Top 5 tips on how to choose an industrial flooring applicator
Installing an industrial flooring system, whether on a new floor or the refurbishment of an existing floor, can be a complex project to undertake. Experience teaches us that a correctly prepared substrate, combined with a flooring system that is suited for the relative service environment, will far surpass the life expectancy of that bonded covering.
The choice of applicator is equally important as the choice of finish, as industrial flooring systems should be installed by trained and skilled flooring contractors who take into consideration the technical aspects of installation. These include product and substrate temperatures, ambient conditions, and keeping the installation environment free of dust, birds and bugs to avoid damage during installations and curing. Factors like exposure to direct sunlight, mixing methods, open times and pot life of the specific product being used should all be considered before placement of a system on site. An experienced applicator will also use the correct and industry prescribed equipment and tools to complete the installation.
Our top 5 tips to choosing an applicator are:
- Get a project specification
Get a correct specification for the flooring project, then look for an applicator who is experienced in the required floor covering. If you’re not sure about which flooring system is best suited to your needs, speak to our technical advice centre for advice and a specification for the correct fit for purpose floor covering for your application.
- Request a quote in writing
Request a quote in writing. It is important to get a signed and detailed quote that explains the exact services being rendered before you begin the project. Consider:
- Is the removal or mechanical abrading of the existing floor covering included in the service (if a renovation project).
- Is priming and the correct substrate preparation included in the quote
- Source multiple quotes
The choice of applicator is equally important as the choice of finish, as industrial flooring systems should be installed by trained and skilled flooring contractors who take into consideration the technical aspects of installation. These include product and substrate temperatures, ambient conditions, and keeping the installation environment free of dust, birds and bugs to avoid damage during installations and curing. Factors like exposure to direct sunlight, mixing methods, open times and pot life of the specific product being used should all be considered before placement of a system on site. An experienced applicator will also use the correct and industry prescribed equipment and tools to complete the installation.
Our top 5 tips to choosing an applicator are:
- Get a project specification
Get a correct specification for the flooring project, then look for an applicator who is experienced in the required floor covering. If you’re not sure about which flooring system is best suited to your needs, speak to our technical advice centre for advice and a specification for the correct fit for purpose floor covering for your application.
- Request a quote in writing
Request a quote in writing. It is important to get a signed and detailed quote that explains the exact services being rendered before you begin the project. Consider:
- Is the removal or mechanical abrading of the existing floor covering included in the service (if a renovation project)
- Is priming and the correct substrate preparation included in the quote
- Source multiple quotes
Source multiple quotes then carefully read and compare the offering, relative to the scope of work required for the site. This quote should be item specific, and the work as quoted should fall in line with the manufacturers prescribed guidelines for installation, and specification.
- Get references of project referrals
References or project referrals should be considered along with an understanding of how long it will take to conduct the required work. Variables like program changes or delays by other trades should also be factored in to ensure the contractors availability to successfully complete work. Ask for samples of colours and finishes of the floor covering, so that you know exactly what the final product will look like.
- Determine the financial requirements
Determine how much you will be required to pay upfront and what guarantees you will have on the work. A standard set of industry terms and conditions should be applied and agreed upon before payments are made. These could include deposits, progress payments and practical completion certificates for final payment etc.
Specifying and installation of a multi-level industrial flooring system by an experienced applicator, may be a higher cost at the outset, but the downstream savings are clear. Beyond the cost of the initial installation, the costs of remedial repair are exponential, as is the time factor when required to remove the failed flooring system.
For project specifications for your industrial flooring project, contact the TAL Technical Advice Centre.
Source multiple quotes then carefully read and compare the offering, relative to the scope of work required for the site. This quote should be item specific, and the work as quoted should fall in line with the manufacturers prescribed guidelines for installation, and specification.
- Get references of project referrals
References or project referrals should be considered along with an understanding of how long it will take to conduct the required work. Variables like program changes or delays by other trades should also be factored in to ensure the contractors availability to successfully complete work. Ask for samples of colours and finishes of the floor covering, so that you know exactly what the final product will look like.
- Determine the financial requirements
Determine how much you will be required to pay upfront and what guarantees you will have on the work. A standard set of industry terms and conditions should be applied and agreed upon before payments are made. These could include deposits, progress payments and practical completion certificates for final payment etc.
Specifying and installation of a multi-level industrial flooring system by an experienced applicator, may be a higher cost at the outset, but the downstream savings are clear. Beyond the cost of the initial installation, the costs of remedial repair are exponential, as is the time factor when required to remove the failed flooring system.
For project specifications for your industrial flooring project, contact the TAL Technical Advice Centre.
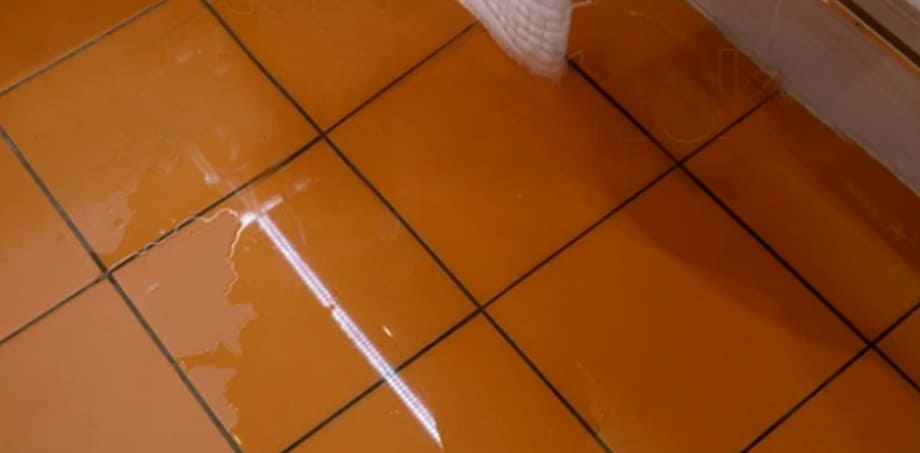
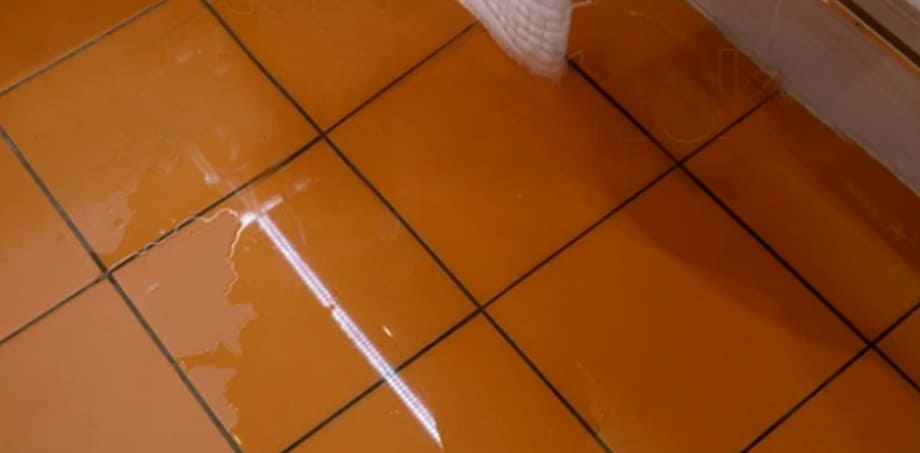
-
HOW MUCH WATER CAN A TILE ABSORB?
The structure of the tile and the way it has been manufactured, will determine how much water it can absorb.
-
Handmade terracotta tiles: are fired at low temperatures, resulting in the body of the tile being porous. This means it has a higher water absorption rate (about 15%) than say a ceramic or porcelain tile
-
Glazed ceramic tiles: are impervious to water because of their glazed finish; however, if there are undetected cracks in the glaze at the front (the ‘face’) of the tile, water may permeate through these cracks into the tile body (which isn’t glazed). This means that the back of the tile (termed the ‘base’ or the ‘biscuit’ of the tile) can absorb water.
-
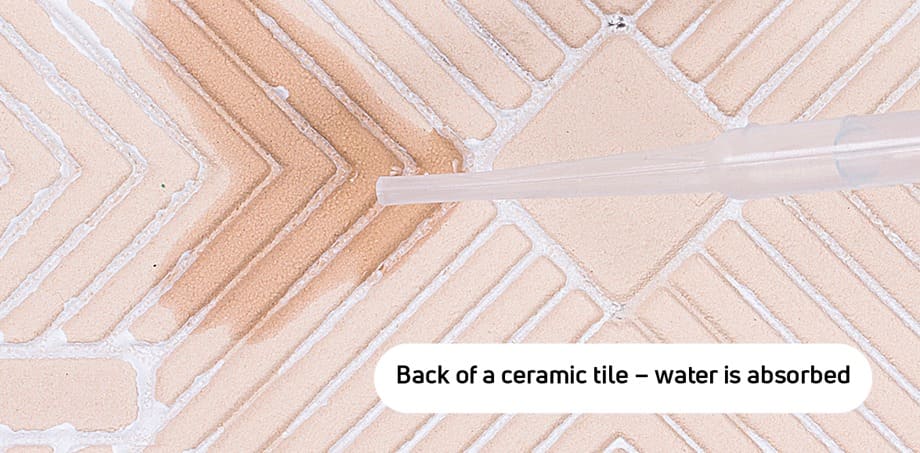
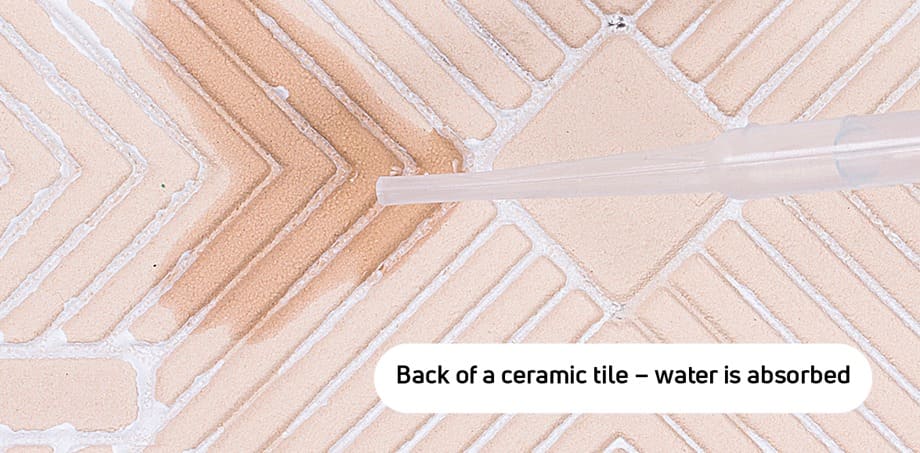
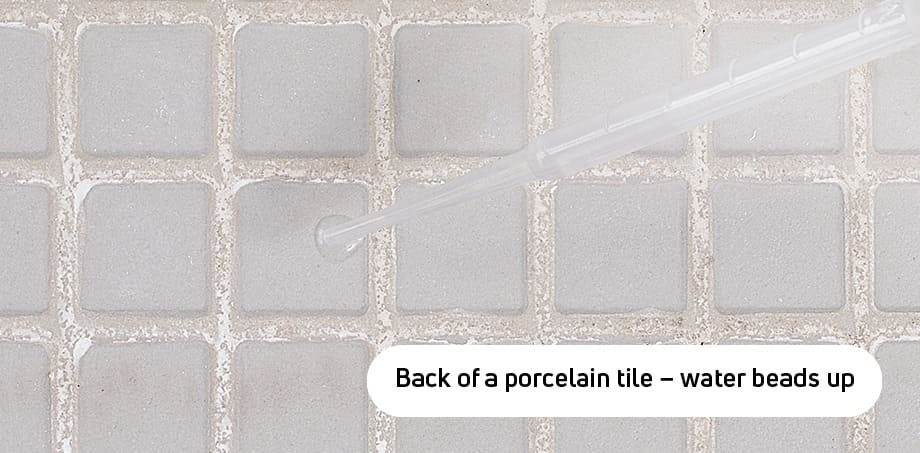
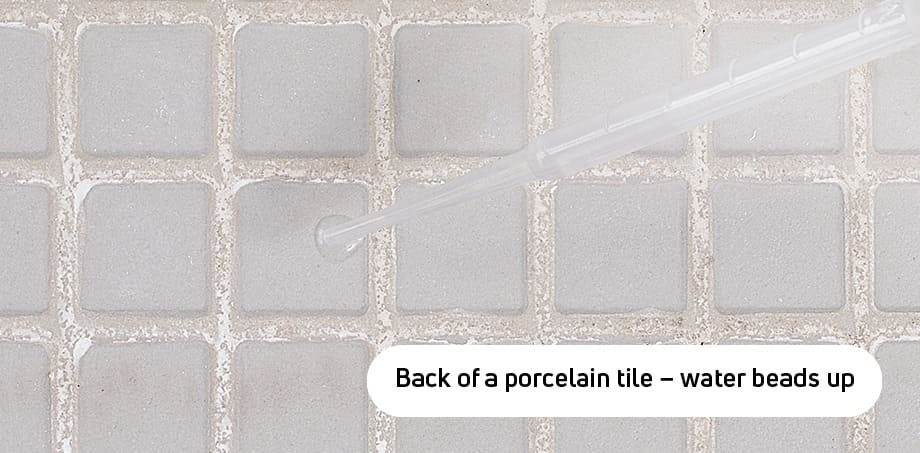
HOW TO DETECT THE PROBLEM!
If this happens, you will know your tiles are exposed to an excess of moisture:
The surface of a glazed tile is similar to a semi-transparent glass finish:
-
Should there be moisture ingress into the tile installation, the face of the tile, particularly light-coloured ceramic tiles with a transparent glaze, will change colour, and appear darker than the surrounding tiles.
What causes the problem?
Most instances of water absorption in tiles will take place in showers, bathrooms, kitchens, and outdoor areas. The reasons could be as follows:
-
The shower recess or balcony was not waterproofed before tiling.
-
Waterproofing compounds were applied incorrectly.
-
There was a leak in the water pipe behind tiling.
-
The floor water outlet is not draining water properly, and is now flooding.
-
There are cracks in the grout, or incorrectly applied grout which is not sealed.
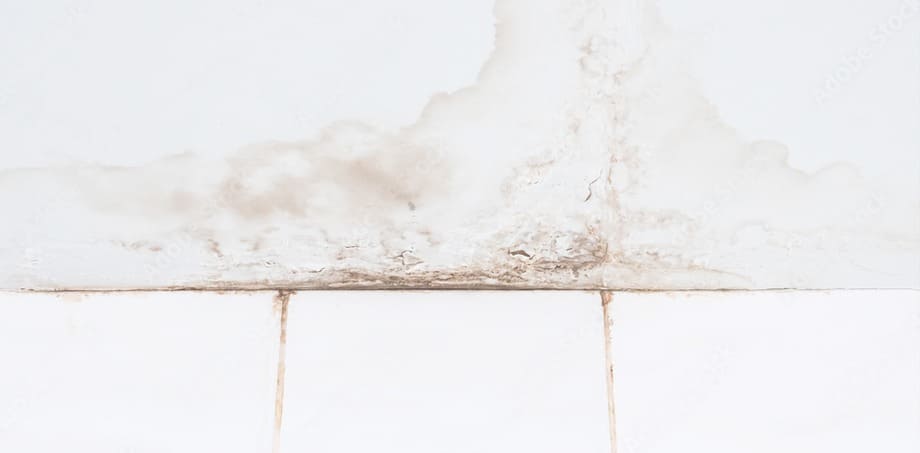
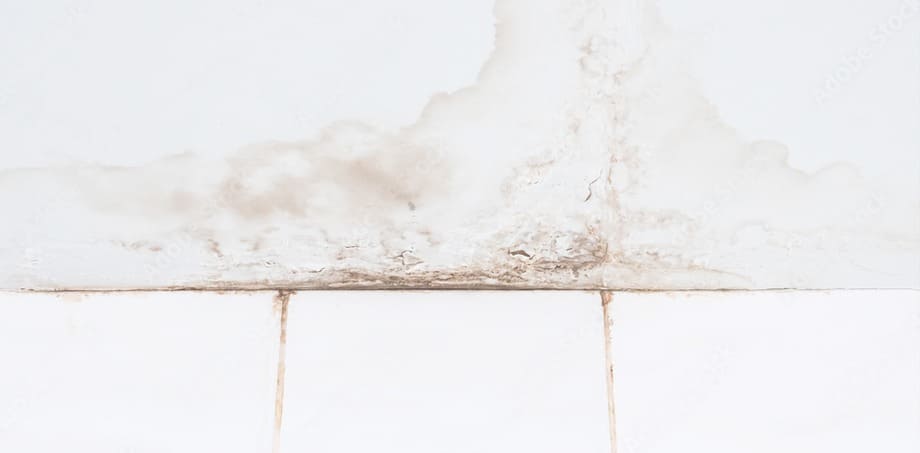
-
WHAT CAN I DO?
Attend to the water damage as soon as a problem is detected!
Water permeating through the grout and adhesive into the substrate can cause damp patches on adjacent walls or on the ceilings of rooms below the installation. There is also a risk of mould growth.
Follow these steps:1. Get a plumber in to determine if there is a leak in the pipe-work or taps:
- leakages must be repaired as soon as possible.
2. Consult a professional tiling contractor to determine if the problem is caused by:
- a lack of waterproofing
- failed waterproofing
- cracks in tile glaze
- cracked or soft grout
3. Should the wet area be tiled with porous tiles such as unglazed ceramics, or natural stones (travertine, slate, or marble), consider sealing the tiles with a suitable tile sealer.
4. Once the problems are rectified and the tiles are allowed to dry out, the dark shading will disappear.
- Porous tiles should be allowed to dry completely before being sealed.
- If you seal the tiles while they are still saturated with water, moisture could get trapped beneath the sealant, or prolong the drying-out process.
5. In extreme cases, especially if waterproofing has failed, the tiles will have to be removed and reinstalled. (See our article on How to waterproof a shower)
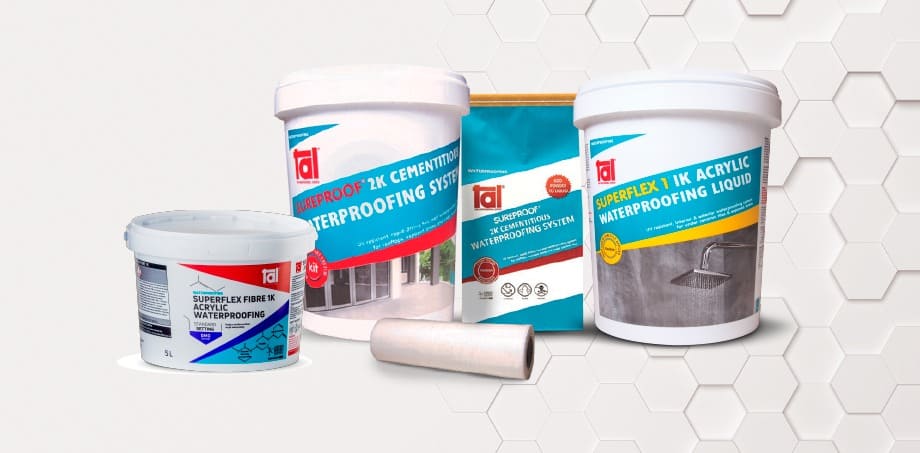
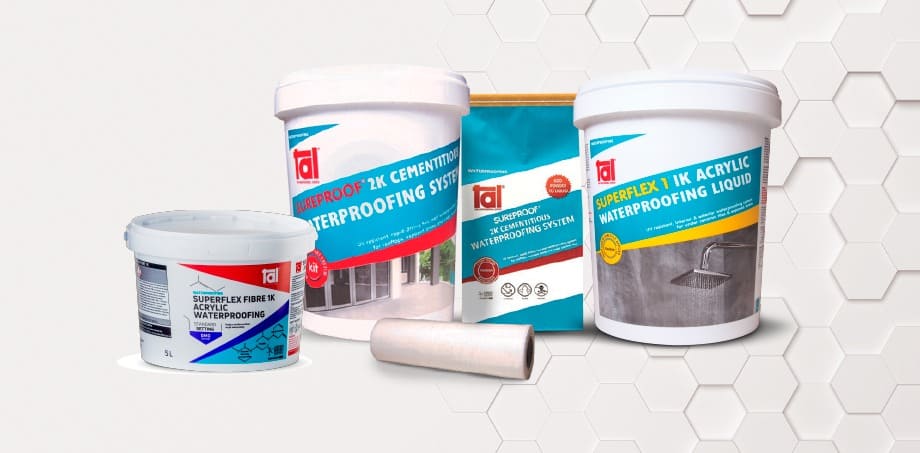
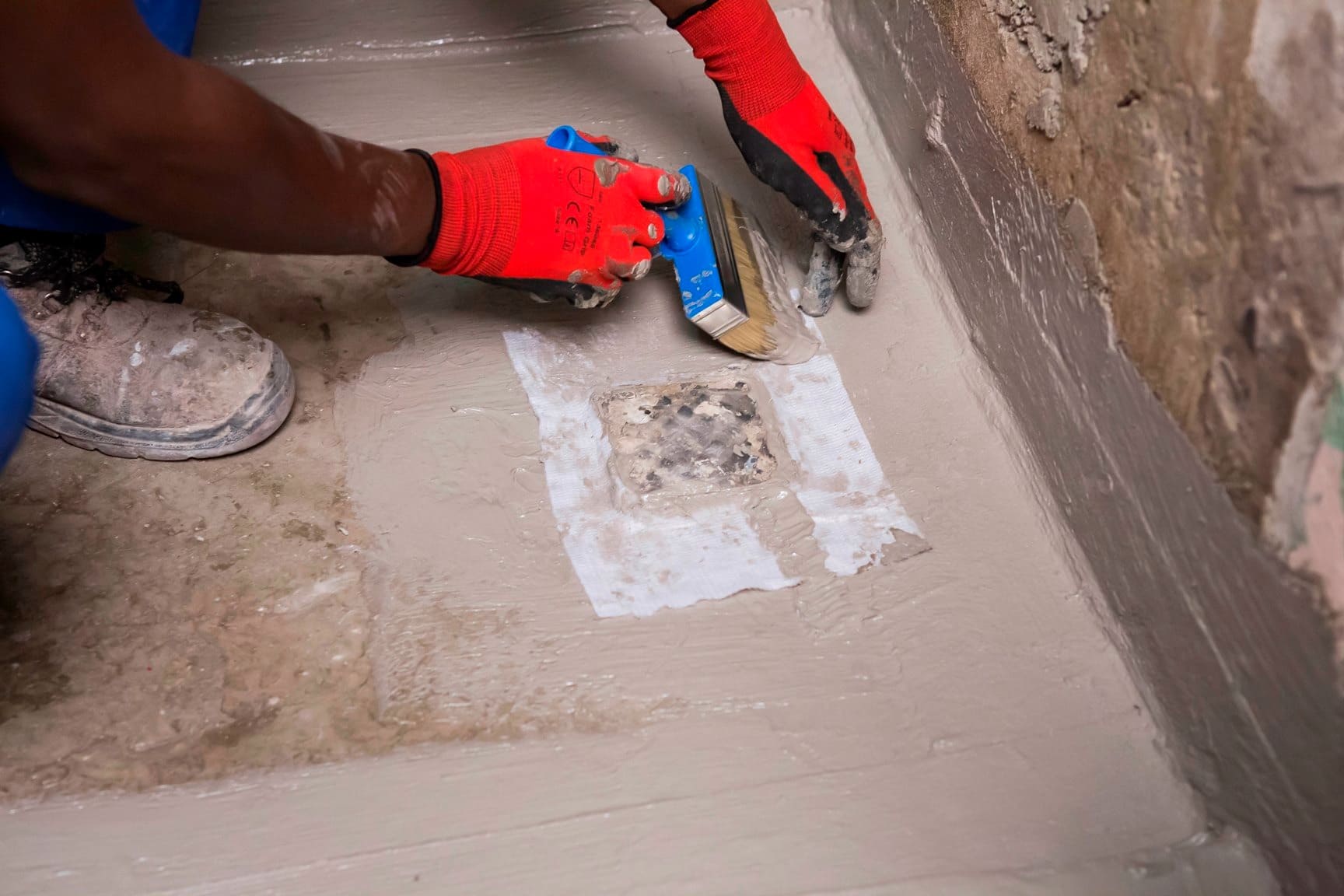
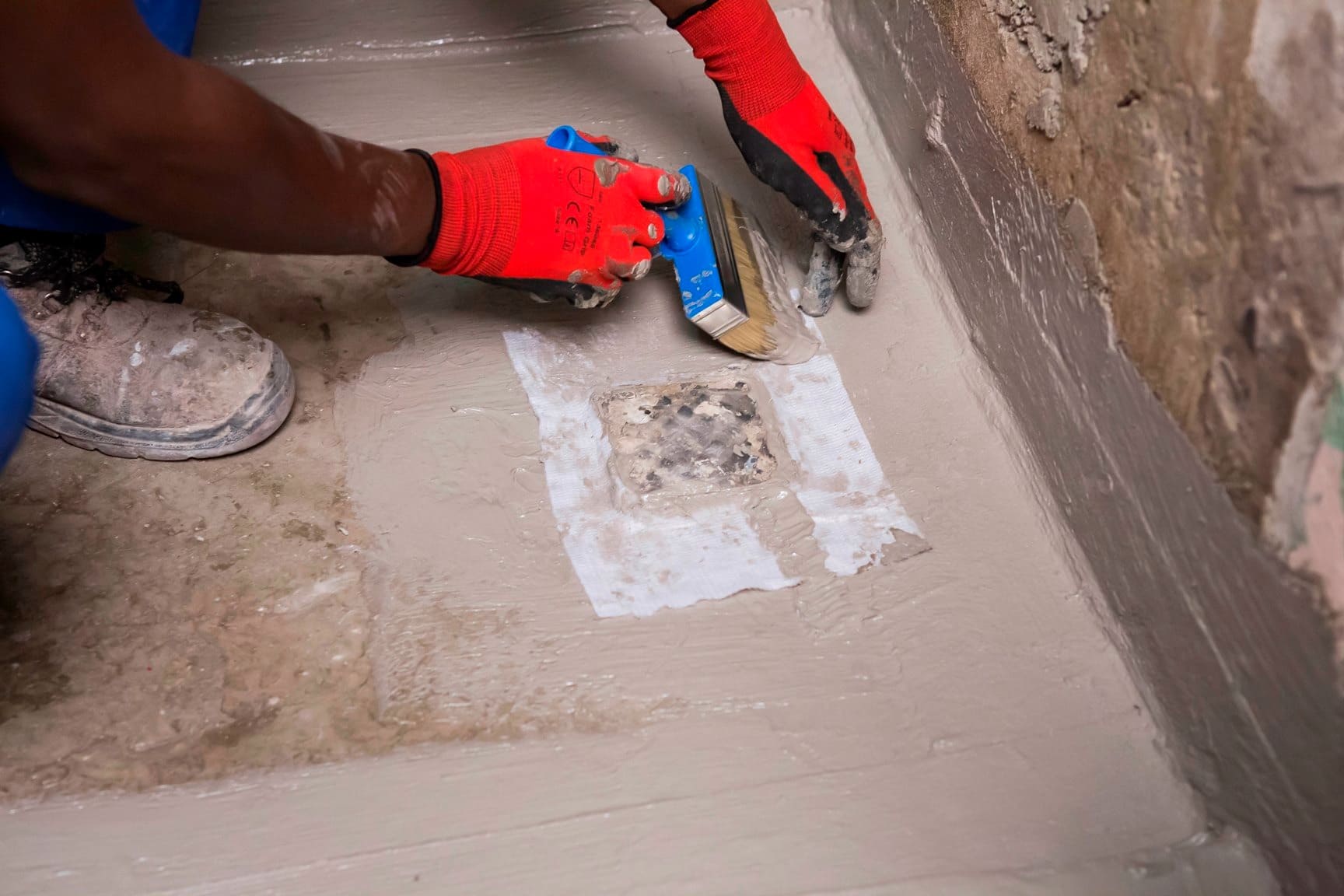
The waterproofing system needs to be applied to above the height of the shower rose and, where the wastes are flush with the floor, down into the shower waste.
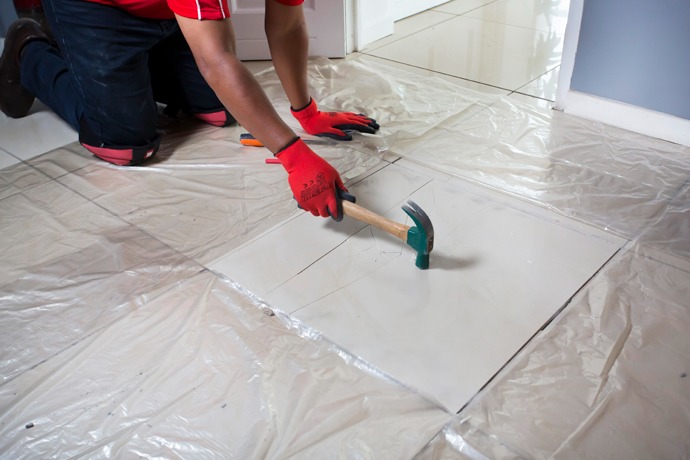
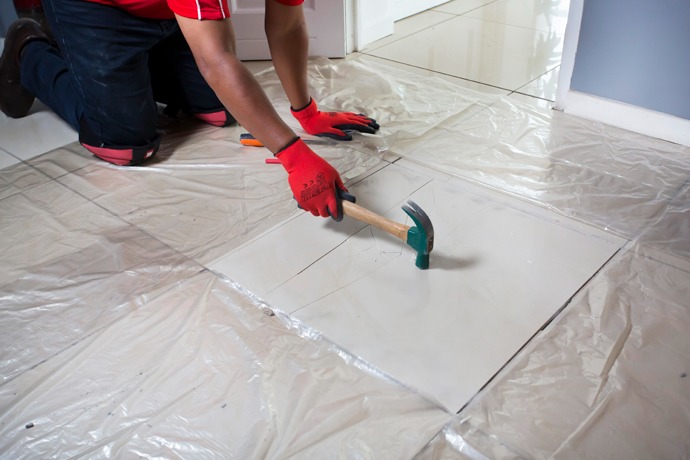
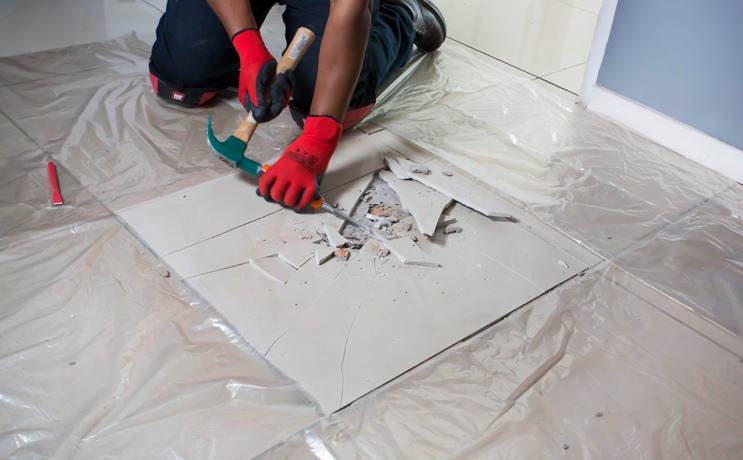
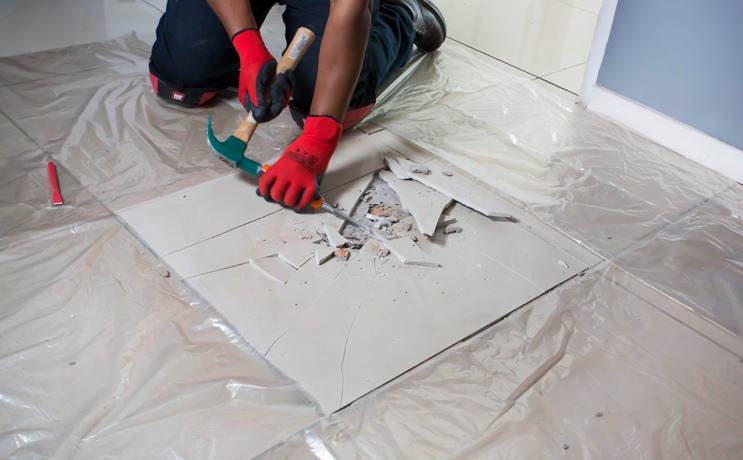
Where necessary, use a grout squeegee to apply additional adhesive to fill in any voids in the grout joints.
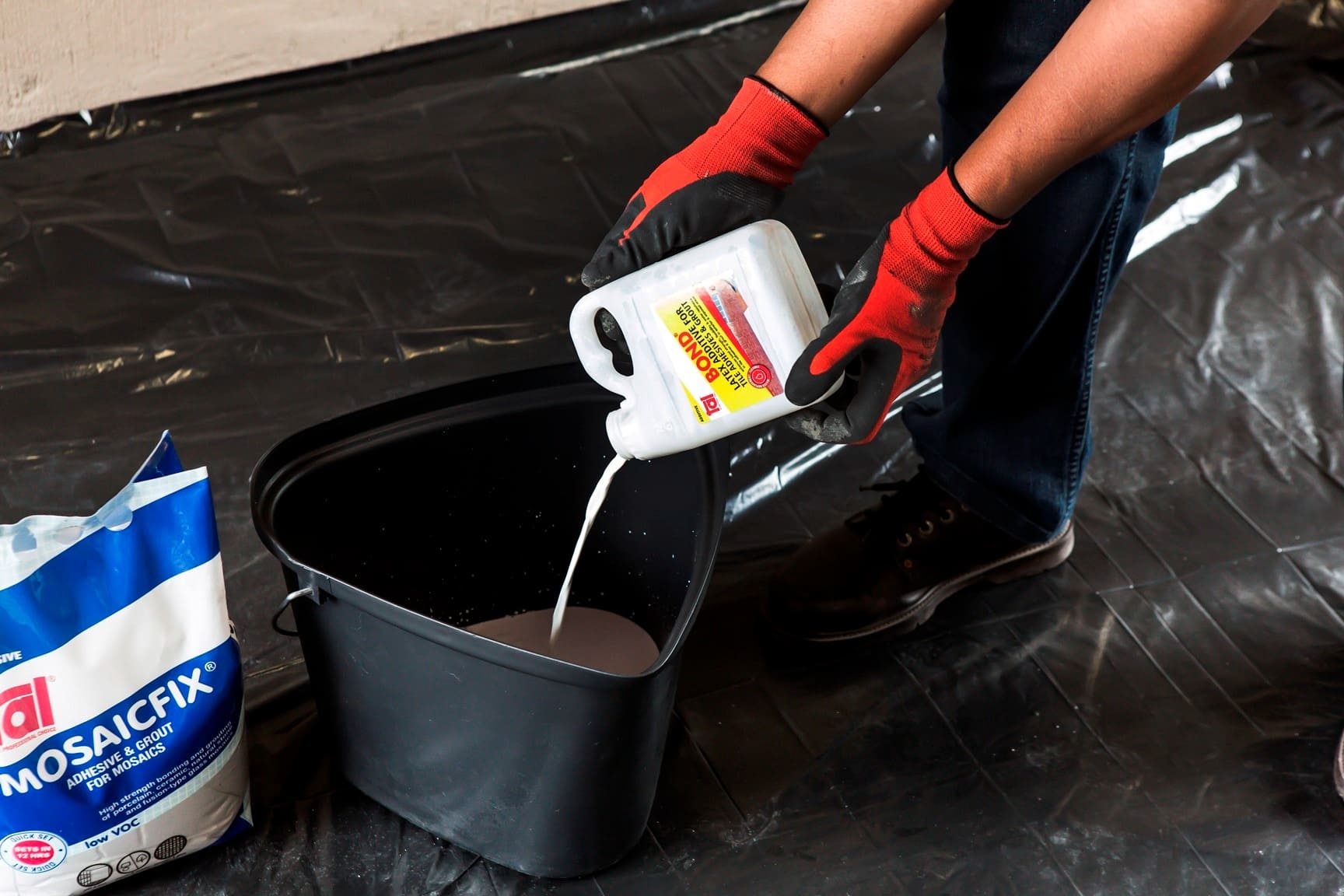
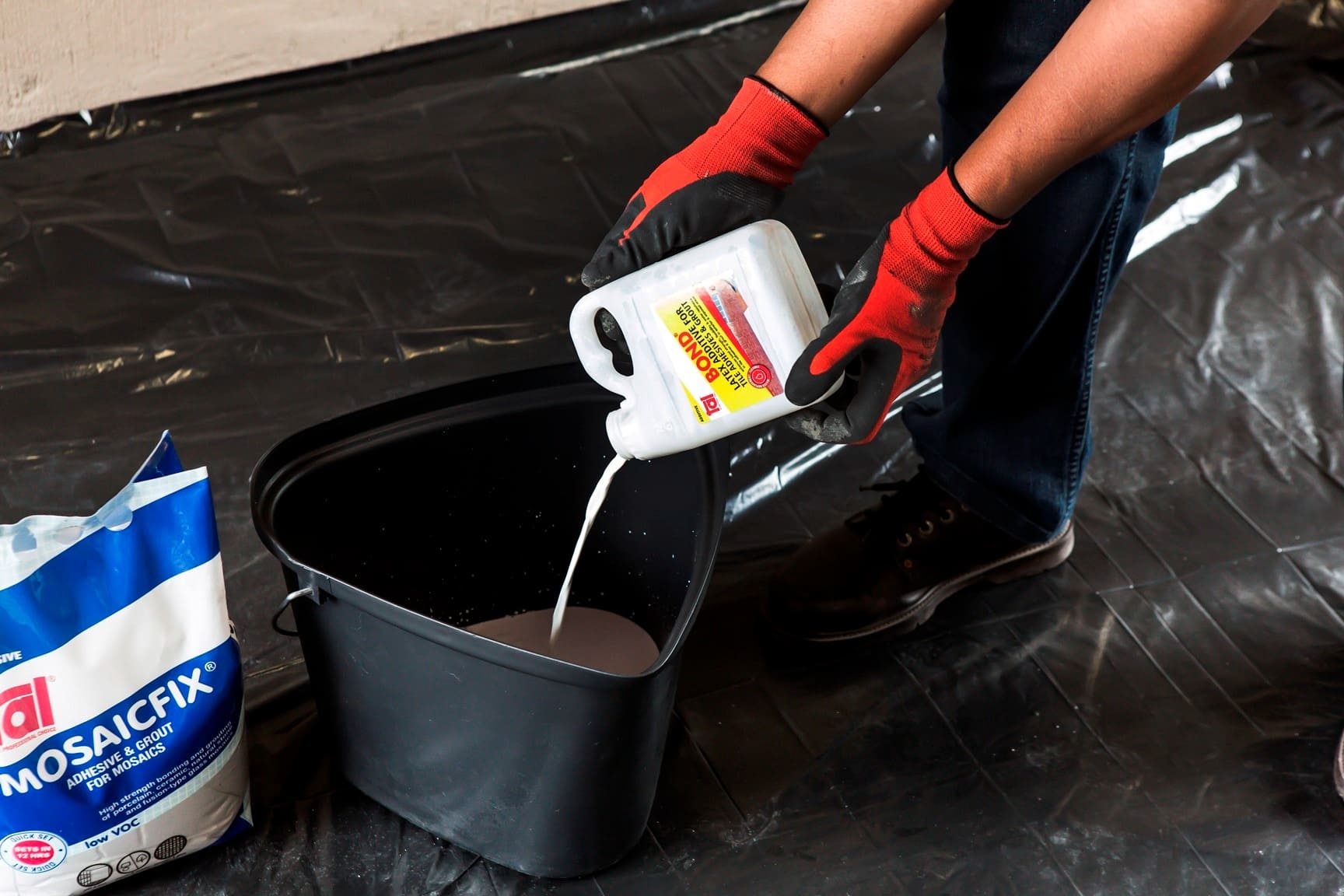
Complete the waterproofing system by replacing the water in the grout mix with TAL Bond, a latex additive, as this further increases the water resistance and flexibility of the installation.
Get the job right the first time and avoid future headaches from water seeping through and damaging the walls and floors of your home. The additional cost and effort of properly waterproofing your shower is an investment in your property and will ensure a beautiful and functional bathroom for years to come.
For more information on multi-level waterproofing systems, contact a TAL Expert on 0860 000 TAL (825), email us or watch our how-to video on YouTube for step-by-step advice on how to waterproof a shower.
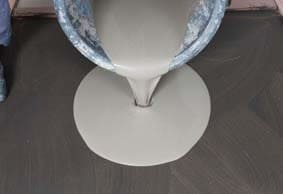
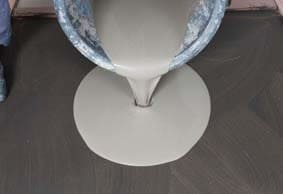
STEP 8
Roll the area using a TAL Spiked Roller to facilitate the release of any trapped air to produce a smooth surface, and to allow it to dry.
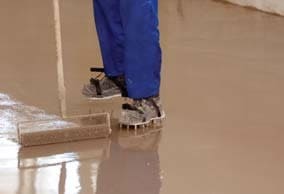
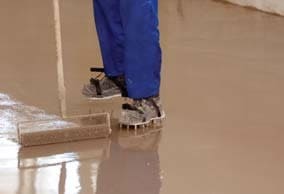
Allow the screed installation to dry for 24 hours before subjecting to foot traffic (or other trades) or installing floor coverings.


TAL MOSAICFIX is available in 20 kg and 5 kg bags from leading retail outlets.
Designed to be 100% compatible, using the TAL range of products ensures fully guaranteed multi-level tiling systems from a single source. TAL products are manufactured in South Africa to suit local climatic conditions.
If you are in any doubt, contact the TAL Technical Advisory Service on 0860 000 TAL (825), email taltech@tal.co.za. Alternatively, employ the services of an experienced and skilled mosaic tiling contractor.
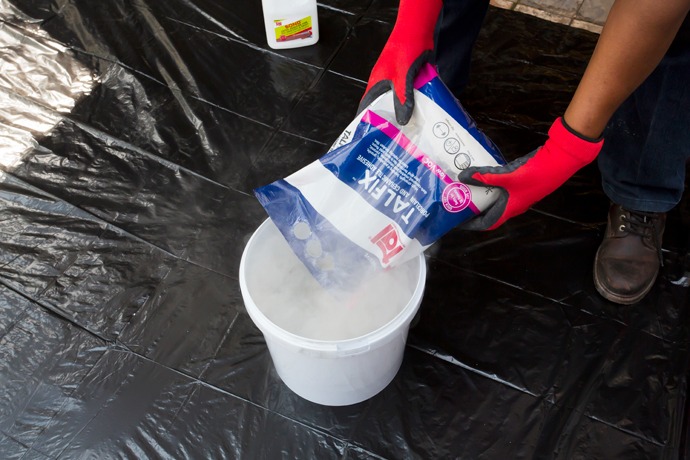
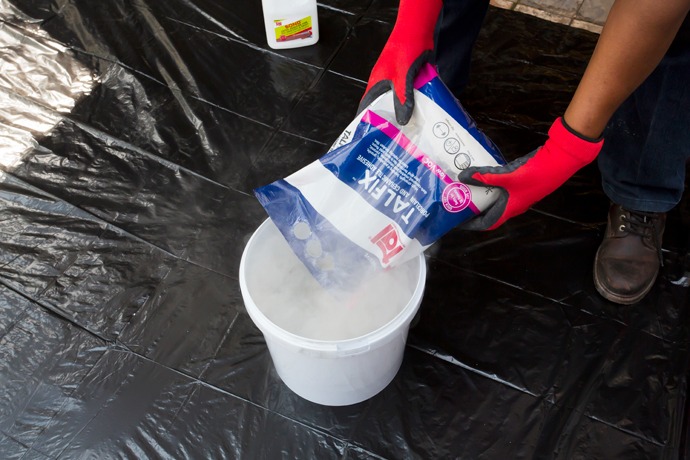
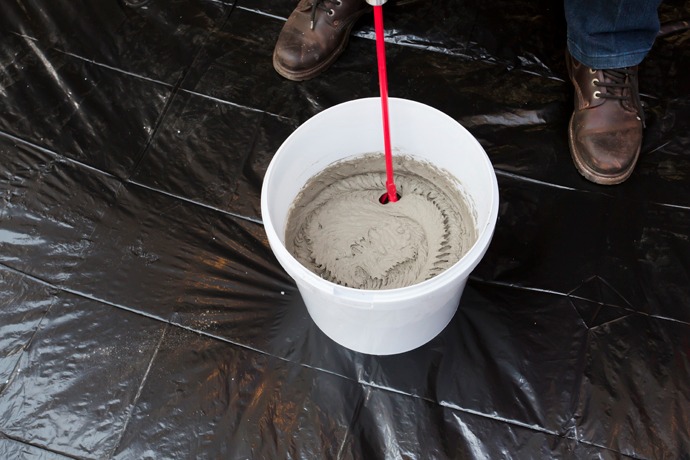
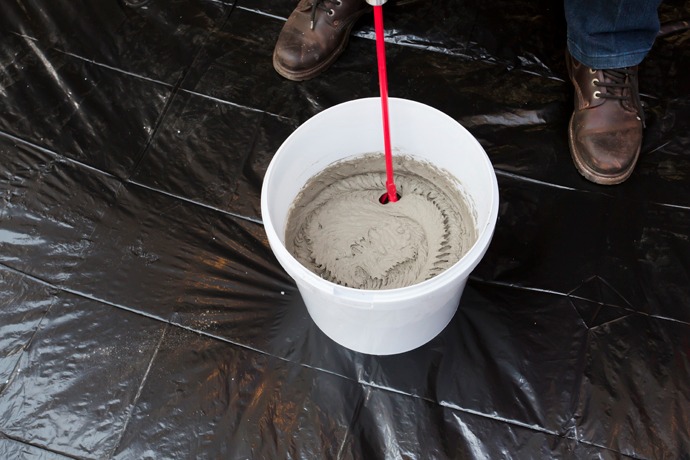
When replacing tiles, it is not always possible to apply the TALFIX directly to the floor, in which case apply the adhesive in a solid bed onto the back of the tile, ensuring complete coverage. Gently trace the notched side of a floor trowel through the adhesive to create ‘ridges’.
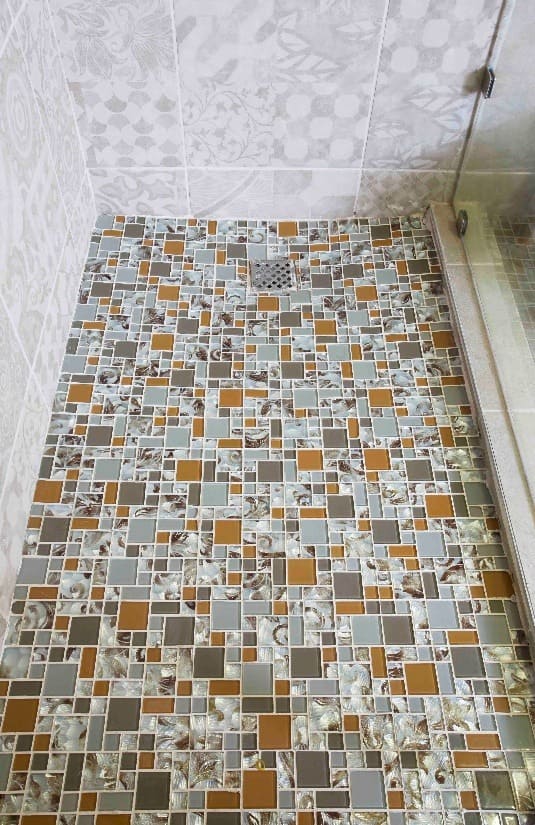
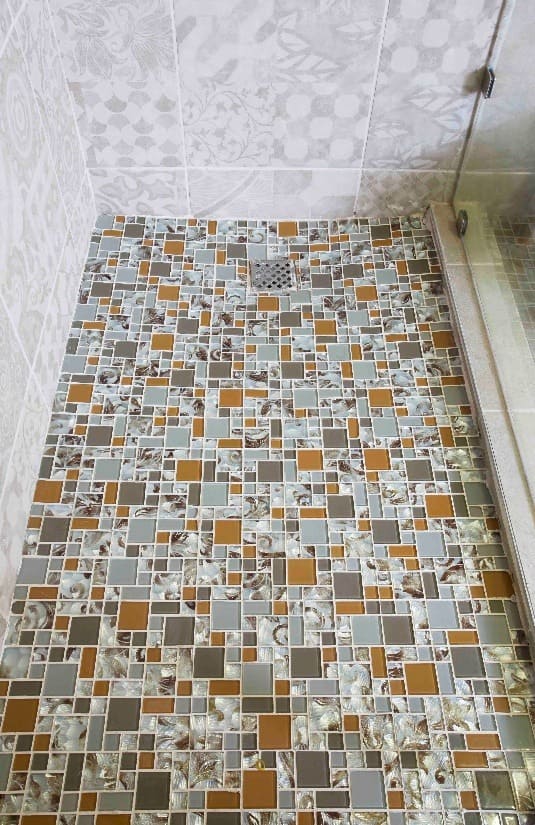
Adhesive system
When tiling onto existing tiles, it is important to only use a quick- or rapid-setting adhesive, as the existing tiles will present a dense, impervious surface, and standard-setting adhesives will take longer to dry. Too early trafficking of newly-installed tiles before the adhesive has set sufficiently can result in hollow-sounding or loose tiles.
Use TAL Tile-To-Tile quick-setting adhesive for tiling onto interior surface beds. When tiling onto suspended slabs and for external installations mix the TAL Tile-To-Tile with TAL Bond, replacing the water in the mix. Alternatively, TAL Bond Powder can be added to the adhesive mixing water.
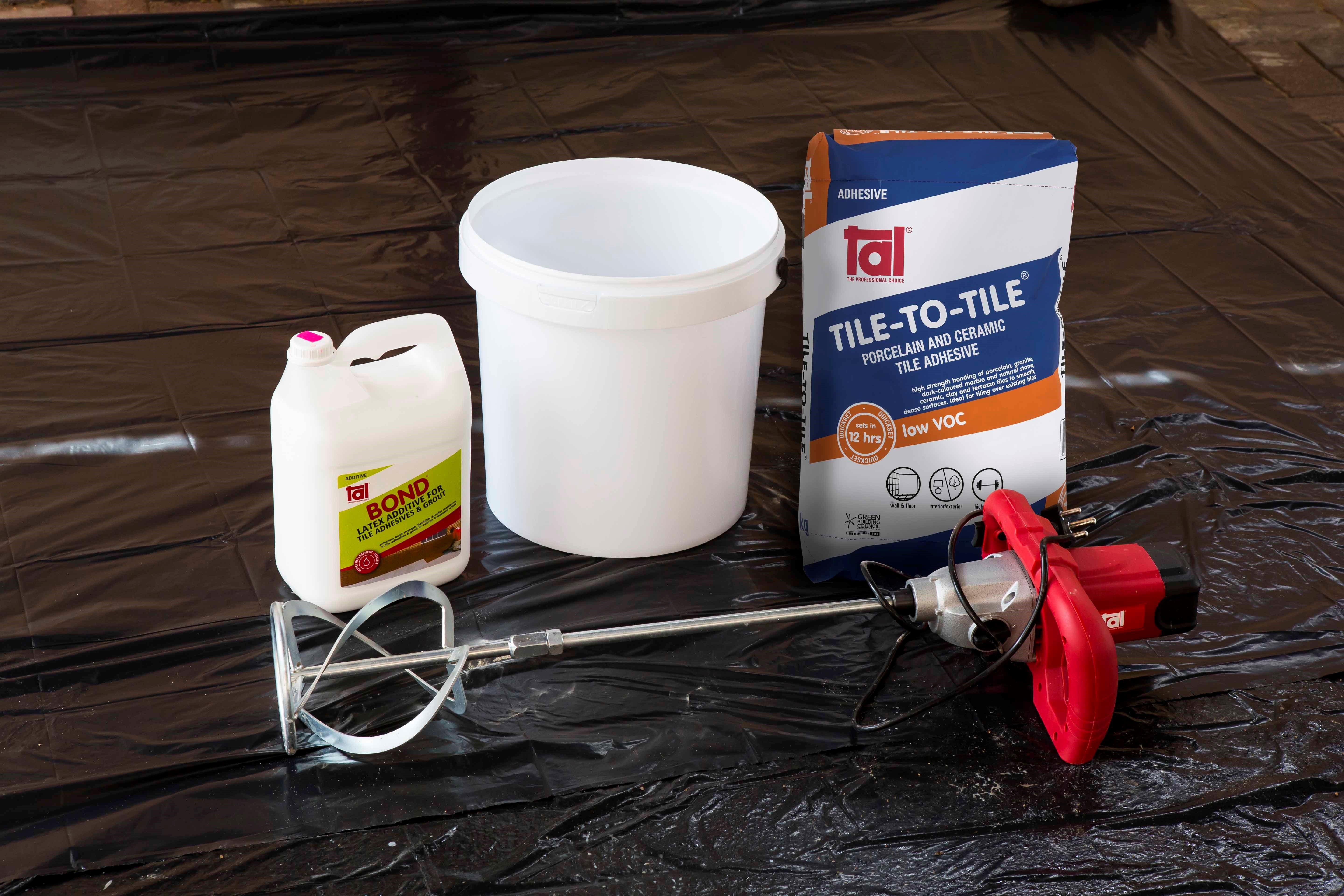
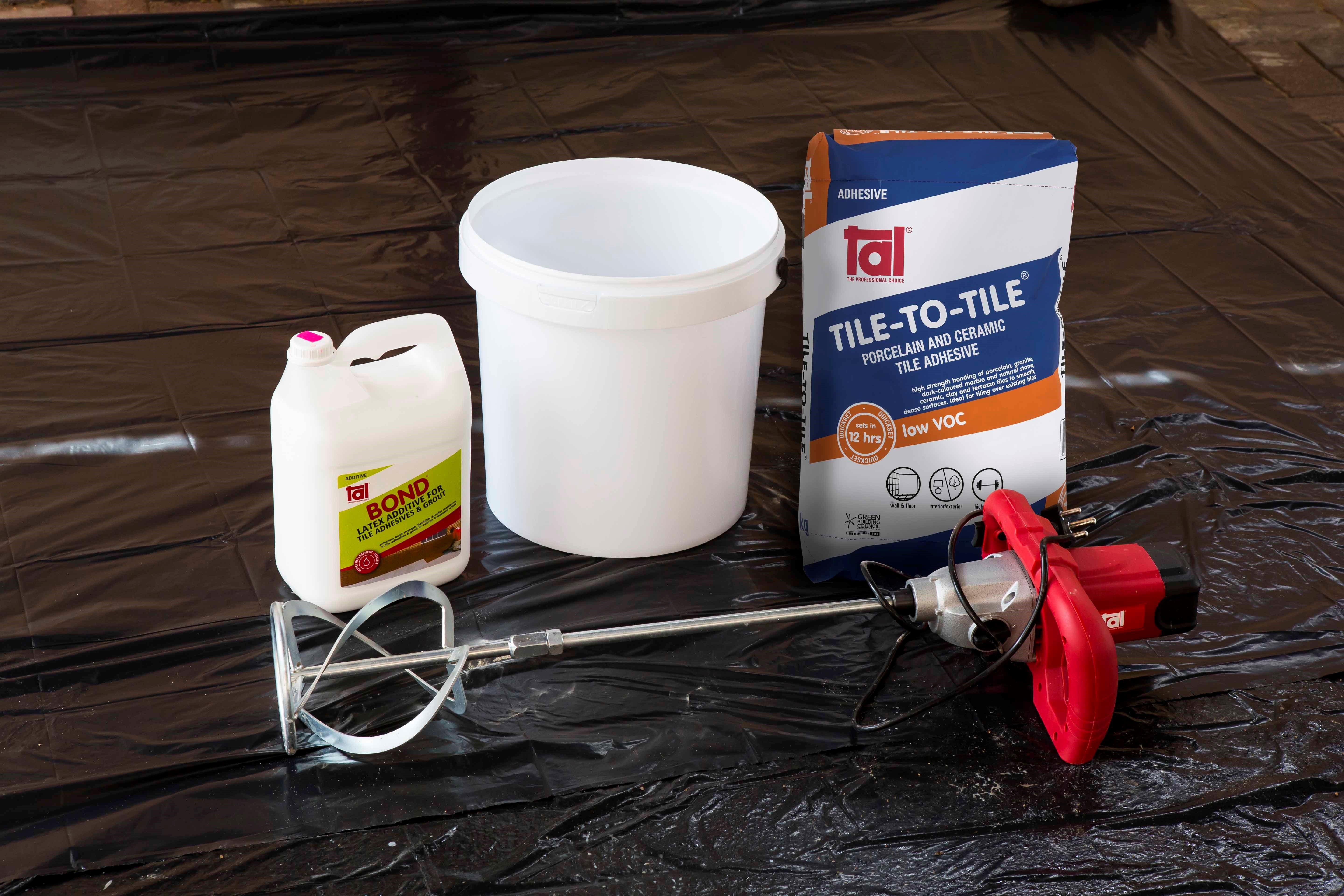
Ensure that there is a solid bed of adhesive at least 6 mm thick beneath each tile.
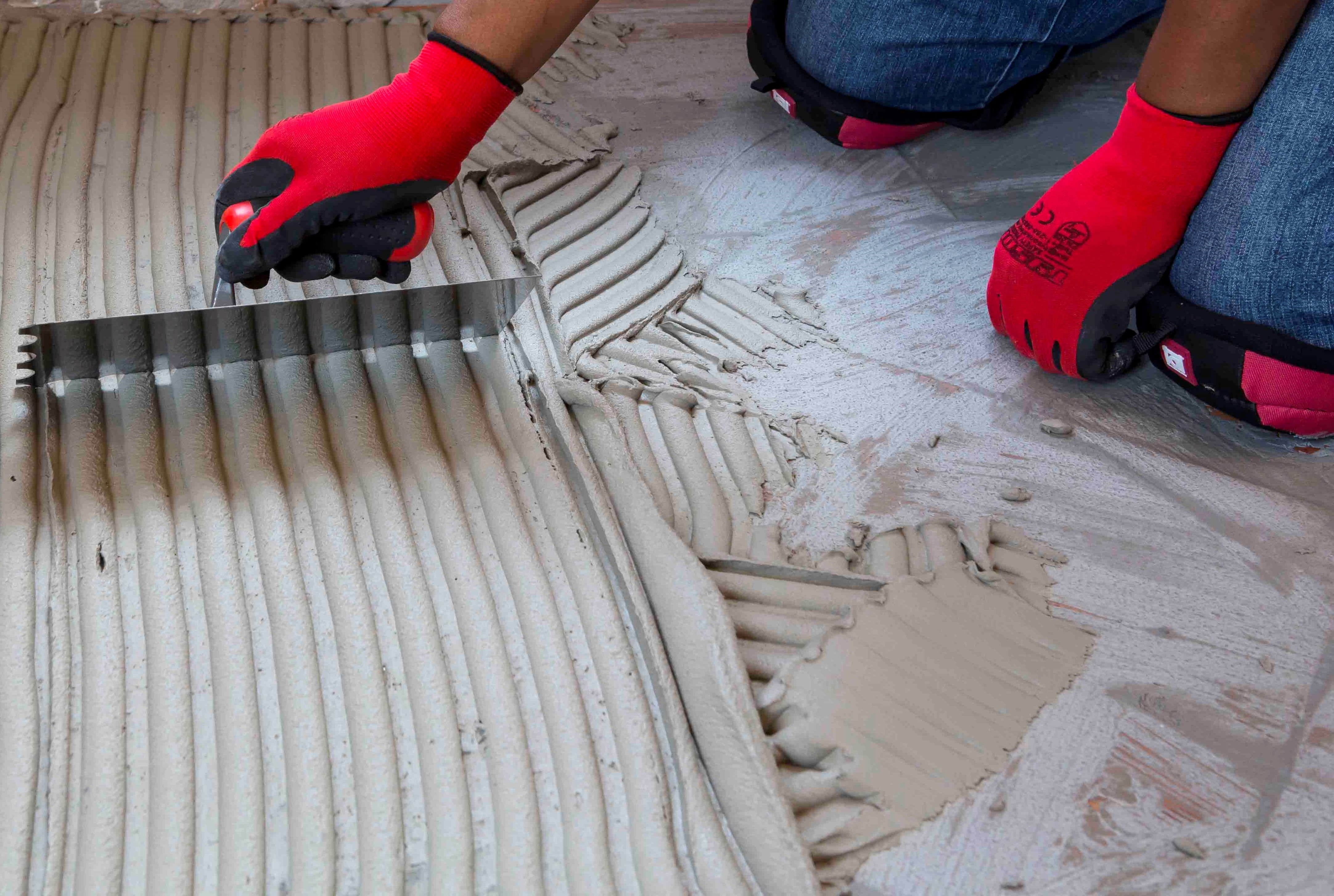
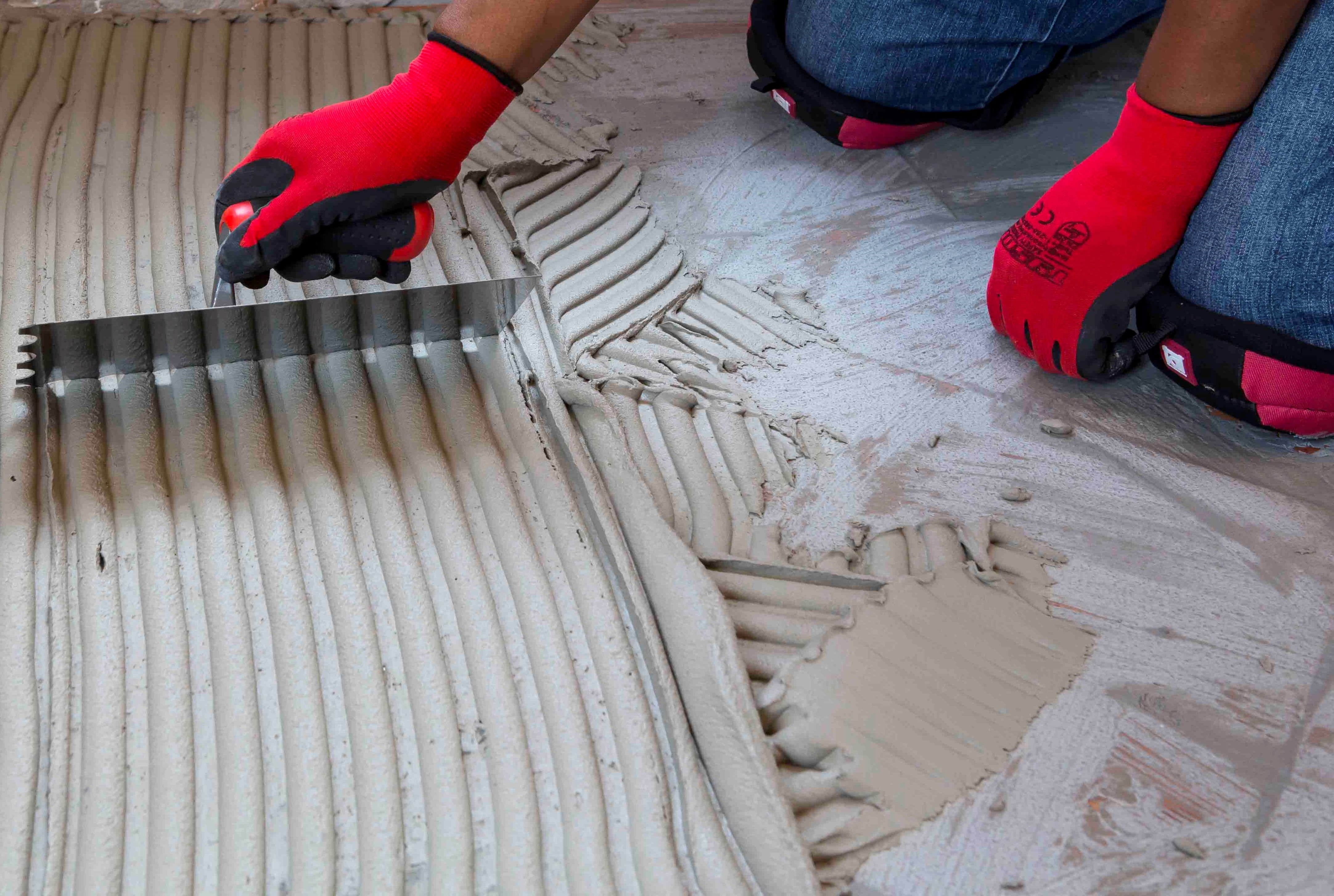
Back buttering with a thin coat of adhesive may also be required when using large-format tiles to ensure full contact with the adhesive bed.
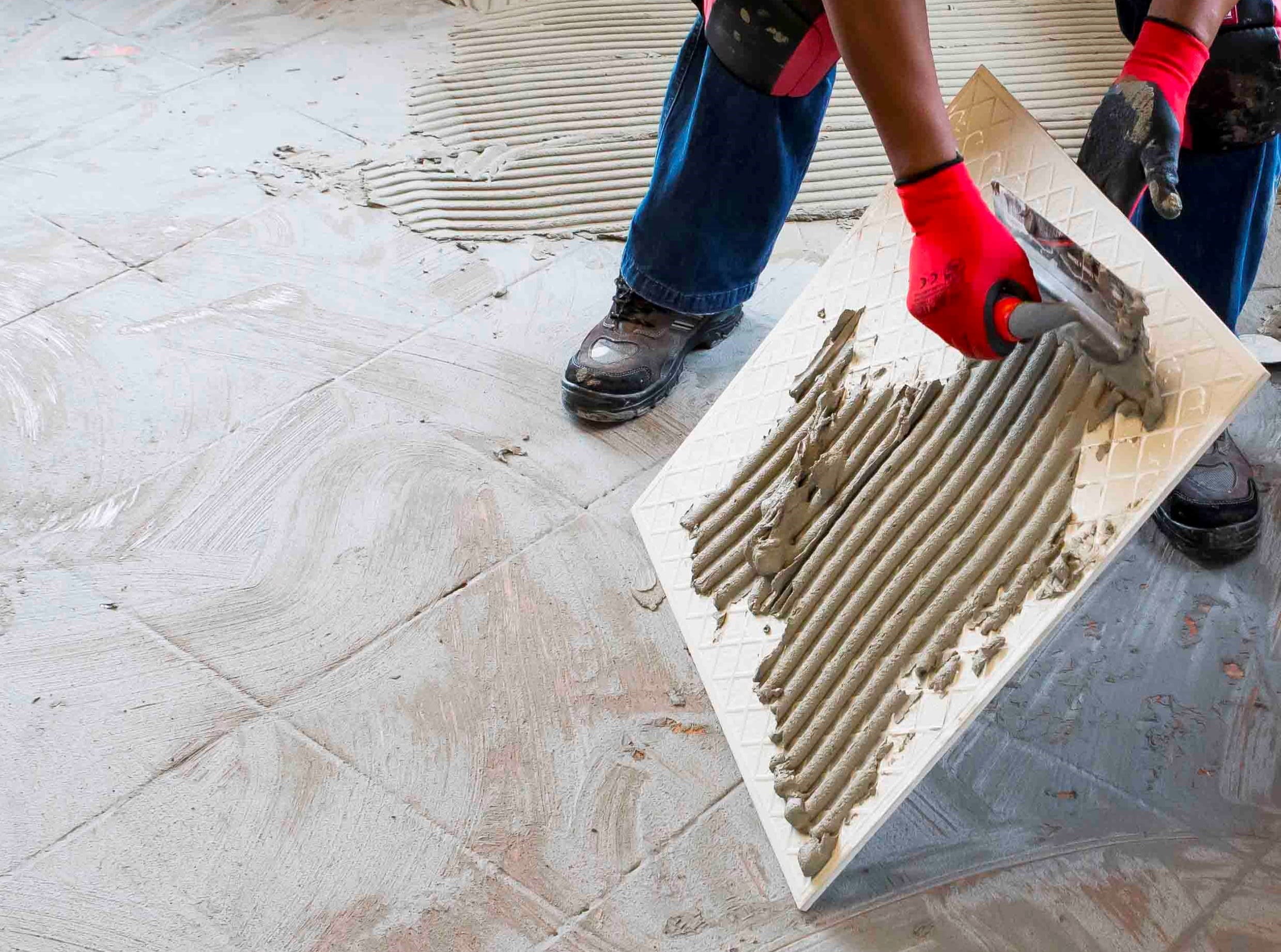
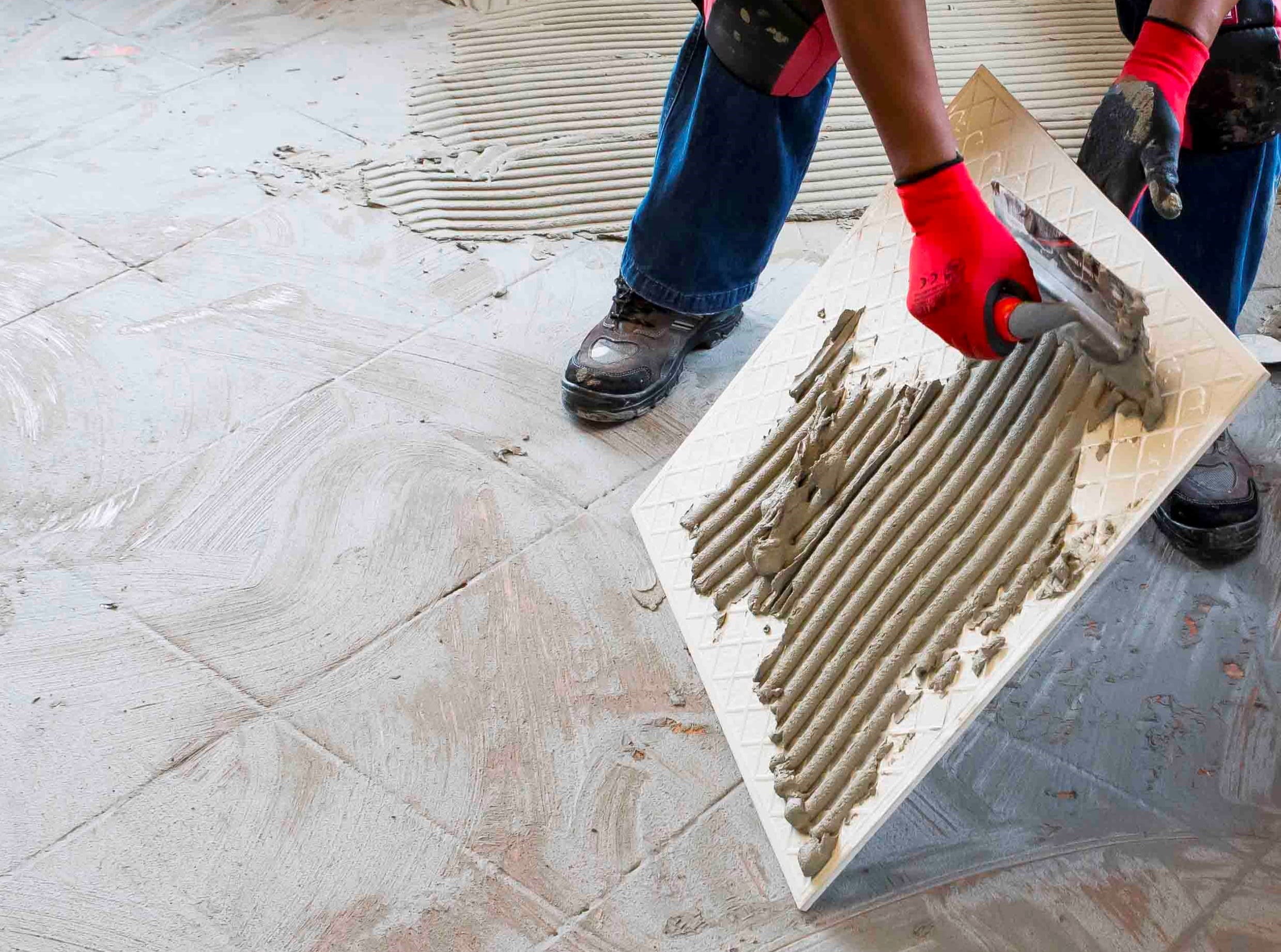
Grouting
Grouting should not be carried out until the adhesive has set sufficiently to prevent the tile installation from being disturbed during the grouting operation (always refer to the adhesive packaging for setting times). When using TAL TAL Tile-To-Tile, allow a minimum of six hours before grouting.
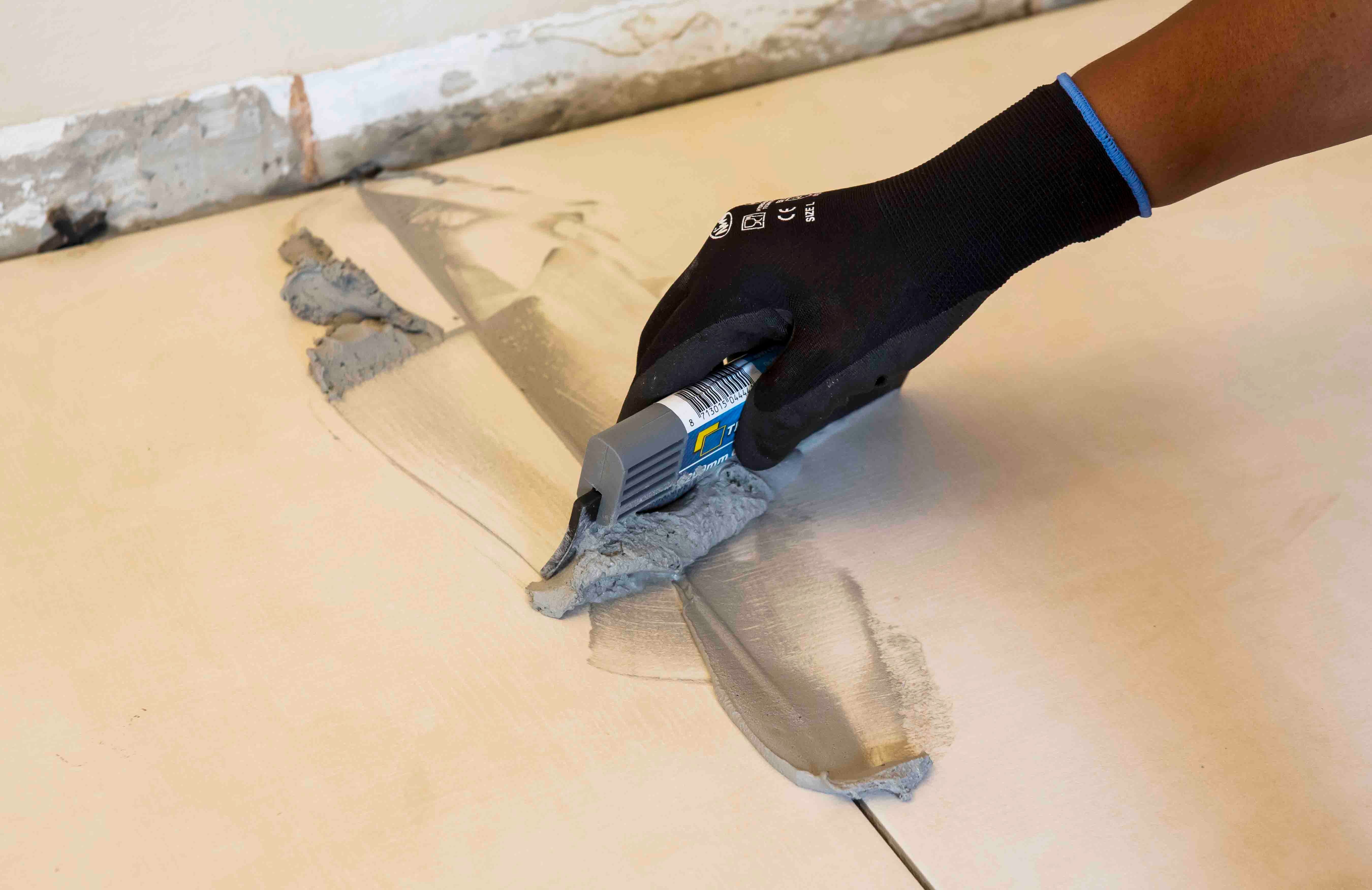
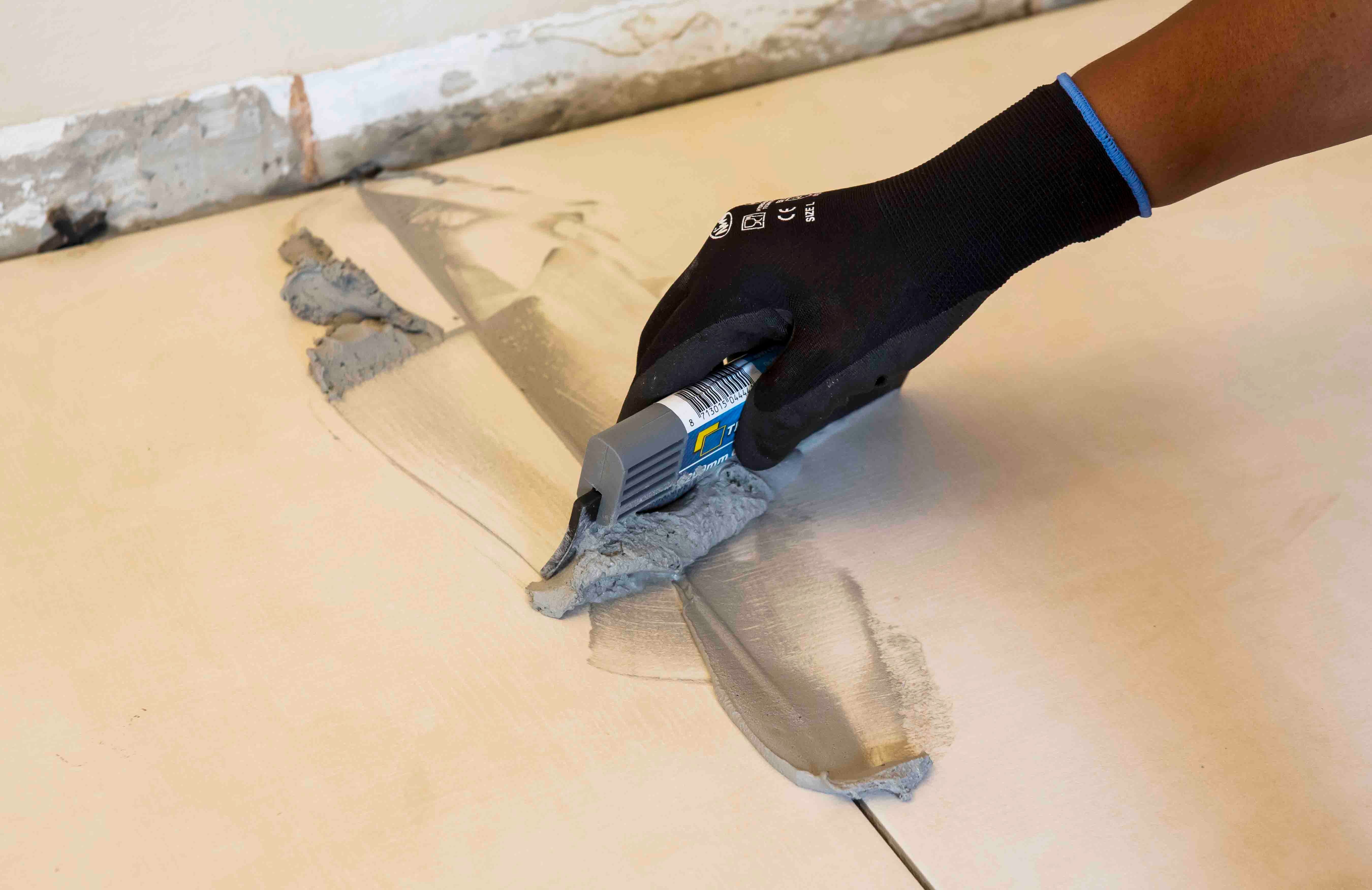
For interior surface beds, use TAL Wall & Floor Grout for filling tile joints up to 8 mm wide. TAL Quarry Grout can be used in wider joints up to 25 mm wide. On suspended slabs and for external installations, replace the water in the grout mix with TAL Bond, or add TAL Bond Powder to the grout mixing water.
Particular care must be taken to clean the grout off the tile face before it hardens completely. This is especially important when an additive such as TAL Bond or TAL Bond Powder has been used. A tile sample should be tested beforehand to ensure that no grout is absorbed through the glaze or into the tile body, thereby staining the tiles permanently.
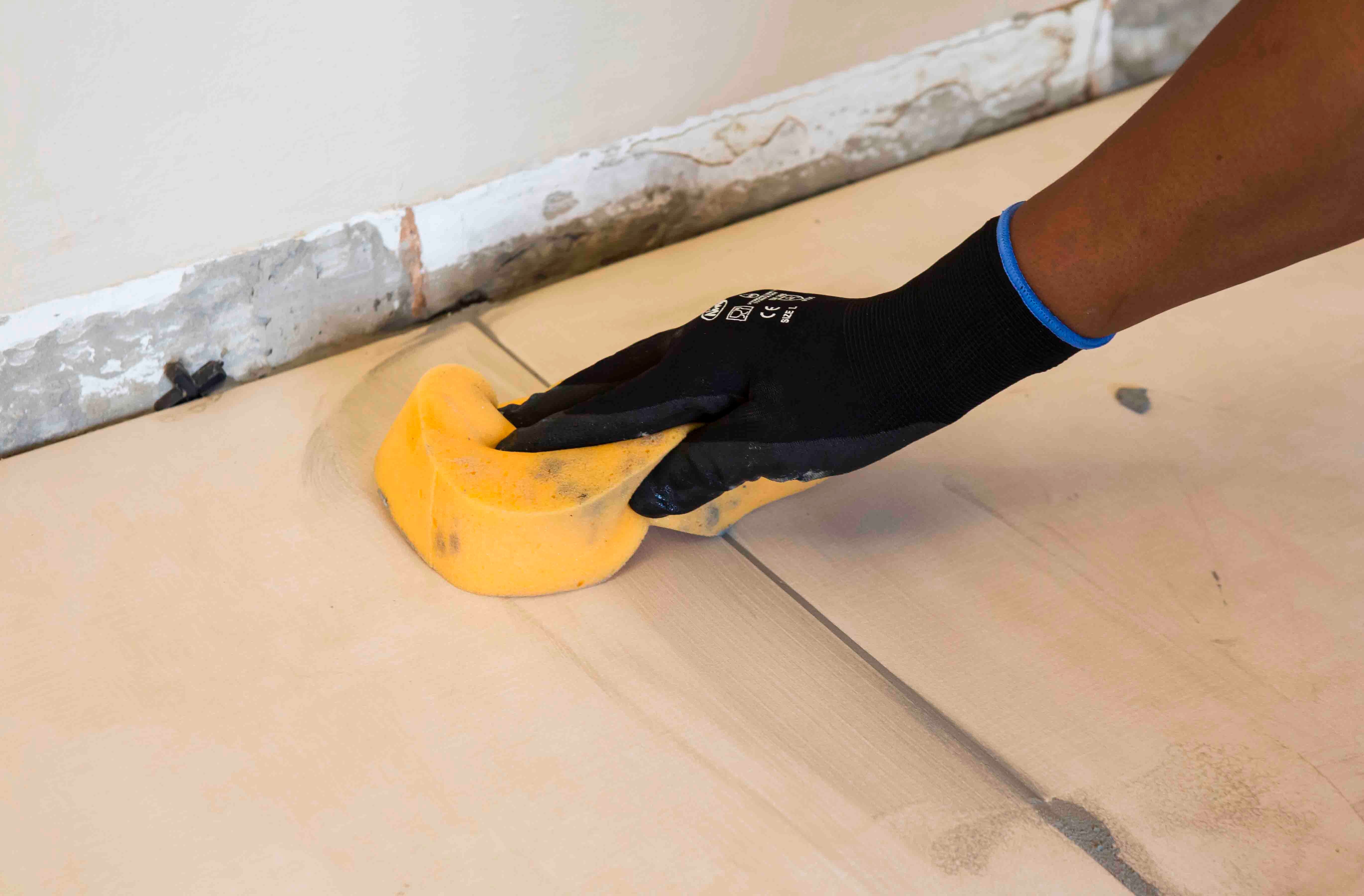
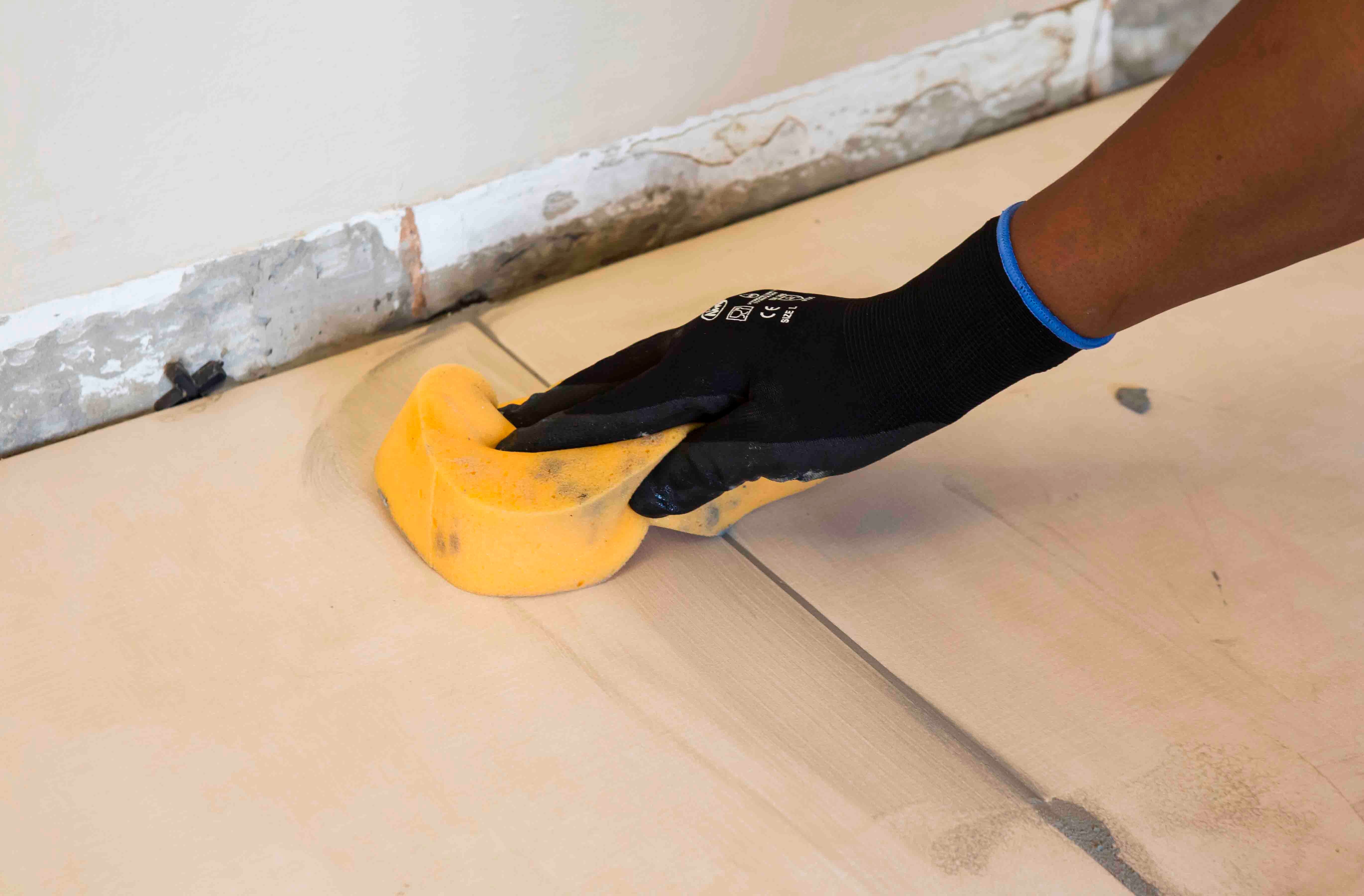
Movement joints
The lack of movement joints in tile installations is a major cause of tile failure. When tiling over existing tiles, the existing structural and movement joints must be maintained in the new tile installation. The movement joints should be at least 5 mm wide and extend through the adhesive and both tile layers.
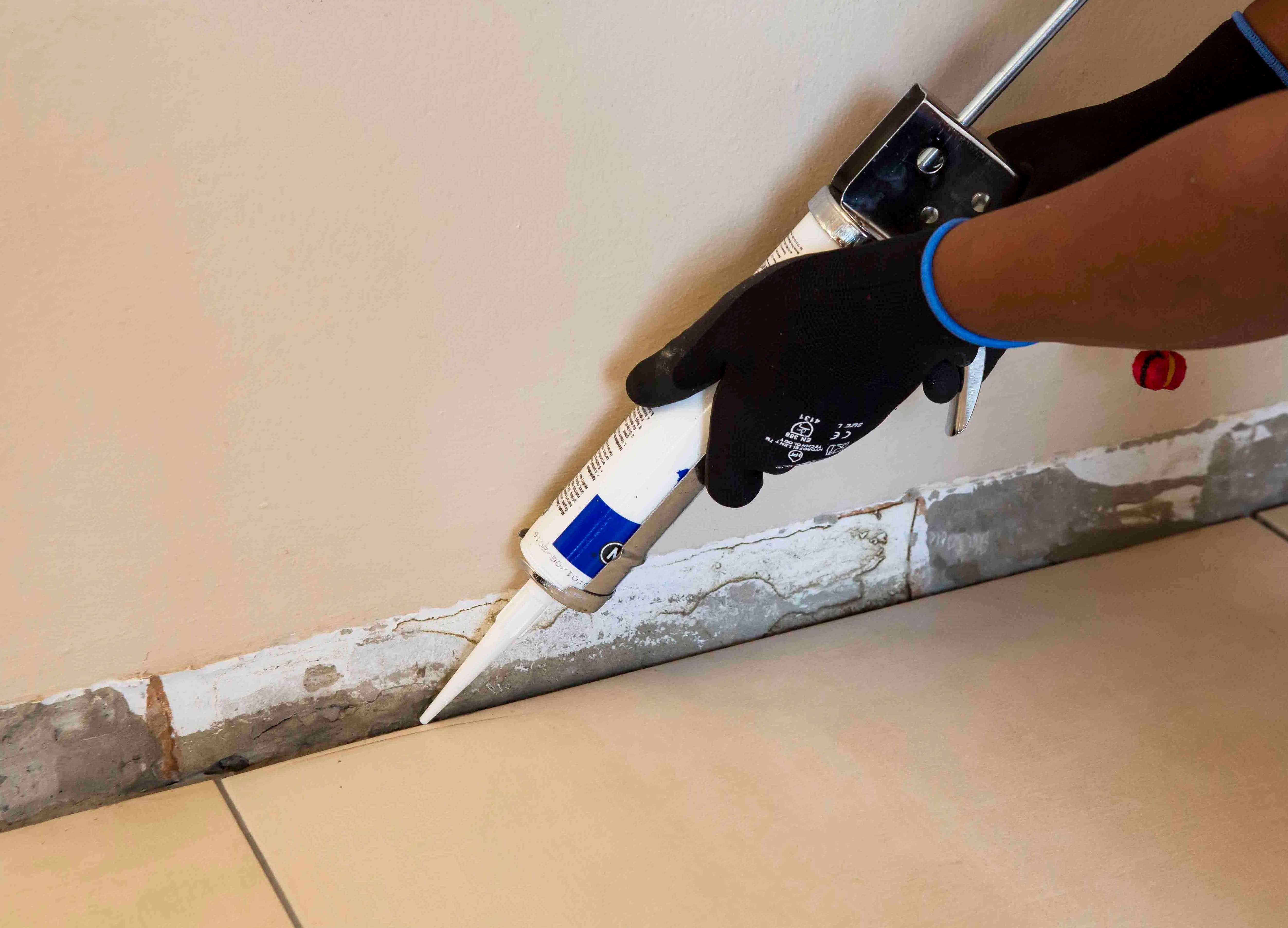
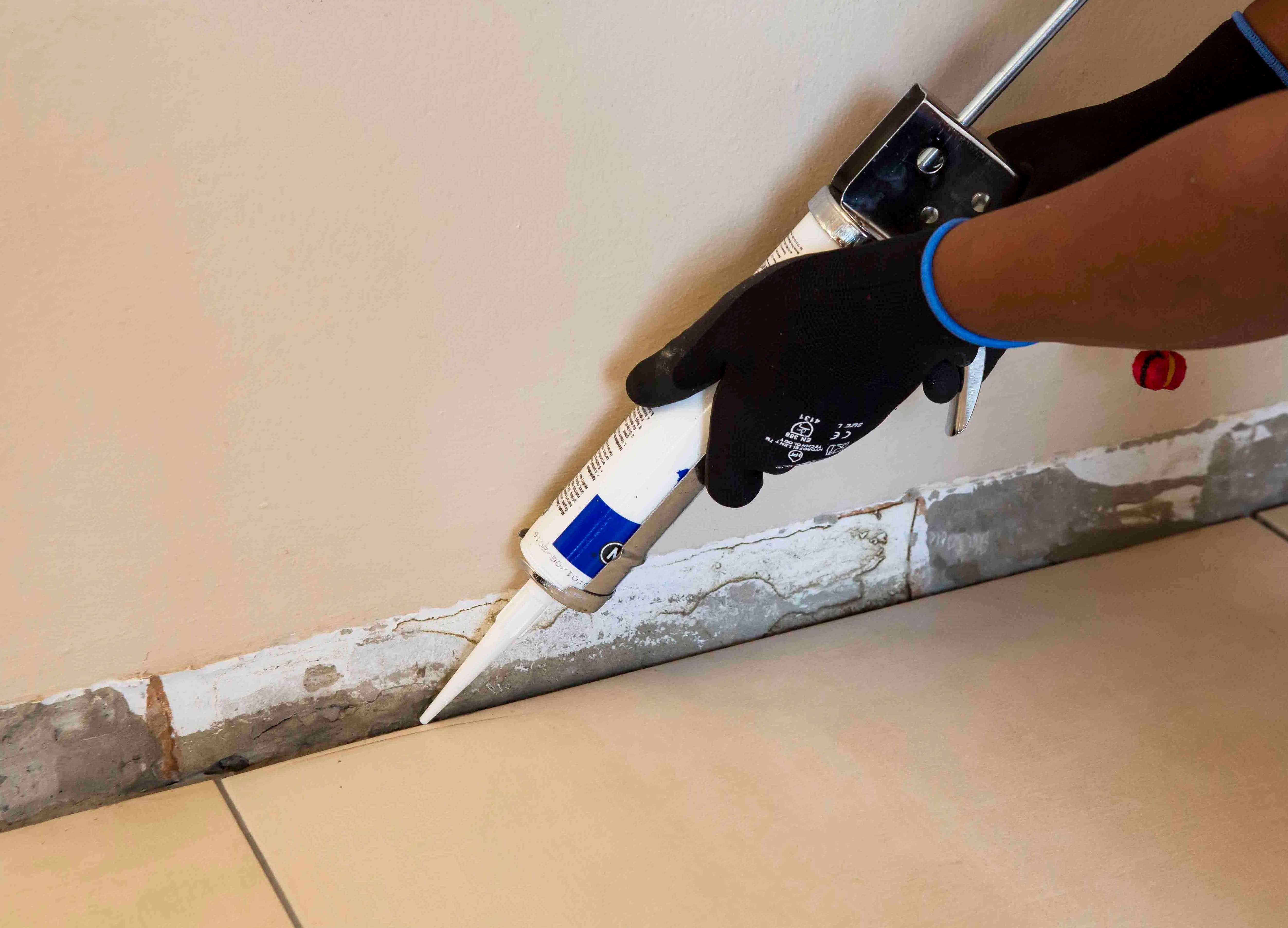