level system approach when installing floor coverings is key to enjoying a long-lasting and durable installation, and a happy client.
For more information on the value of vapour barriers and on multi-level installation systems for floor coverings, contact the TAL Technical Advice Centre.
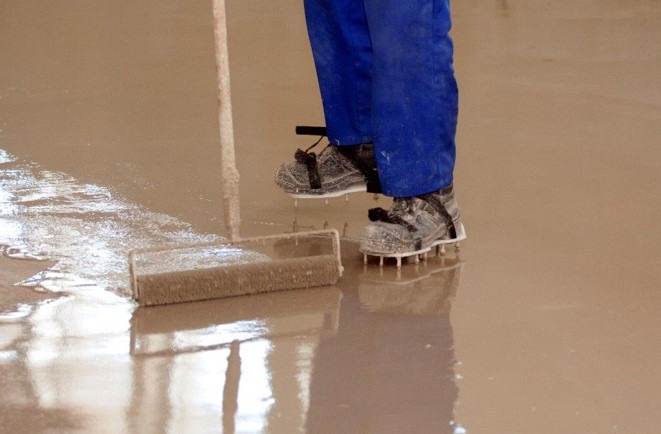
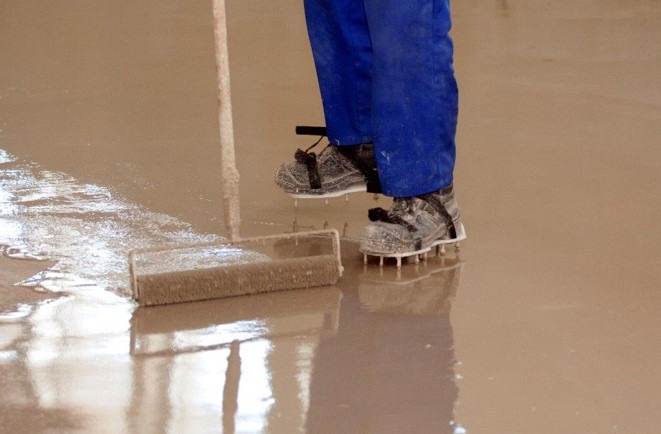
Unlike trowel-applied underlayments, that are usually only able to be applied a few square meters at a time, self-levelling underlayments are flowable and designed to be poured over the surface, then spread out to the desired thickness with an appropriate notched floor rake or adjustable floor spreader.
The high-flow and rapid-setting properties result in minimised installation times, making them ideal for fast-track installations. They can also be installed manually or can be pumped for large contracts or upper level floors.
The application of self-levelling underlayment compounds requires professional equipment and trained applicators, and as such, are better suited for installation by experienced installers.
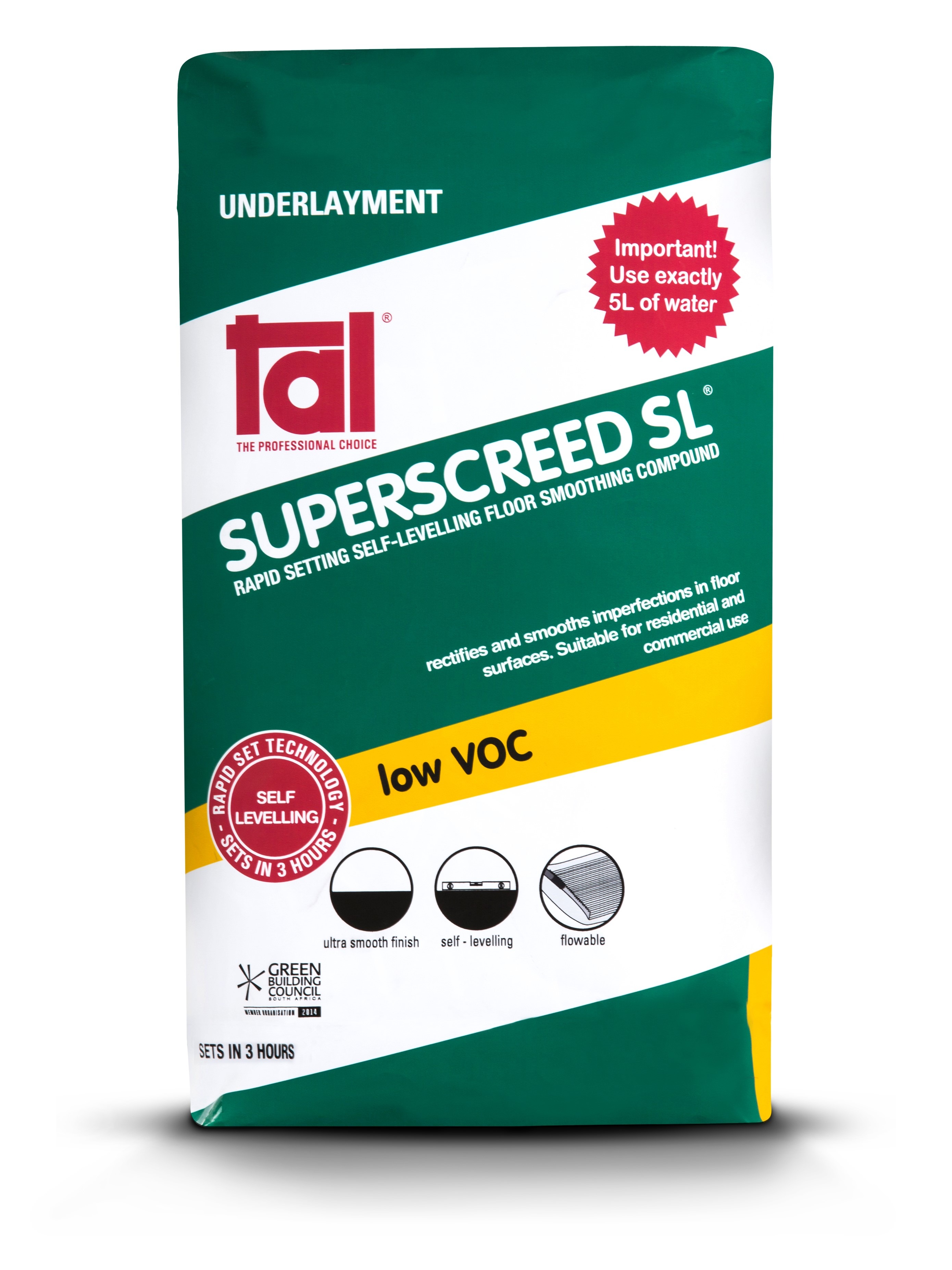
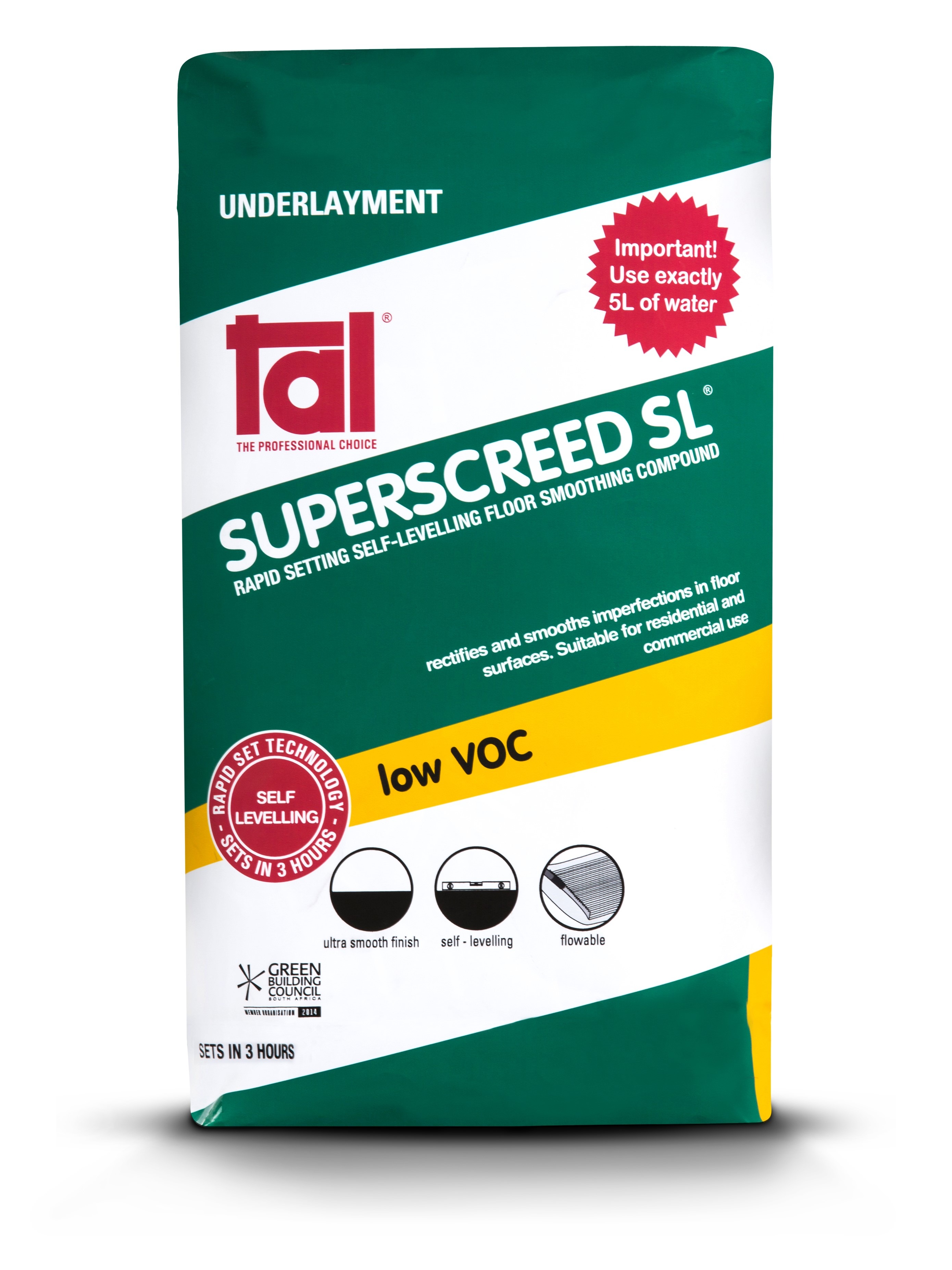
Additives
An additive is a latex-based liquid, designed to replace water in a cement-based adhesive and / or grout mix which is used when tiling or grouting external areas, wet areas, high traffic areas and areas where some flexibility is required. Our range of additives includes TAL Bond and TAL Screedbinder.
TAL Bond improves the bond strength, flexibility and water-resistance when used as a water replacement in cement-based adhesive and grout mixtures.
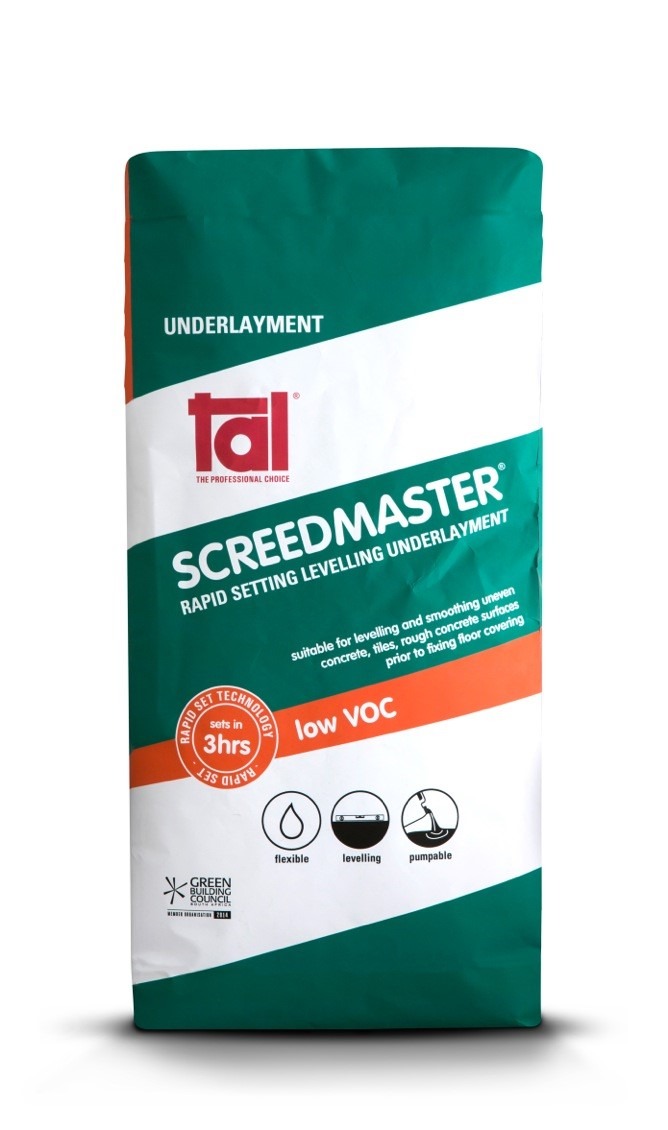
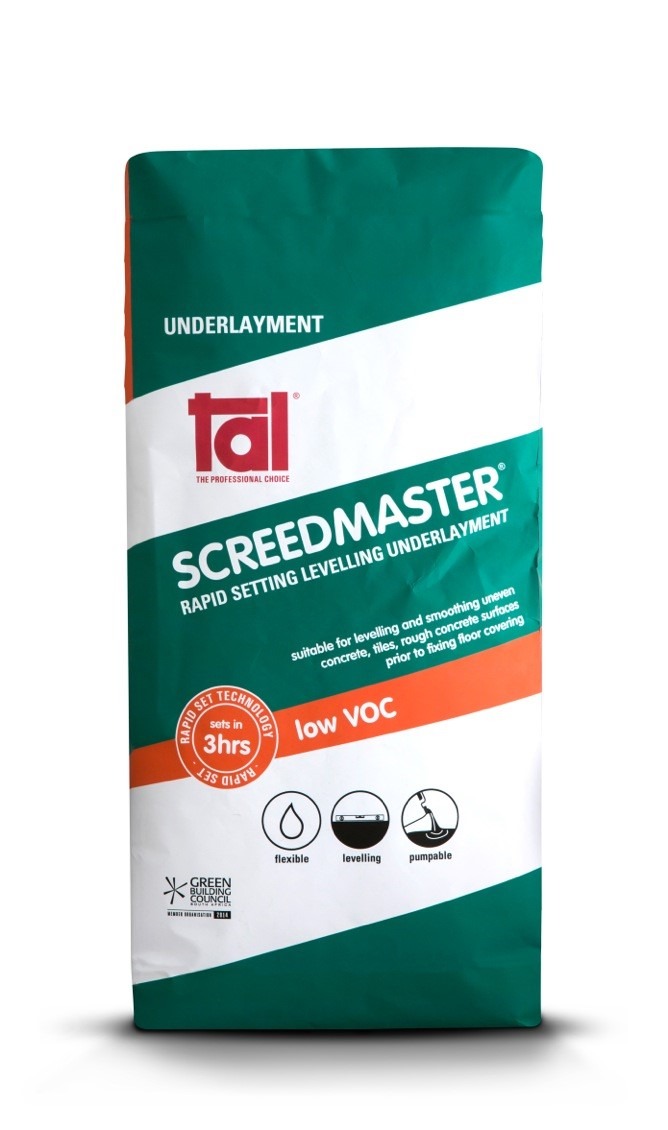
TAL Screedmaster and TAL Superscreed SL are compatible with most commonly used adhesives and soft floor finishes, as well as with hardwood flooring, laminates, tiles and athletic flooring.
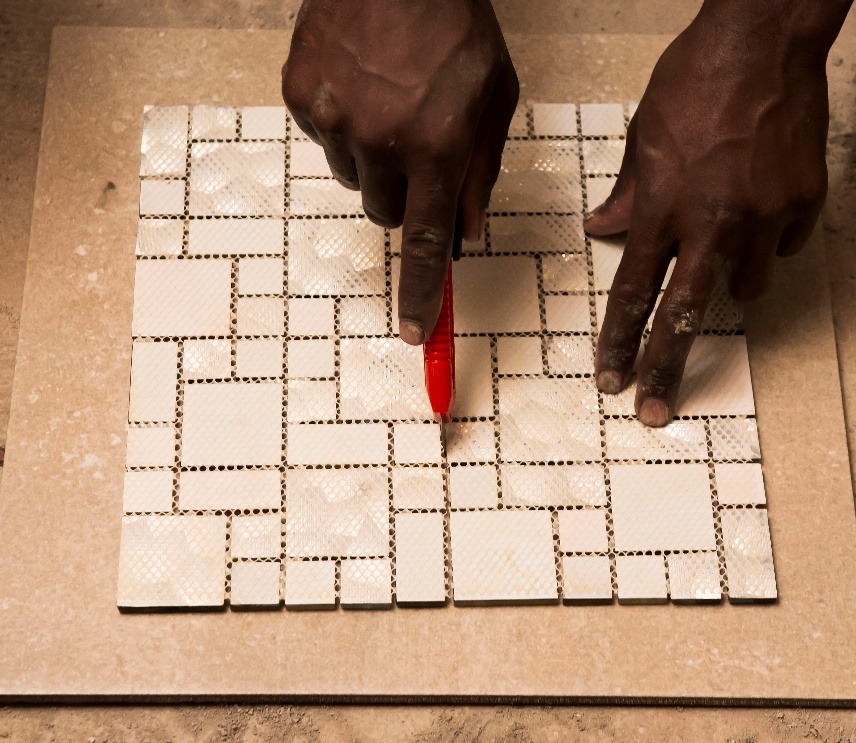
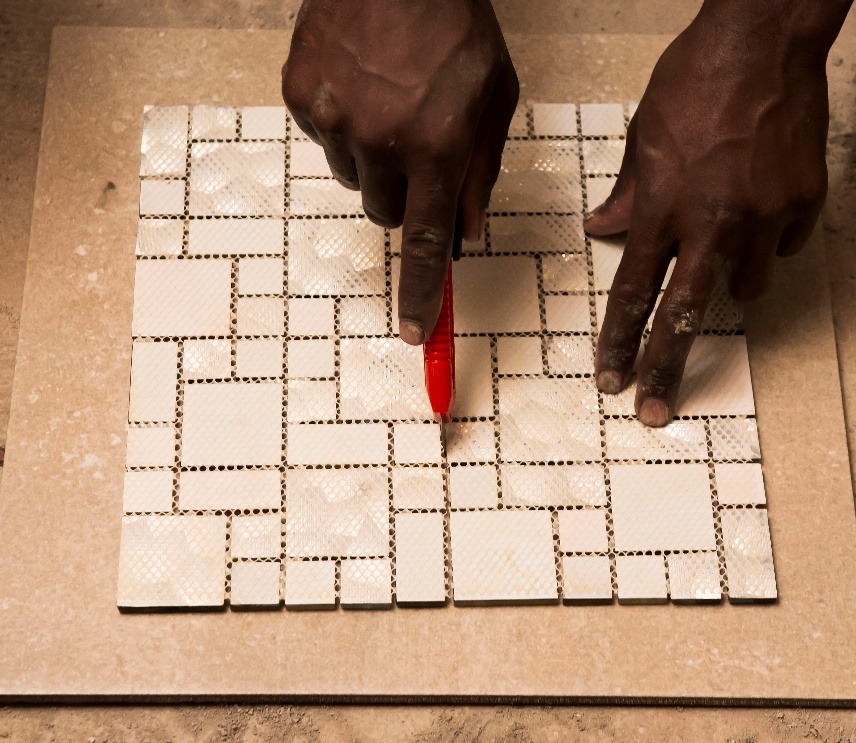
Step 2. In the meantime, plan the layout of the mosaic sheets and cut them to fit around the waste.
Tip: For enhanced flexibility and water resistance, it is recommended that the adhesive water mix be replaced with TAL BOND. This is important in installation areas that will be exposed to water, heat and humidity. Add TAL MOSAICFIX to the liquid and mix well to a creamy, lump-free consistency. Let it stand for three minutes and stir again.
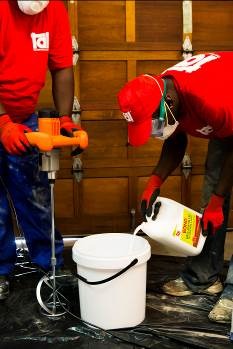
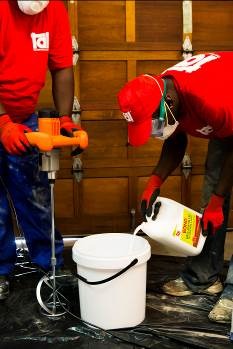
Step 3. Once mixed well, apply the adhesive to the surface in a solid bed of 4 mm to 6 mm, working in small areas of a square metre at a time.
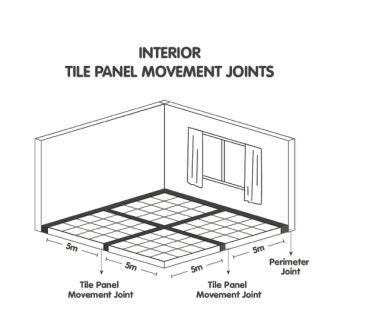
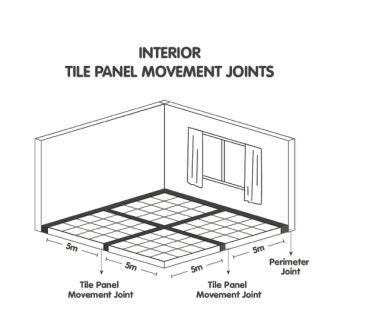
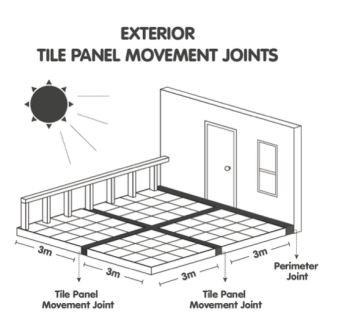
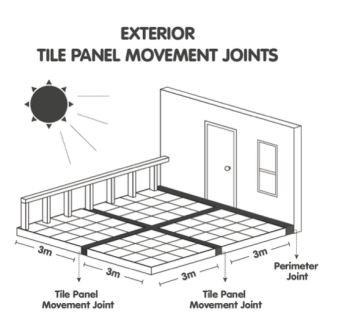
When using large format tiles (a tile with the length of at least one edge equal to/greater than 600mm, or a facial area greater than 3500cm²) there will be a smaller number of grout joints, compared with the same area of normal format tiling. As a result, less stress (movement) can be accommodated at tile joints.
Considering a wood-look tile installation? Give us a call or send usan email and we’ll give the right advice, no matter how big or small your tile installation: 0860000 TAL (825) or [email protected]. If this TAL Talk blog post interested you, you may want to take a look at this TAL Talk blog post: The 101 on wood-look tiles.
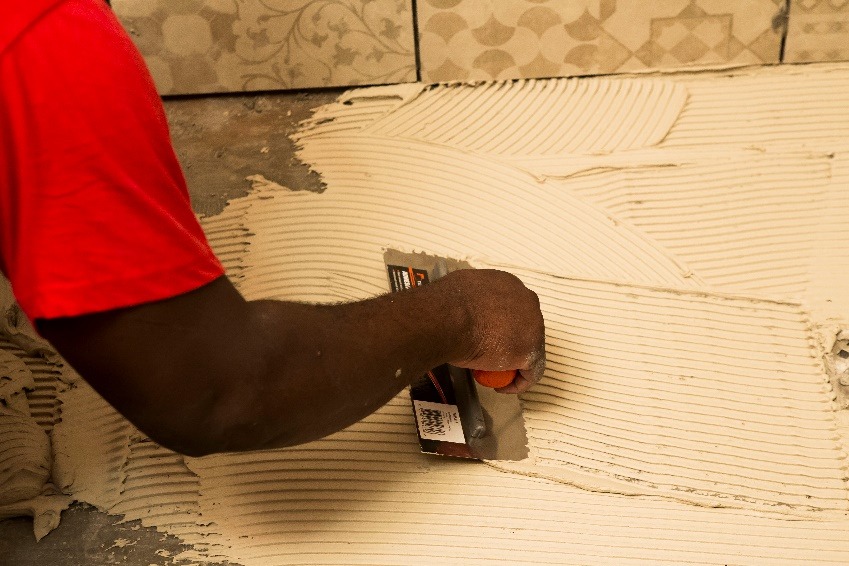
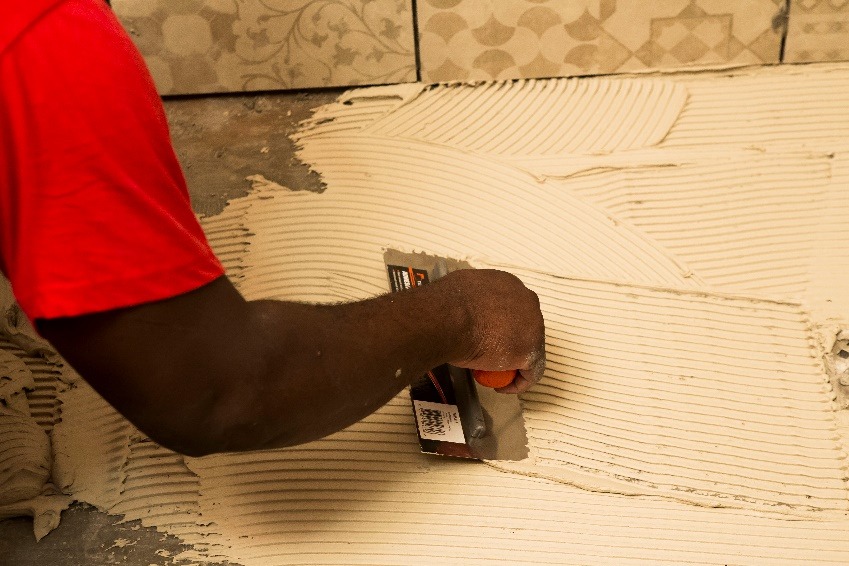
Step 4. Bed the mosaics immediately, pressing them firmly into the adhesive. Use a wooden beating block or rubber grouting float to tap them in and create a level surface. Using tile spacers between the individual mosaic sheets will maintain the joints
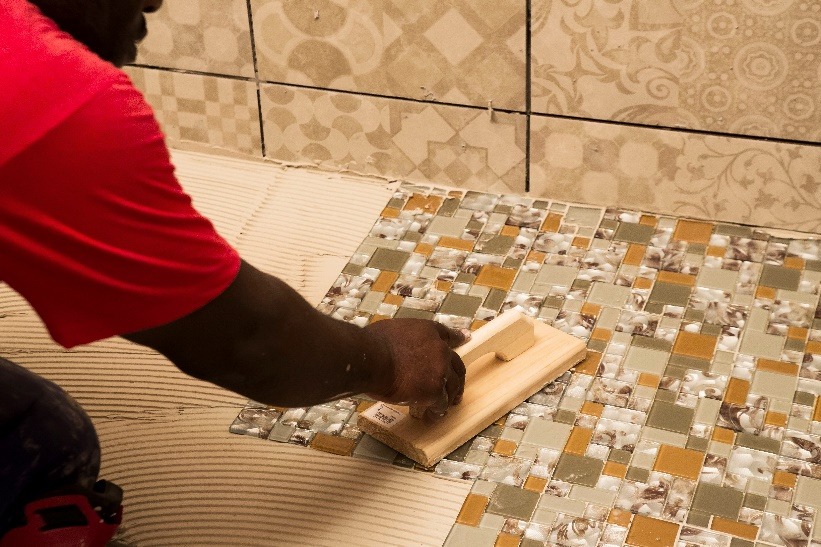
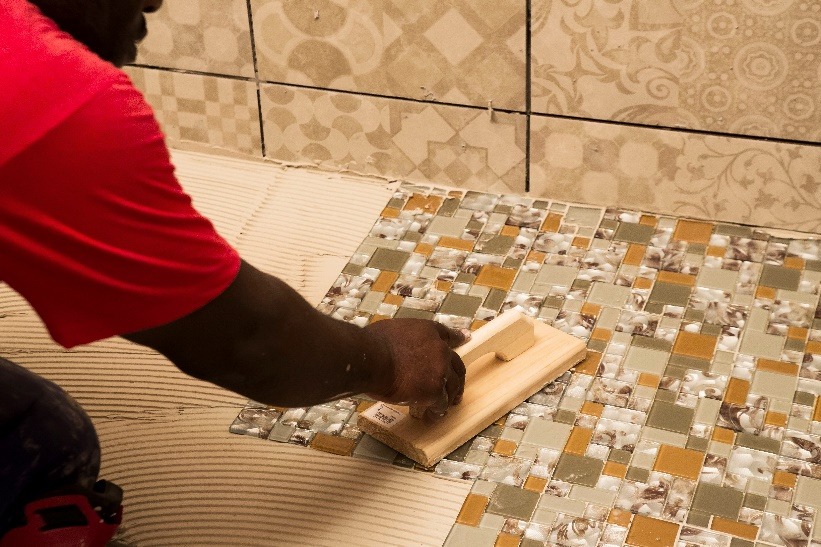
Step 5. Allow the adhesive to squeeze through the joints between the mosaics to form the grout and, if necessary, fill in any low areas in the joints with extra adhesive.
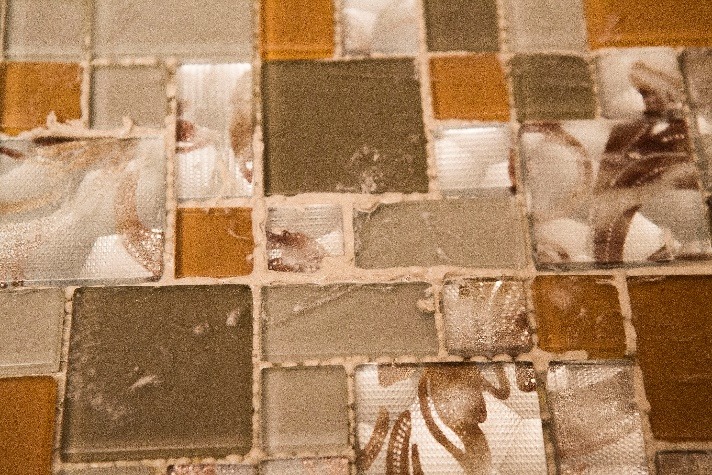
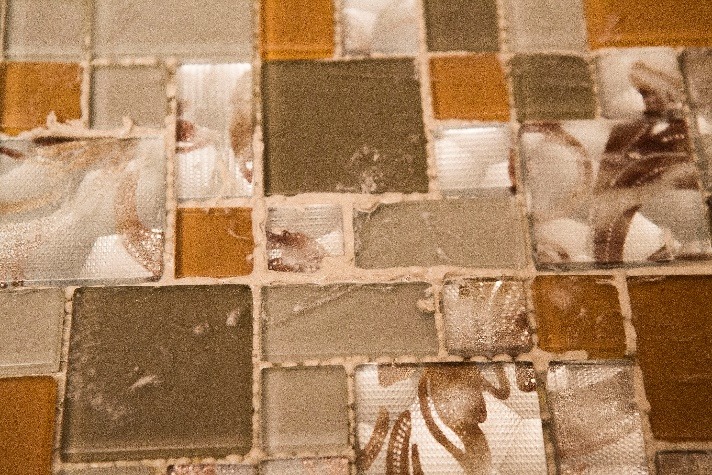
Step 6. Clean the excess adhesive off the face of the mosaics gently with a lightly dampened sponge, and leave to dry for a few hours.Work carefully to ensure that the mosaic installation is not disturbed, and that the glass mosaics are not scratched during application and cleaning. Polish the mosaic tiles with a dry cloth to remove any grout haze.
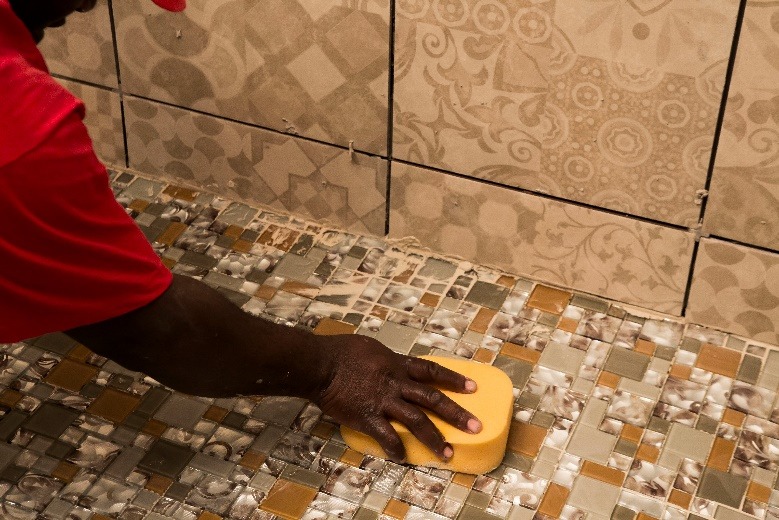
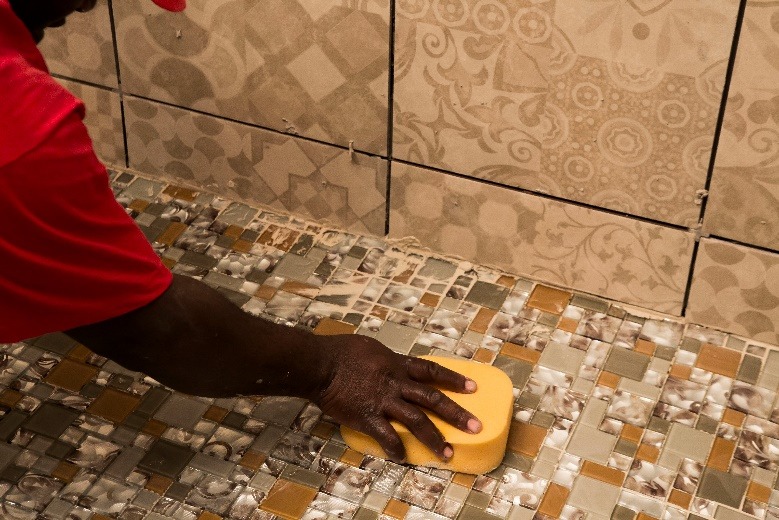
Step 7. Apply a silicone sealant to all the perimeter joints.


TAL MOSAICFIX is available in 20 kg and 5 kg bags from leading retail outlets.
Designed to be 100% compatible, using the TAL range of products ensures fully guaranteed multi-level tiling systems from a single source. TAL products are manufactured in South Africa to suit local climatic conditions.
If you are in any doubt, contact the TAL Technical Advisory Service on 0860 000 TAL (825), email [email protected]. Alternatively, employ the services of an experienced and skilled mosaic tiling contractor.
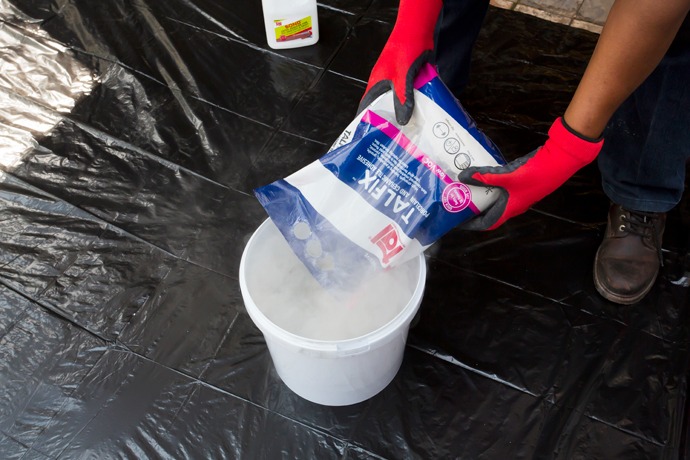
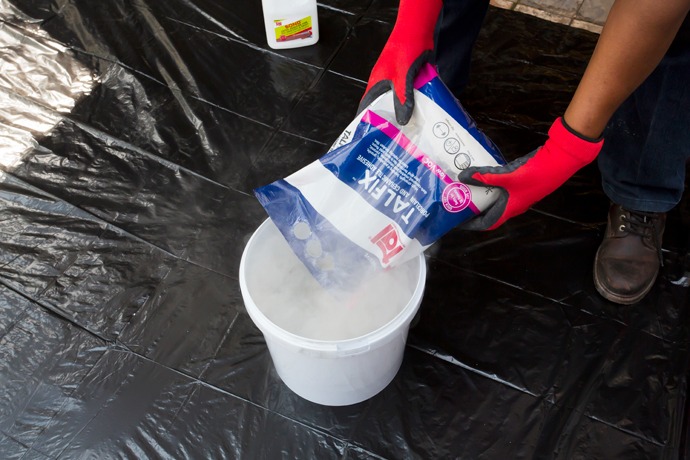
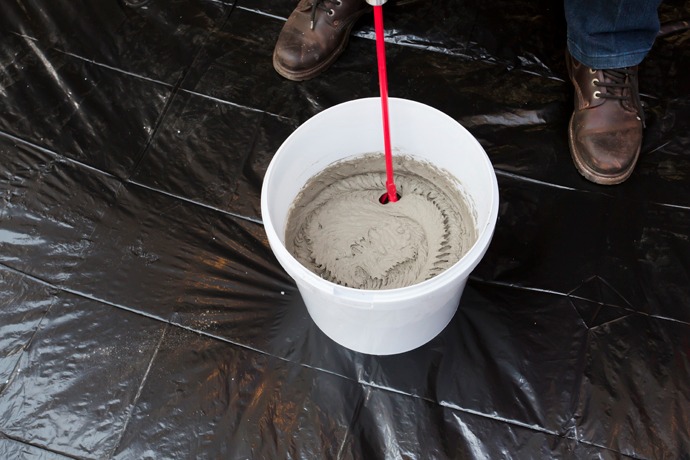
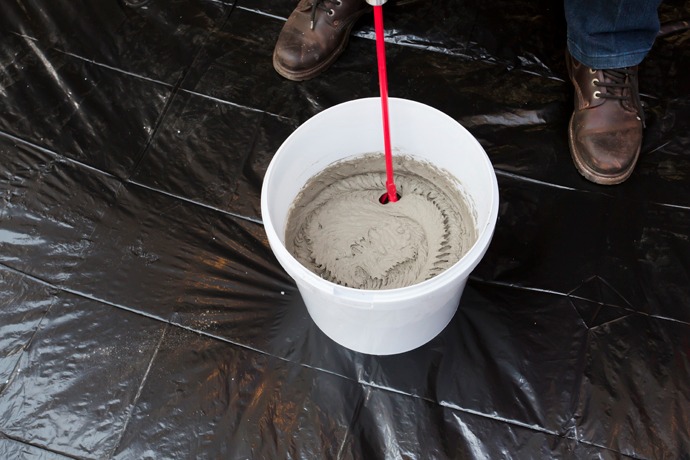
When replacing tiles, it is not always possible to apply the TALFIX directly to the floor, in which case apply the adhesive in a solid bed onto the back of the tile, ensuring complete coverage. Gently trace the notched side of a floor trowel through the adhesive to create ‘ridges’.
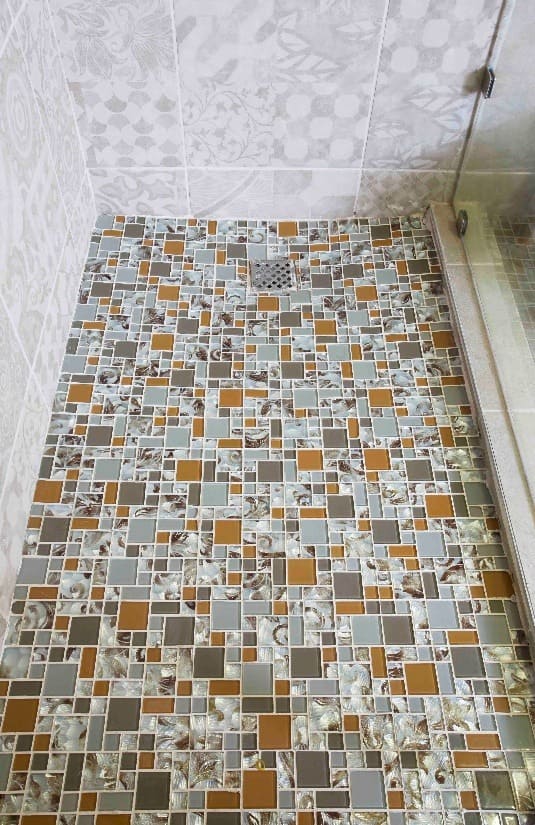
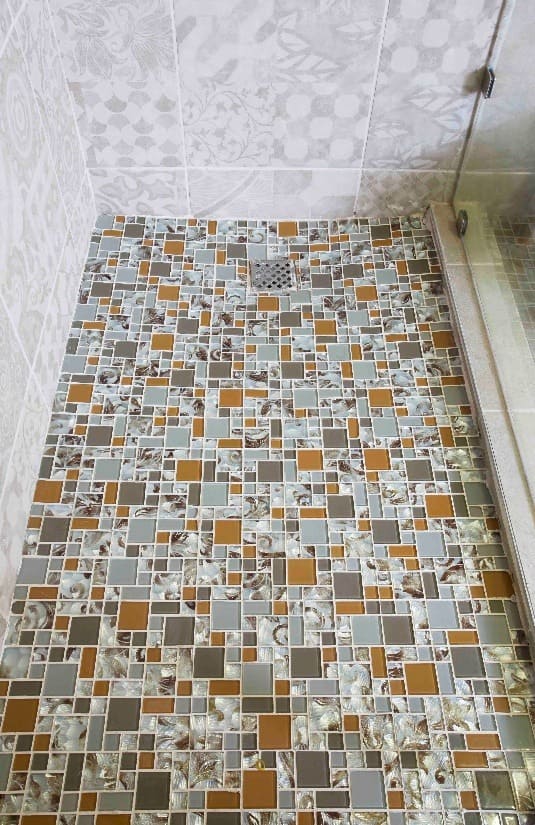
Adhesive system
When tiling onto existing tiles, it is important to only use a quick- or rapid-setting adhesive, as the existing tiles will present a dense, impervious surface, and standard-setting adhesives will take longer to dry. Too early trafficking of newly-installed tiles before the adhesive has set sufficiently can result in hollow-sounding or loose tiles.
Use TAL Tile-To-Tile quick-setting adhesive for tiling onto interior surface beds. When tiling onto suspended slabs and for external installations mix the TAL Tile-To-Tile with TAL Bond, replacing the water in the mix. Alternatively, TAL Bond Powder can be added to the adhesive mixing water.
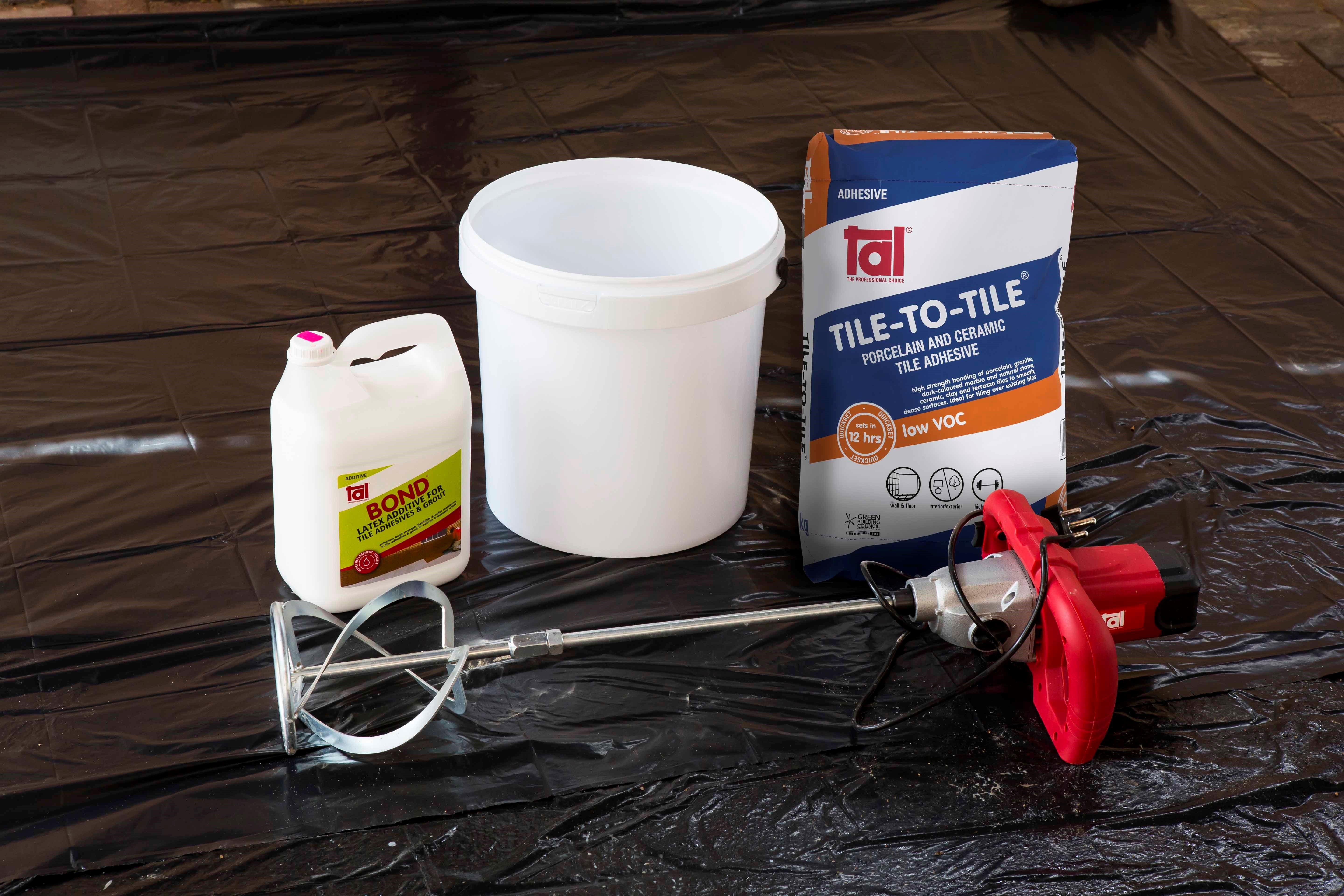
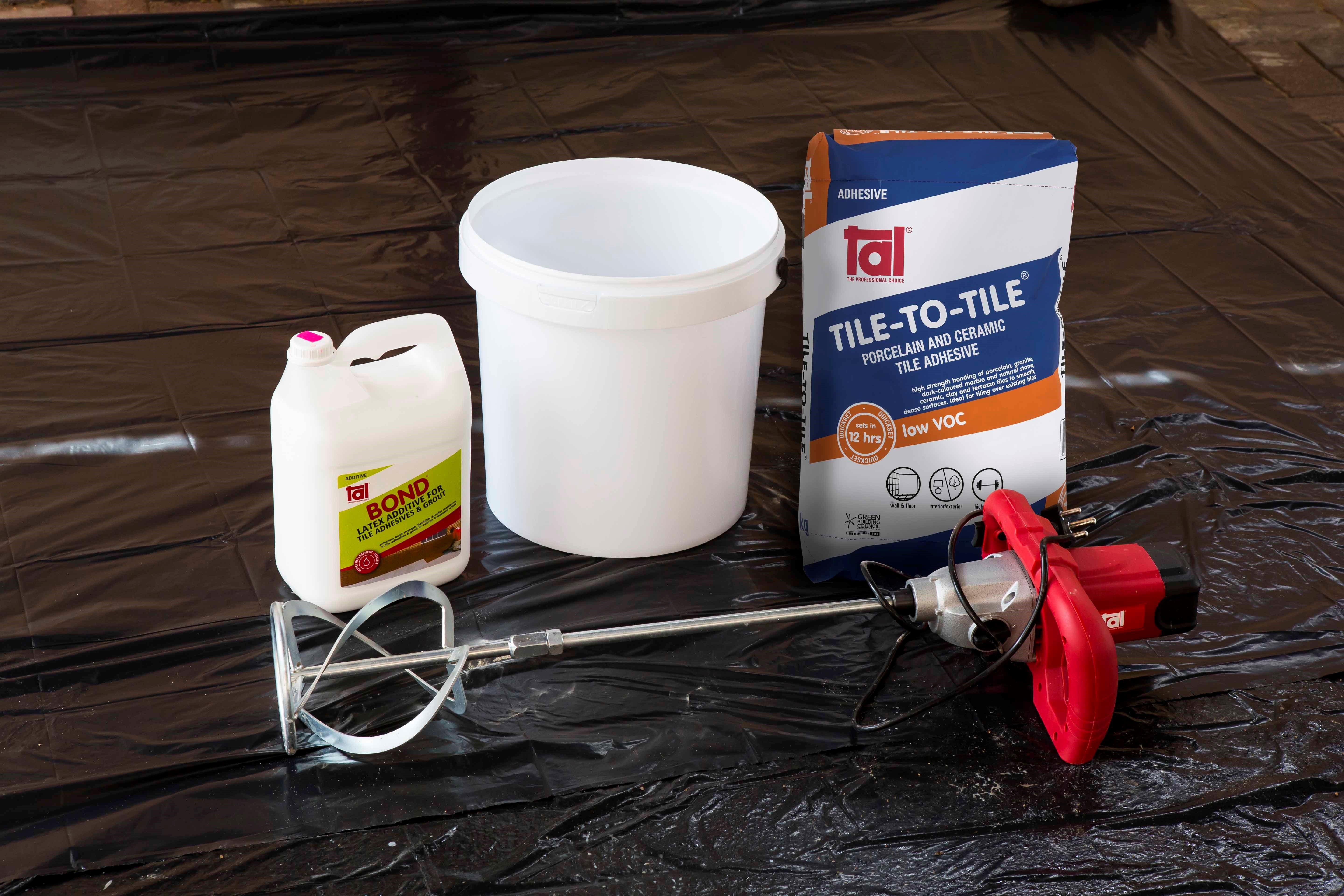
Ensure that there is a solid bed of adhesive at least 6 mm thick beneath each tile.
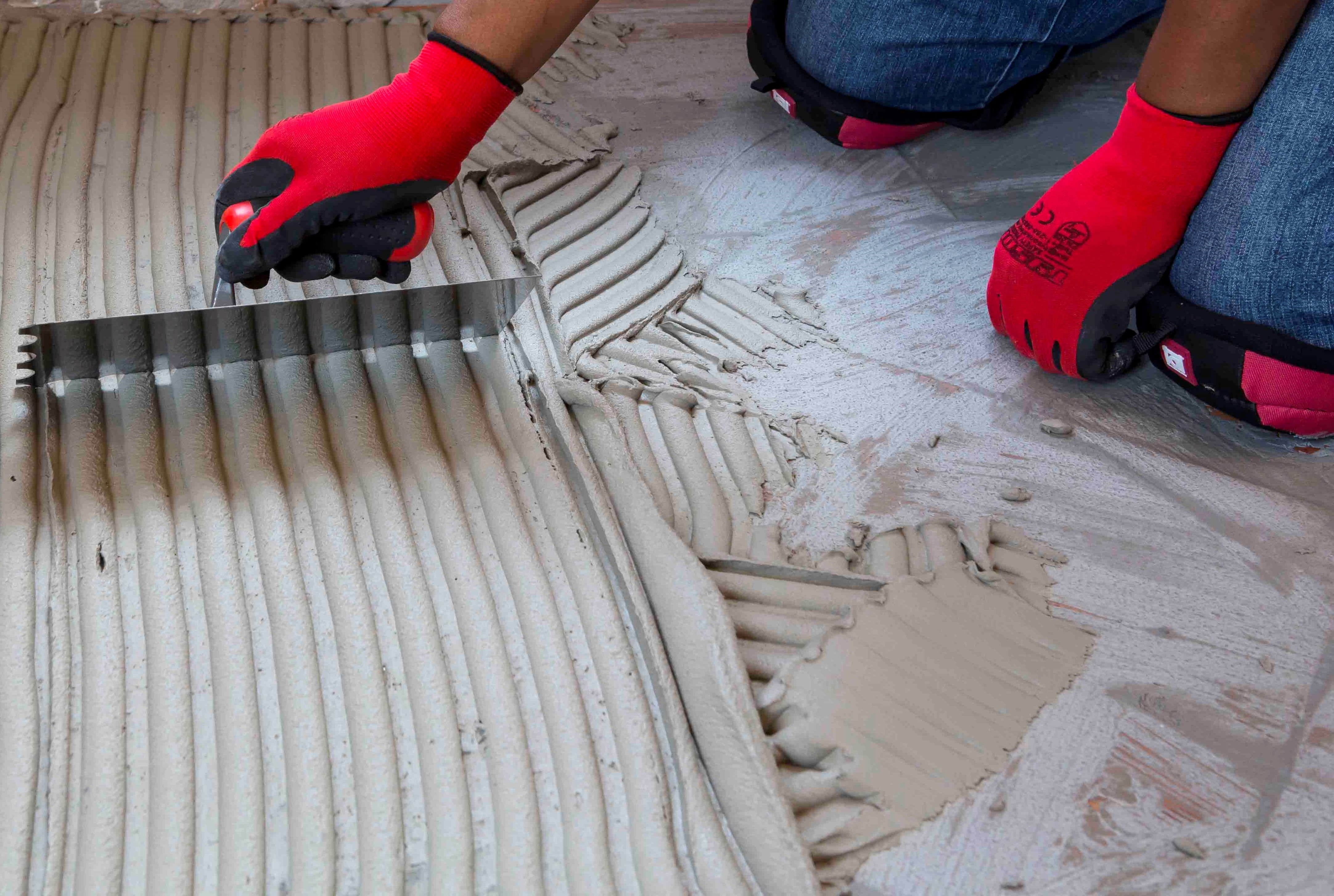
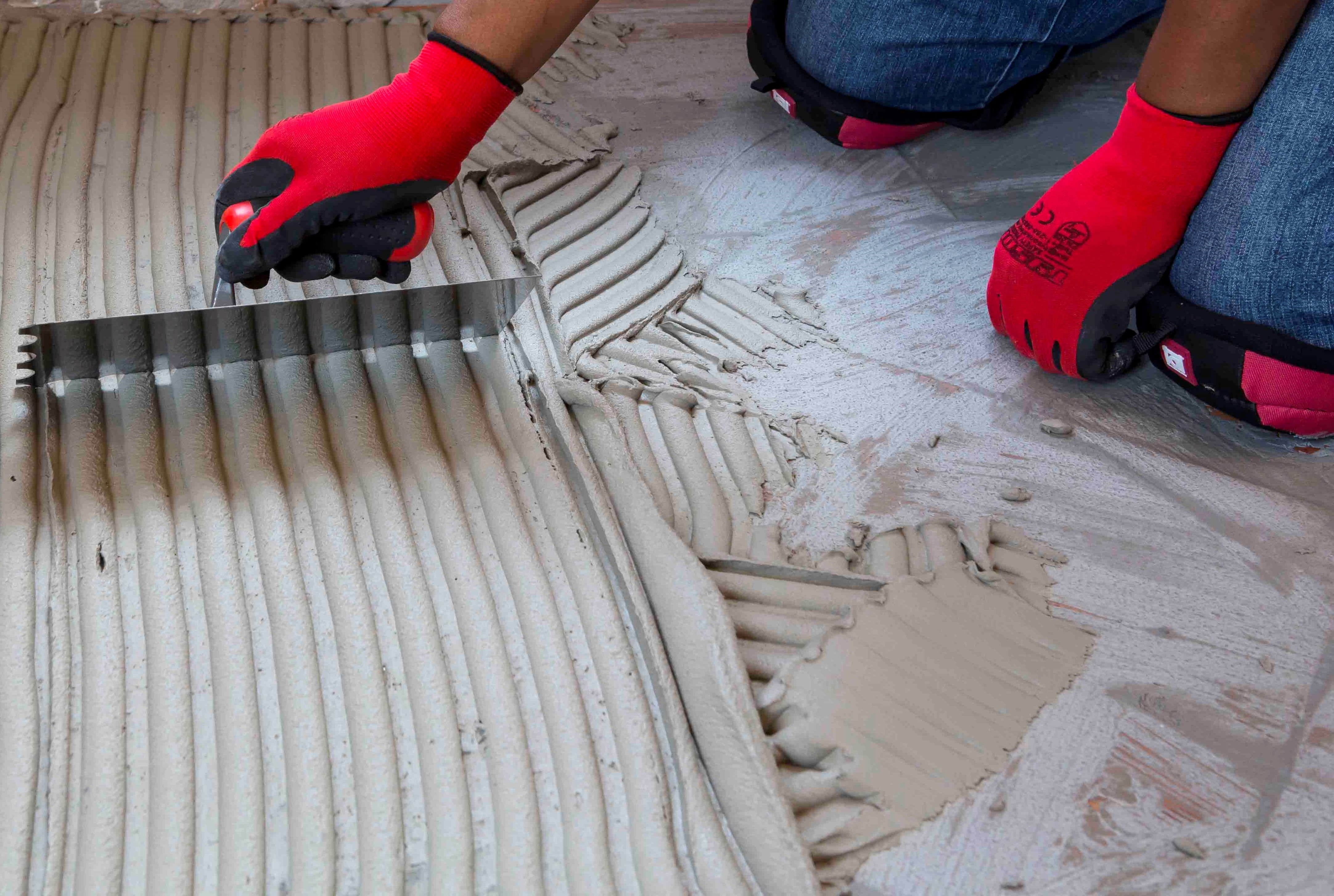
Back buttering with a thin coat of adhesive may also be required when using large-format tiles to ensure full contact with the adhesive bed.
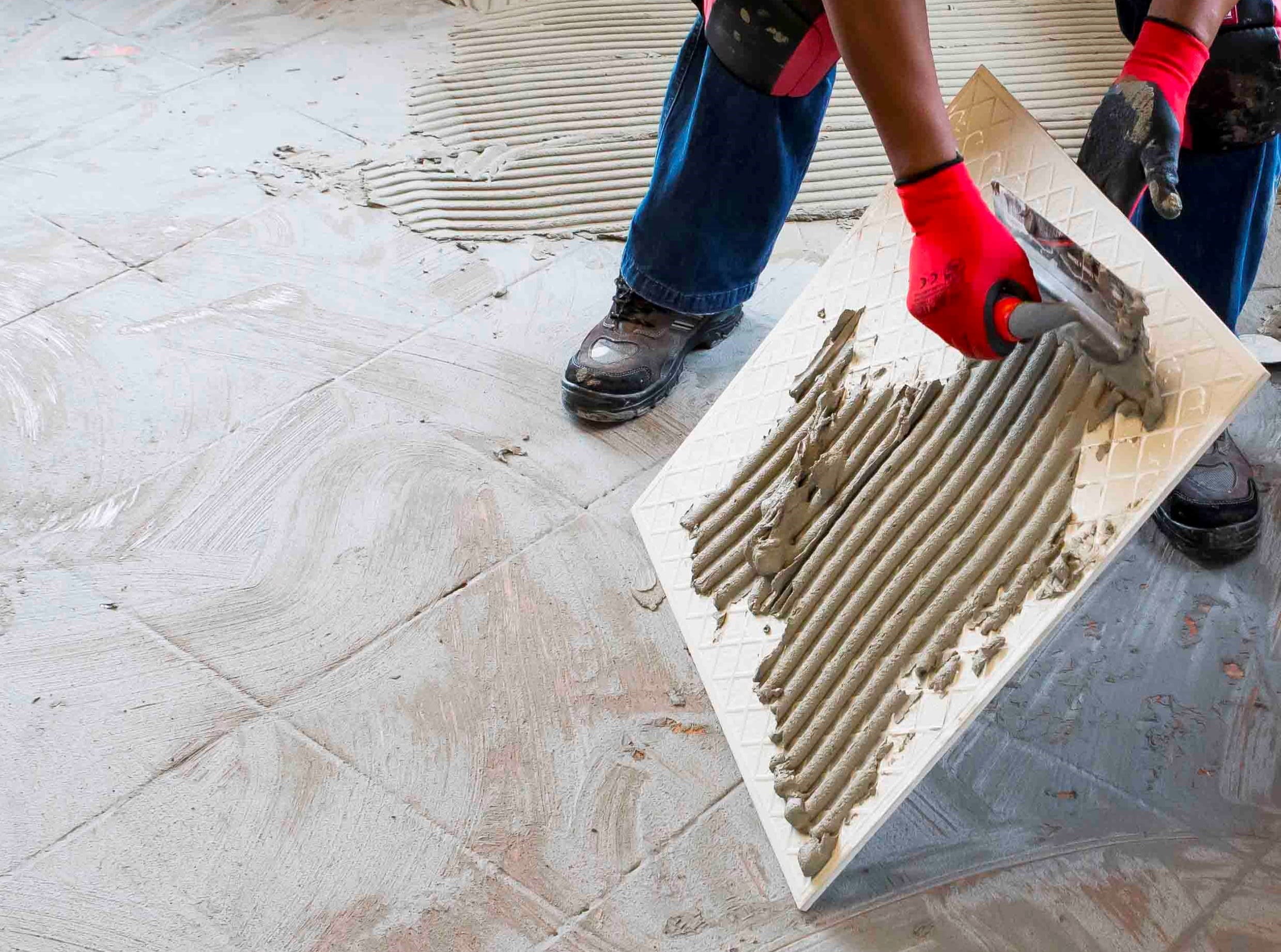
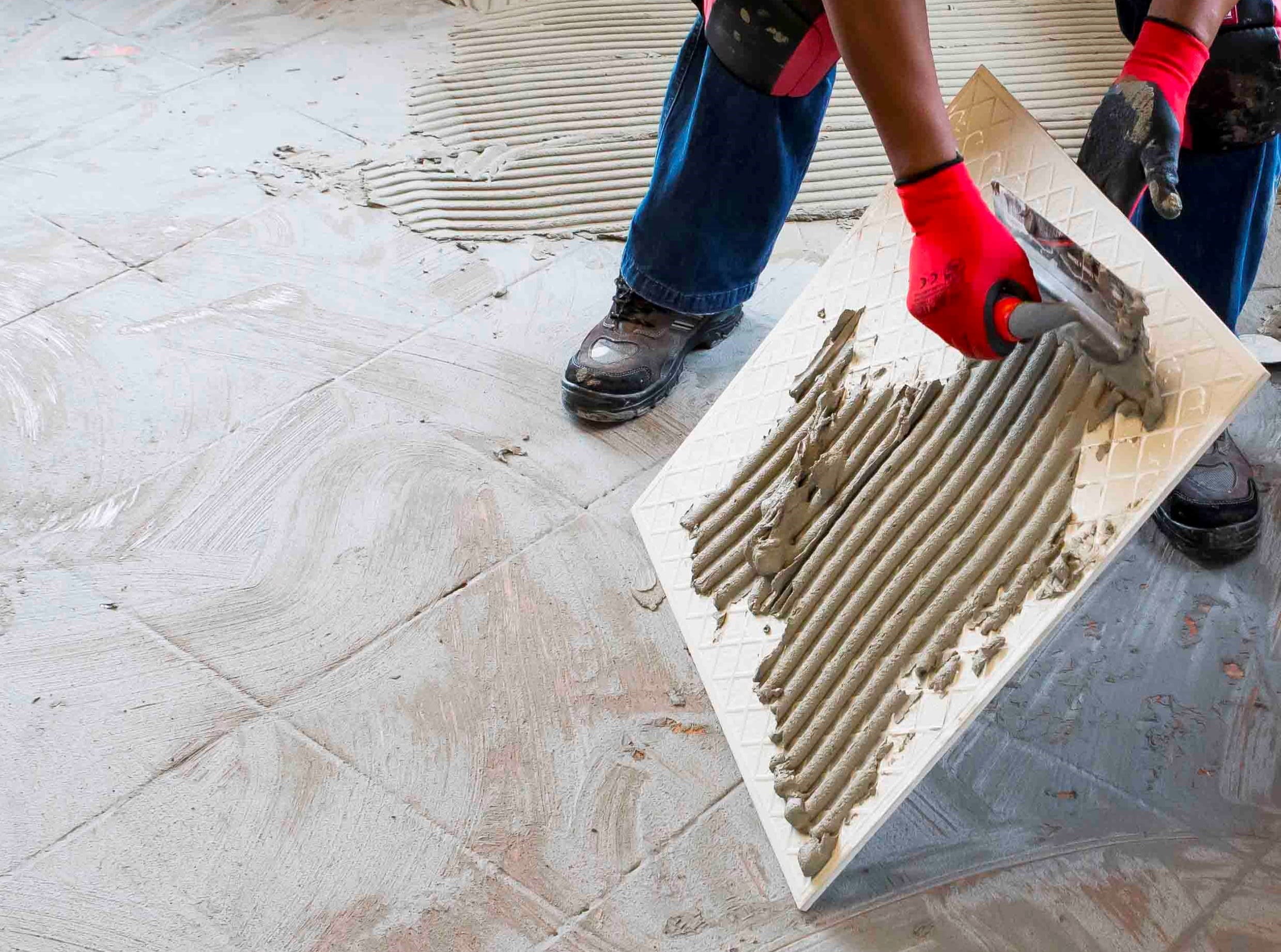
Grouting
Grouting should not be carried out until the adhesive has set sufficiently to prevent the tile installation from being disturbed during the grouting operation (always refer to the adhesive packaging for setting times). When using TAL TAL Tile-To-Tile, allow a minimum of six hours before grouting.
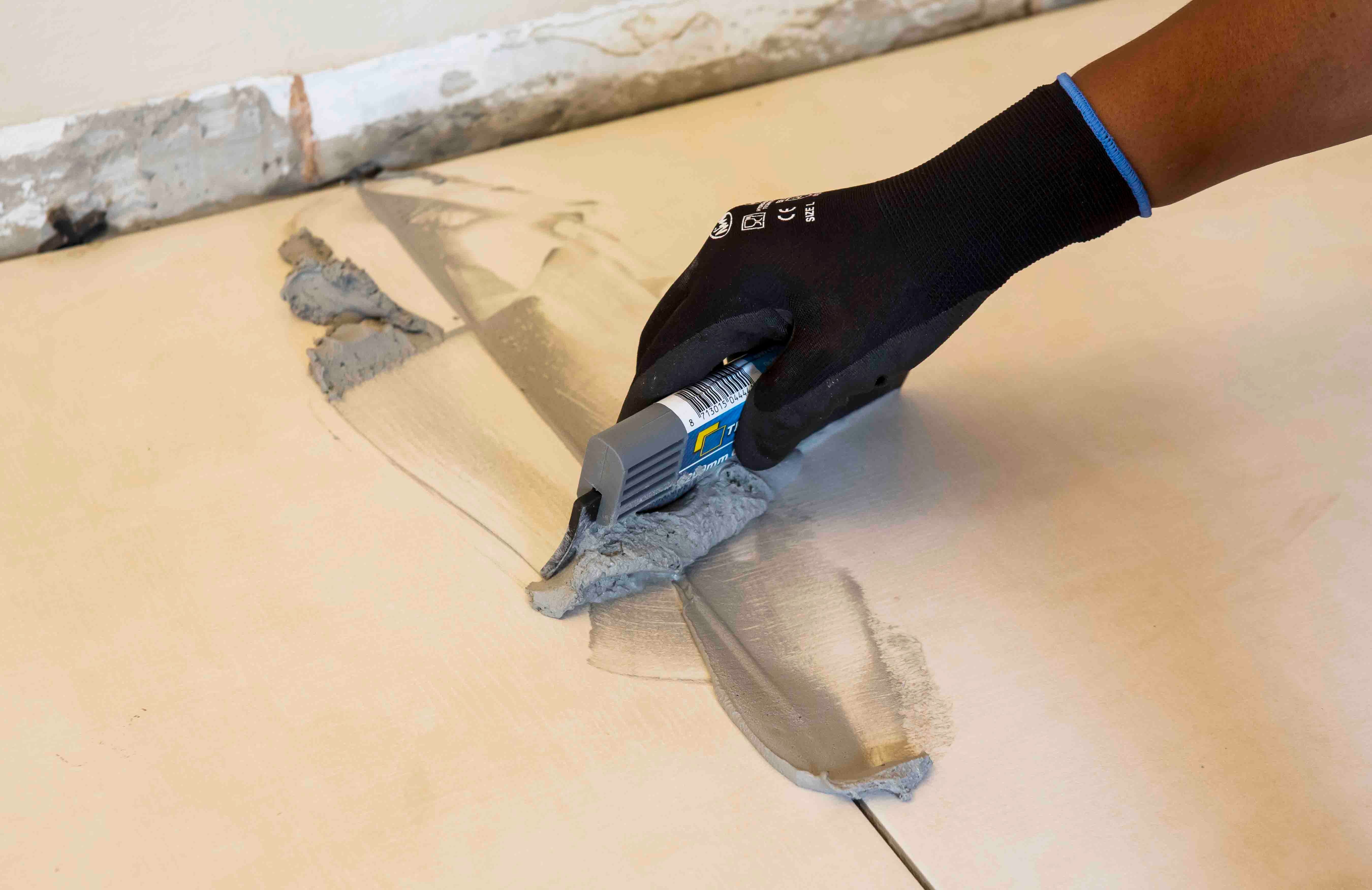
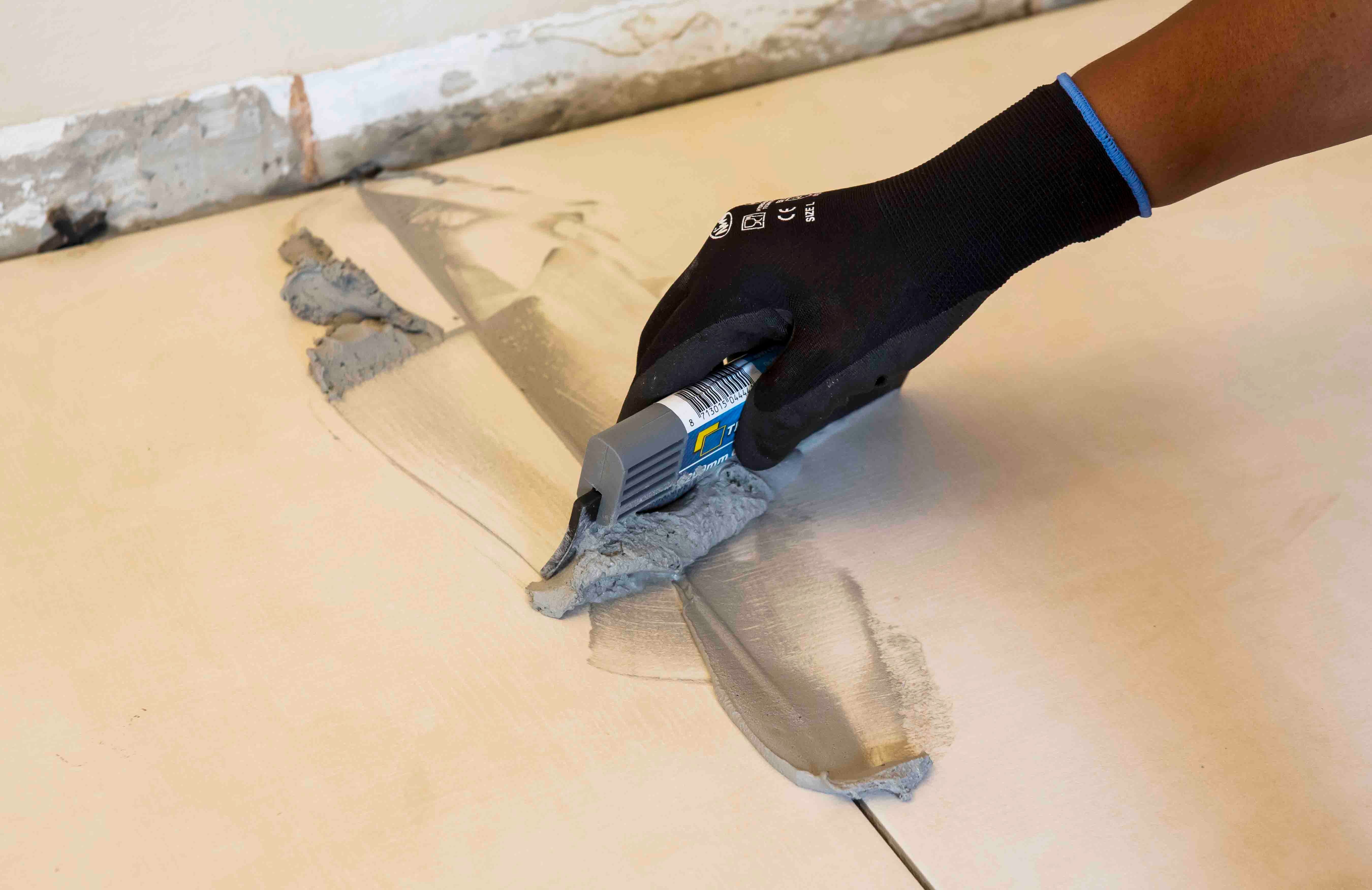
For interior surface beds, use TAL Wall & Floor Grout for filling tile joints up to 8 mm wide. TAL Quarry Grout can be used in wider joints up to 25 mm wide. On suspended slabs and for external installations, replace the water in the grout mix with TAL Bond, or add TAL Bond Powder to the grout mixing water.
Particular care must be taken to clean the grout off the tile face before it hardens completely. This is especially important when an additive such as TAL Bond or TAL Bond Powder has been used. A tile sample should be tested beforehand to ensure that no grout is absorbed through the glaze or into the tile body, thereby staining the tiles permanently.
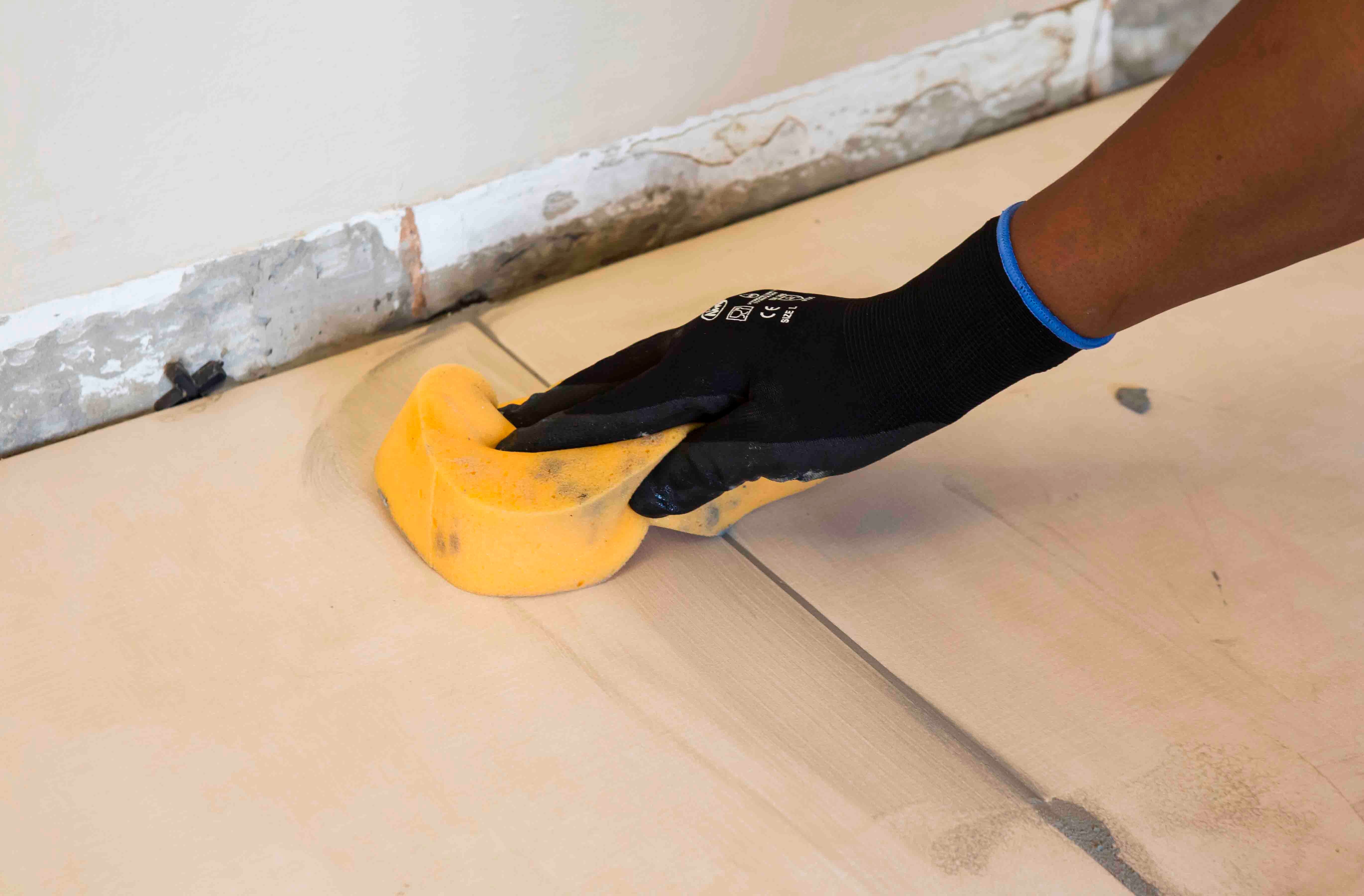
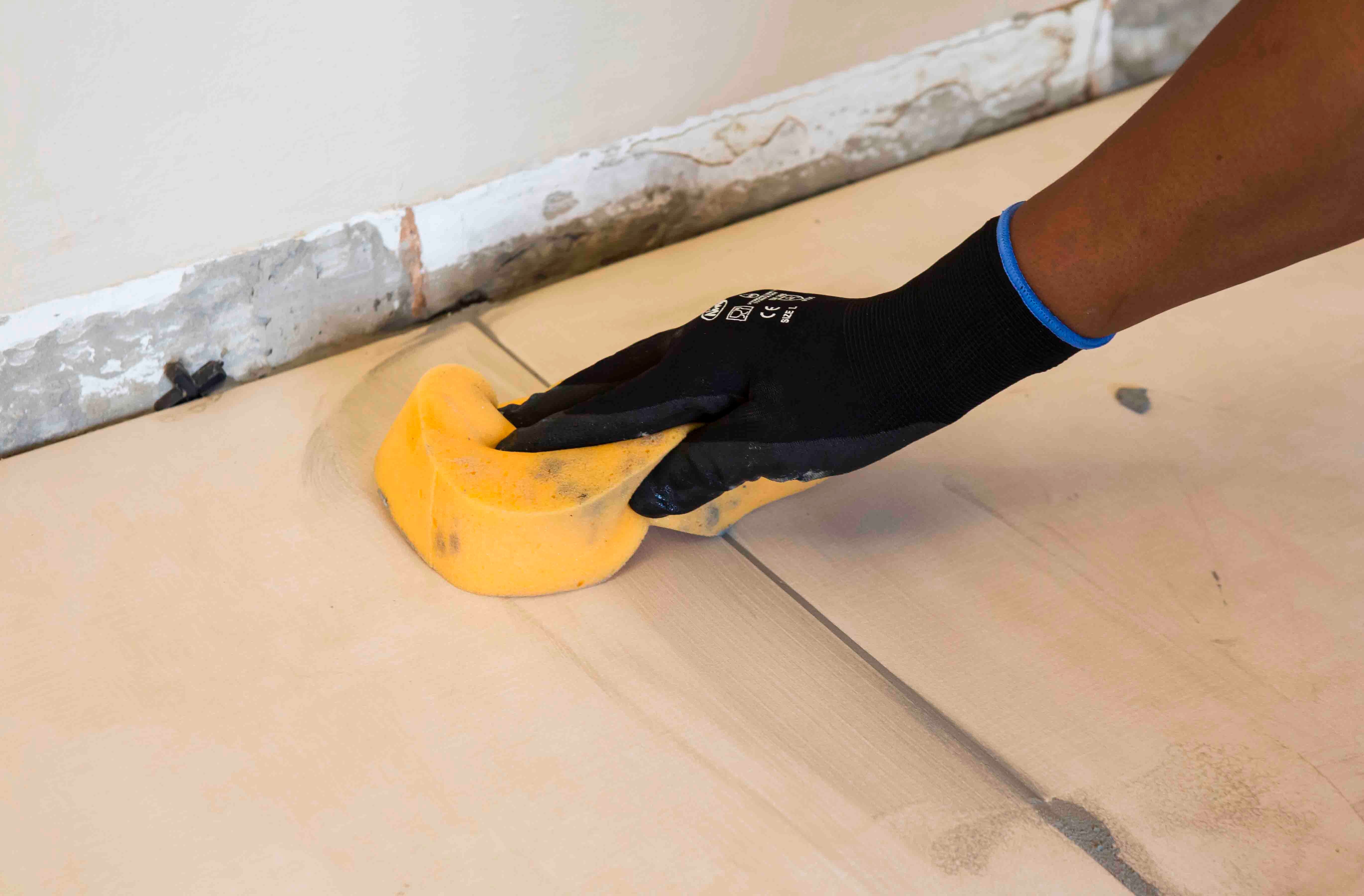
Movement joints
The lack of movement joints in tile installations is a major cause of tile failure. When tiling over existing tiles, the existing structural and movement joints must be maintained in the new tile installation. The movement joints should be at least 5 mm wide and extend through the adhesive and both tile layers.
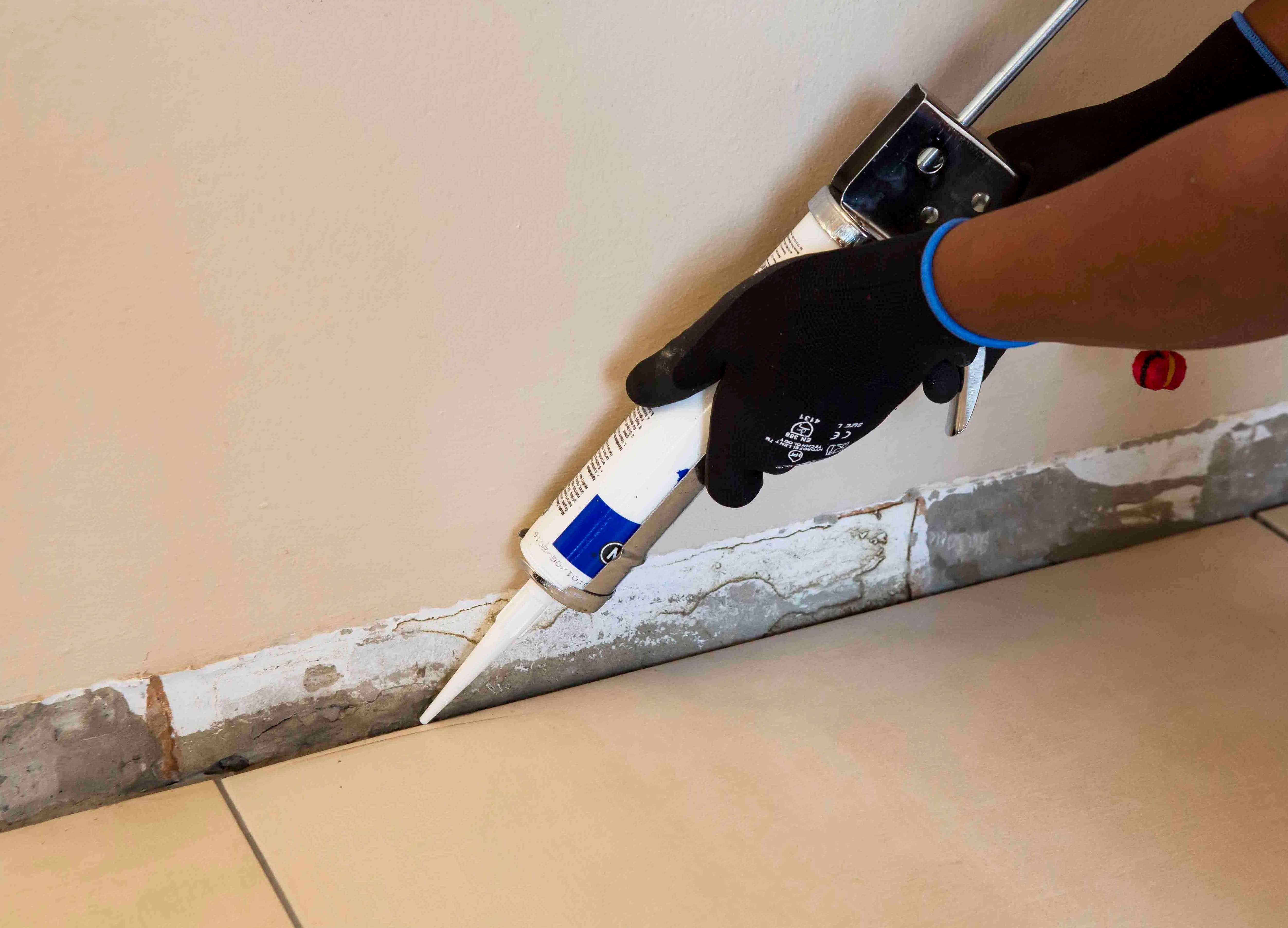
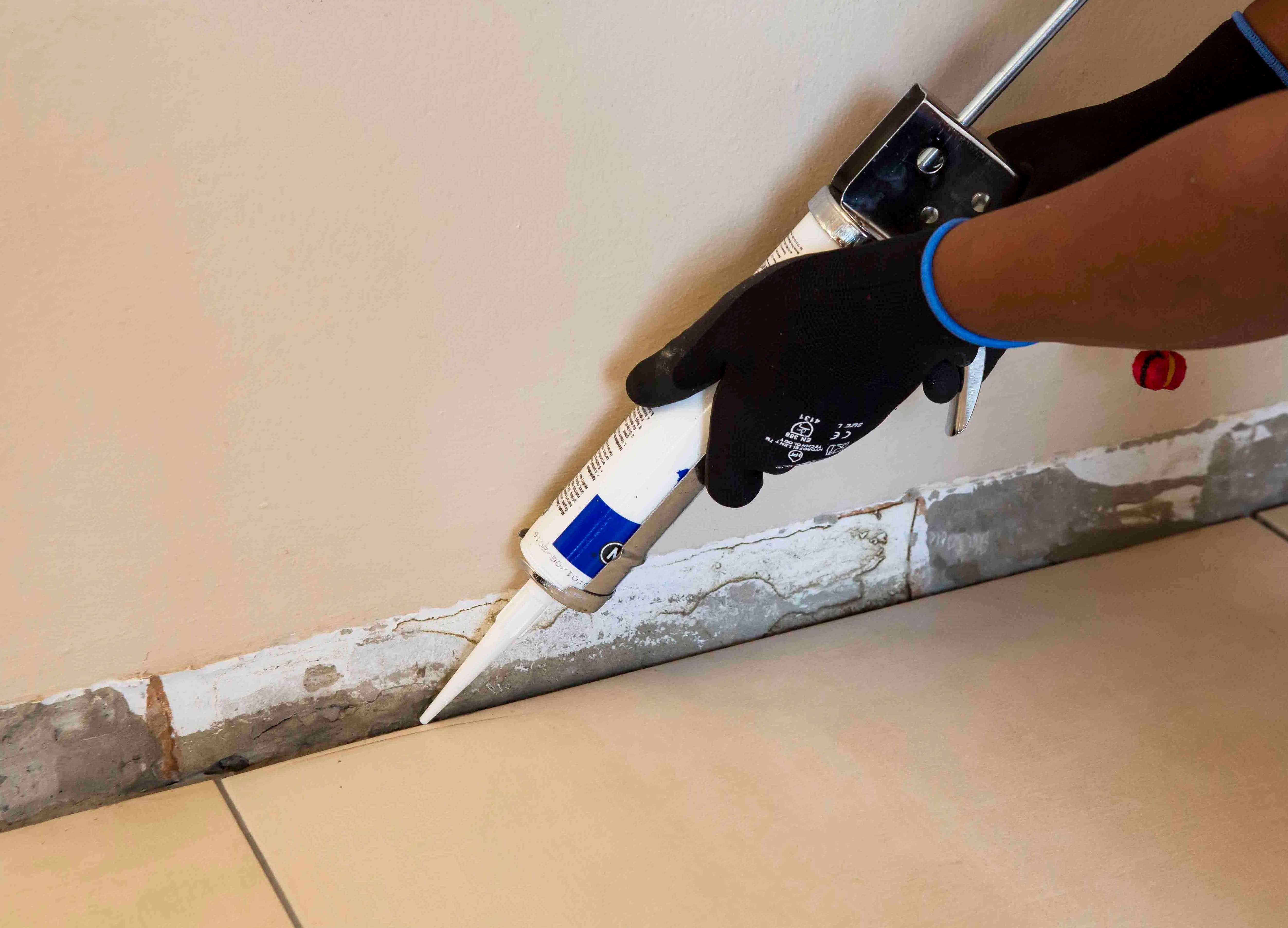