Putting our money where our mouth is
In a professional work environment, protecting floors from everyday damage is of extreme importance as damaged floors can cause health and safety issues. Hazards such as abrasions, thermal shock, and chemical wear, can damage floors in a working environment, leading to compromised health and safety. It is for this reason that we selected TAL UraFloor HT as the floor covering when we renovated our technical workshop at our factory in Clayville, east of Johannesburg. The process took three days from surface preparation to laying down of the final product.
1. Laying down an epoxy primer
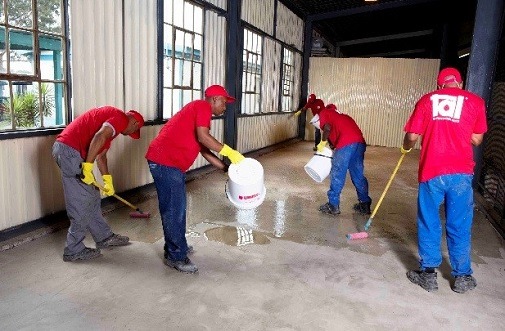
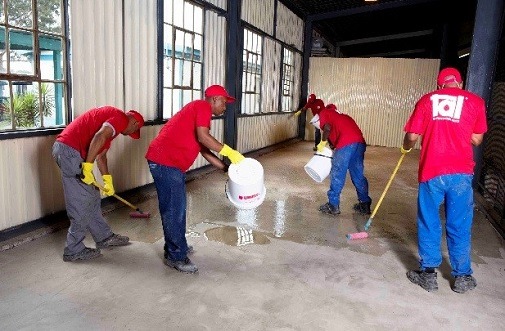
2: Broadcasting a coarse grit to ensure grip
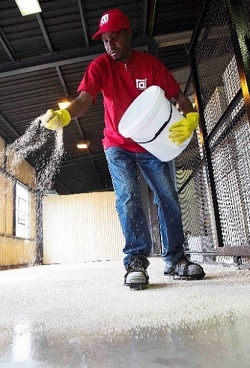
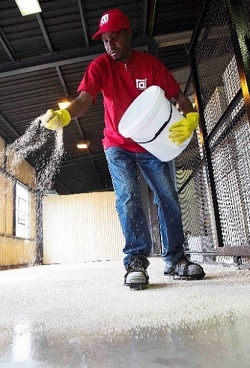
3: Applying the final product
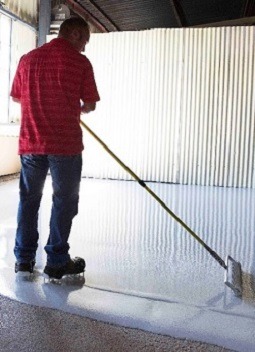
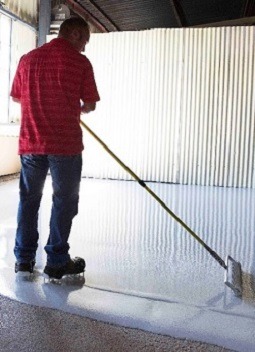
4: Drying time is between 3 - 5 days depending on the foot traffic of the area
In this video you can view the entire process from start to finish:
https://www.youtube.com/watch?v=zjYHSuXykqA
Our Construction Products team points out that the TAL UraFloor range is not a DIY solution but rather, one that needs prior training or the assistance of a trained professional.
TAL’s UraFloor range of polyurethane floors forms part of the X-Calibur X-Tech range, which also consists of epoxy and cement screed floors which are overlayments. This range of flooring protection products offer a proactive solution to ensure the longevity of floors.
The TAL UraFloor range comes in four different types:
TALUraFloor HT: A heavy-duty solvent-free polyurethane flooring system which is available in both screed and self-levelling forms. Its excellent resistance to organic and inorganic acids, alkalis, fuel and hydraulic oils, aromatic and aliphatic solvents makes it perfect for heavy-duty applications in areas where chemical and food processing, brewing, engineering process areas, joint nosing and bedding applications take place.
TALUraFloor CS: A heavy-duty polyurethane-based floor screed and mortar designed to provide excellent resistance to abrasion, chemical attack and thermal shock. The product has been developed especially for use in cold stores and freezer rooms.
TAL UraSeal WDS: A high-performance water dispersed polyurethane sealer and anti-scratch coat that can be applied to existing epoxy and polyurethane coatings and floors, as well as to underlays, concrete screeds and slabs.
TAL UraFloor TF: Providing excellent resistance to abrasion, chemical attack and thermal shock is TAL UraFloor TF, a heavy-duty polyurethane-based floor screed and mortar which is resistant to abrasion, impact and chemical attack, and also contains a unique antimicrobial additive.
This makes it a product-of-choice for heavy-duty applications in food processing, medical facilities, dairies, beverage factories, cold stores and anywhere else that requires a non-slip finish. If applied at a thickness of 9 mm, TAL UraFloor TF can also be steam cleaned for maximum hygiene.
TAL UraFloor Range is the perfect industrial companion that ensures a ‘prevention rather than cure’ solution to the longevity of floors. Again, it is emphasised that these products are for industrial use and are potentially hazardous if not used correctly by trained operatives. Customers are encouraged to discuss their requirements with us as well as get technical information on which product is the best fit for their purpose.
Interested in these products? Contact any of TAL’s Building Products Reps as outlined below or download the data sheet or contact our TAL Technical Advice Line on 0860 000 TAL (825).
Building Product Reps:
Dylan - 082 652 7824 (Kwa-Zulu Natal)
Matthew - 083 661 7154 (Western Cape)
Schalk – 082 875 0384 (Gauteng)
Tendai – 082 895 1055 (Gauteng)
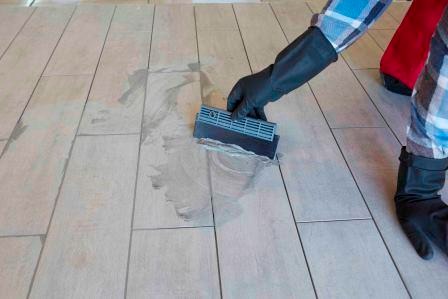
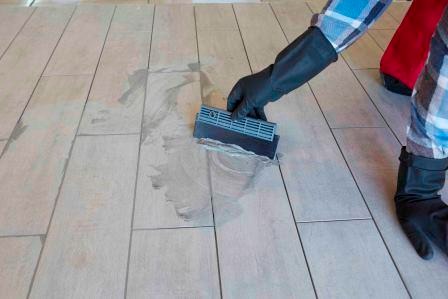
Also ensure that the spacer size you use is correct for the type of tile you have selected; the joint width between glazed ceramic floor tiles should be a minimum of 5mm wide, and a minimum of 3mm wide between porcelain tiles, including rectified porcelain tiles. To achieve the natural look, opt for grout colour that is darker than the tile itself. Click here to find out more about how to select the perfect grout colour.
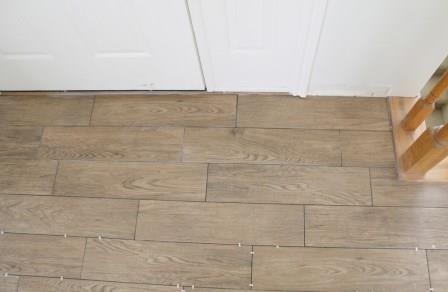
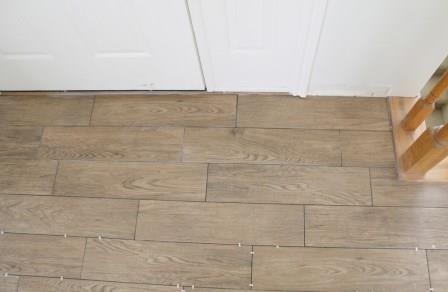
MOVEMENT JOINTS
Allowance for movement (building, thermal and moisture) must be made in all tile installations. Perimeter joints must be installed around the perimeter of all floors and around any fixtures protruding through the tile installation, such as walls, columns and stairs. Intermediate tile panel movement joints should also be installed at maximum 5 metre centres in both directions for interior surface bed applications, and maximum 3 metre centres for suspended slabs and exterior applications. These joints must be a minimum of 5mm wide, must extend through the tile and tile adhesive layers to the substrate, and must be filled with a good quality resilient joint sealant and suitable backing cord.
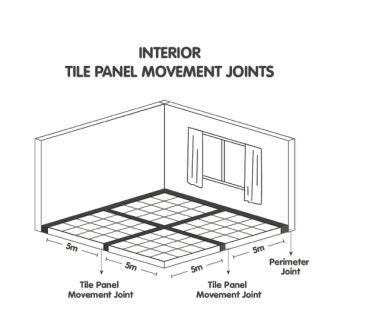
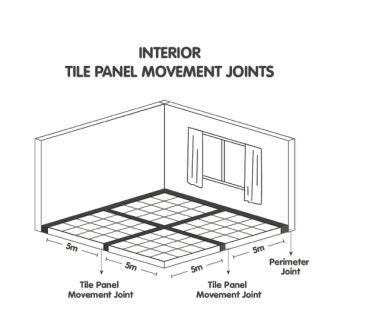
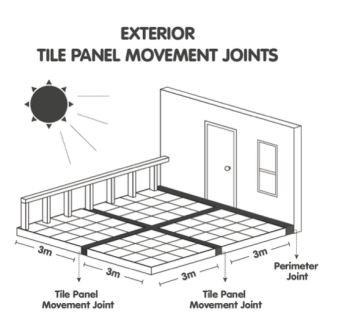
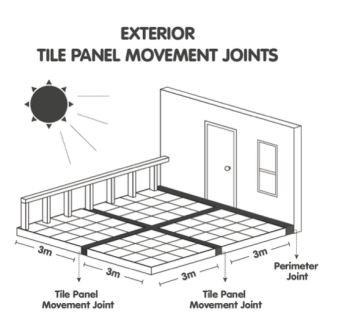
When using large format tiles (a tile with the length of at least one edge equal to/greater than 600mm, or a facial area greater than 3500cm²) there will be a smaller number of grout joints, compared with the same area of normal format tiling. As a result, less stress (movement) can be accommodated at tile joints.
Considering a wood-look tile installation? Give us a call or send usan email and we’ll give the right advice, no matter how big or small your tile installation: 0860000 TAL (825) or [email protected]. If this TAL Talk blog post interested you, you may want to take a look at this TAL Talk blog post: The 101 on wood-look tiles.
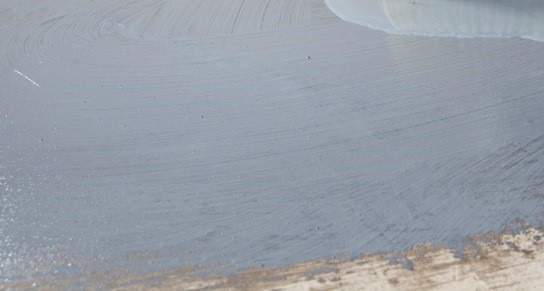
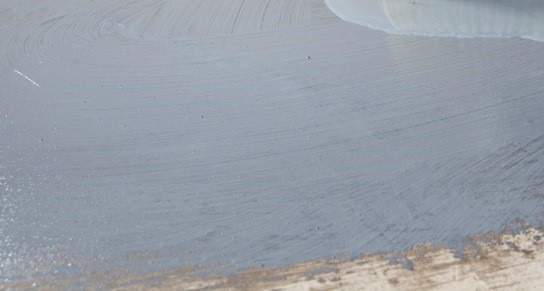
Complete the waterproofing system by replacing the water in the grout mix with TAL Bond, a latex additive, as this further increases the water resistance and flexibility of the installation.
Get the job right the first time and avoid future headaches from water seeping through and damaging the walls and floors of your home. The additional cost and effort of properly waterproofing your shower is an investment in your property and will ensure a beautiful and functional bathroom for years to come.
For more information on multi-level waterproofing systems, contact a TAL Expert on 0860 000 TAL (825), email us or watch our how-to video on YouTube for step-by-step advice on how to waterproof a shower.
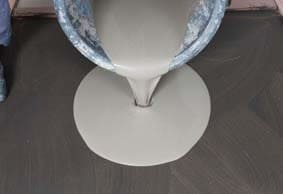
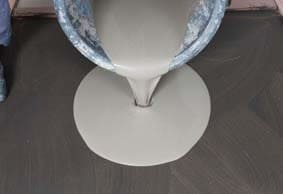
STEP 8
Roll the area using a TAL Spiked Roller to facilitate the release of any trapped air to produce a smooth surface, and to allow it to dry.
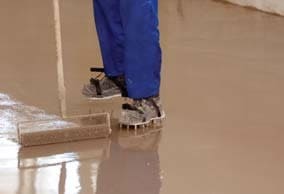
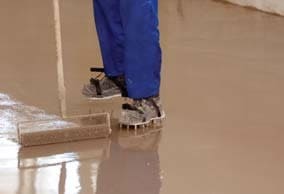
Allow the screed installation to dry for 24 hours before subjecting to foot traffic (or other trades) or installing floor coverings.


TAL MOSAICFIX is available in 20 kg and 5 kg bags from leading retail outlets.
Designed to be 100% compatible, using the TAL range of products ensures fully guaranteed multi-level tiling systems from a single source. TAL products are manufactured in South Africa to suit local climatic conditions.
If you are in any doubt, contact the TAL Technical Advisory Service on 0860 000 TAL (825), email [email protected]. Alternatively, employ the services of an experienced and skilled mosaic tiling contractor.
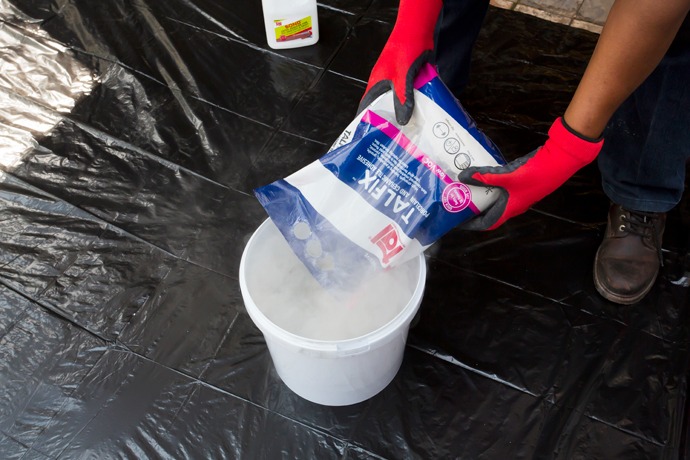
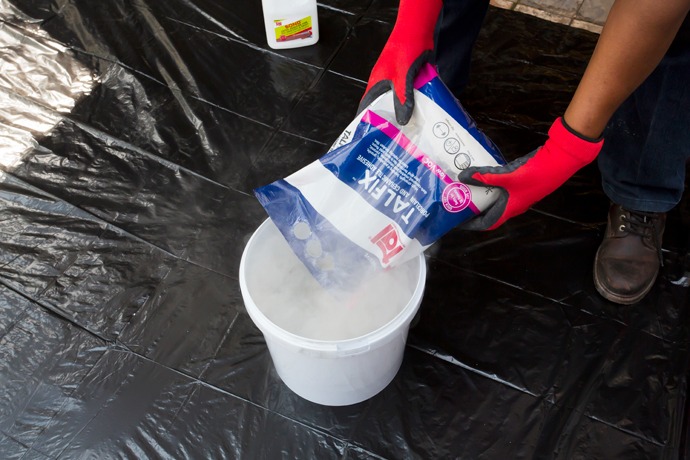
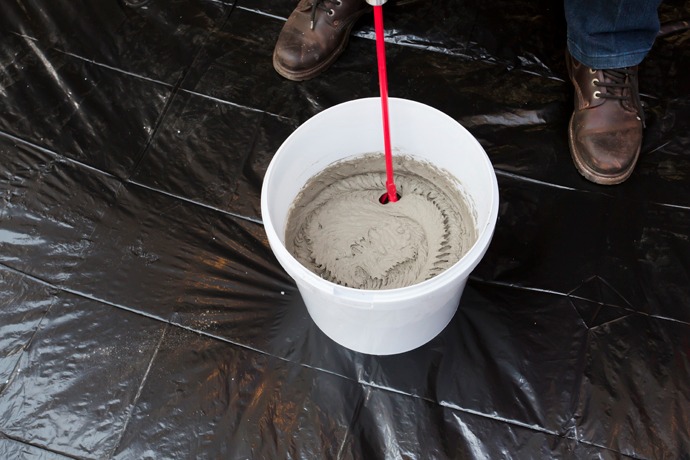
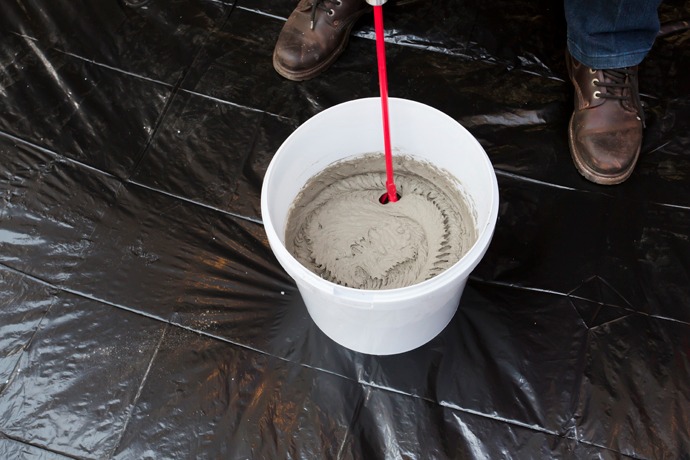
When replacing tiles, it is not always possible to apply the TALFIX directly to the floor, in which case apply the adhesive in a solid bed onto the back of the tile, ensuring complete coverage. Gently trace the notched side of a floor trowel through the adhesive to create ‘ridges’.
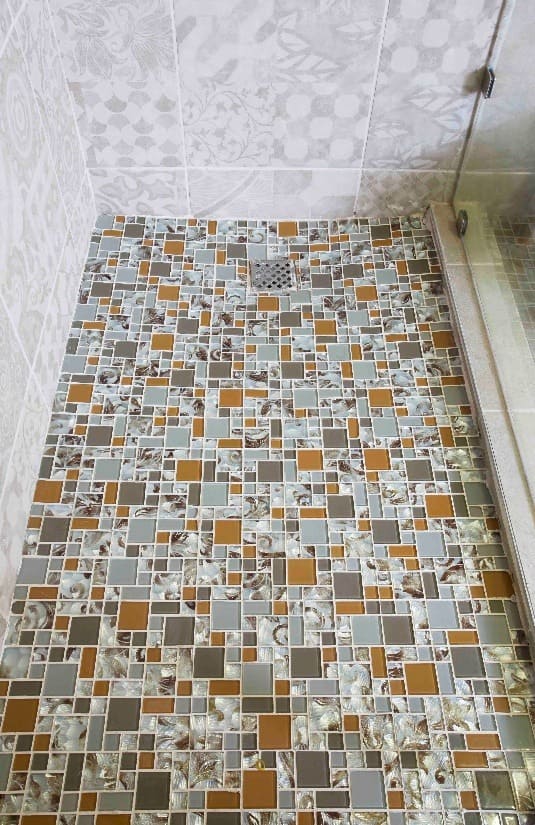
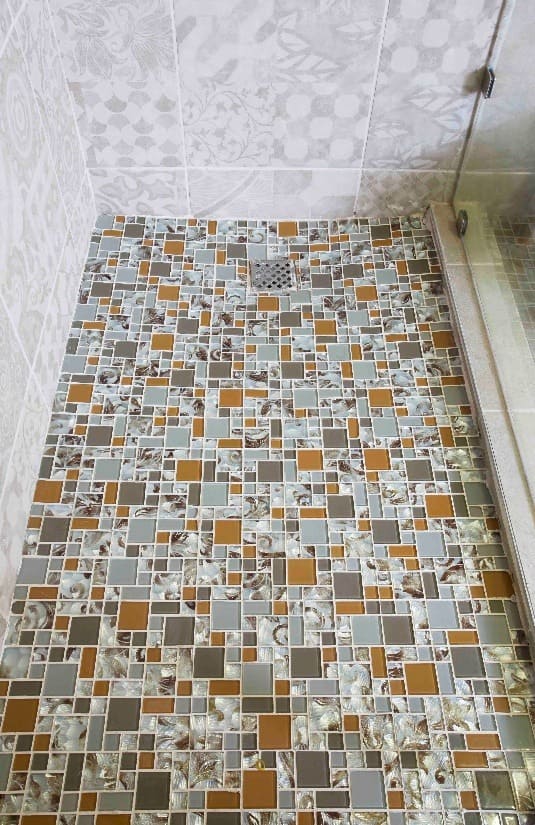
Adhesive system
When tiling onto existing tiles, it is important to only use a quick- or rapid-setting adhesive, as the existing tiles will present a dense, impervious surface, and standard-setting adhesives will take longer to dry. Too early trafficking of newly-installed tiles before the adhesive has set sufficiently can result in hollow-sounding or loose tiles.
Use TAL Tile-To-Tile quick-setting adhesive for tiling onto interior surface beds. When tiling onto suspended slabs and for external installations mix the TAL Tile-To-Tile with TAL Bond, replacing the water in the mix. Alternatively, TAL Bond Powder can be added to the adhesive mixing water.
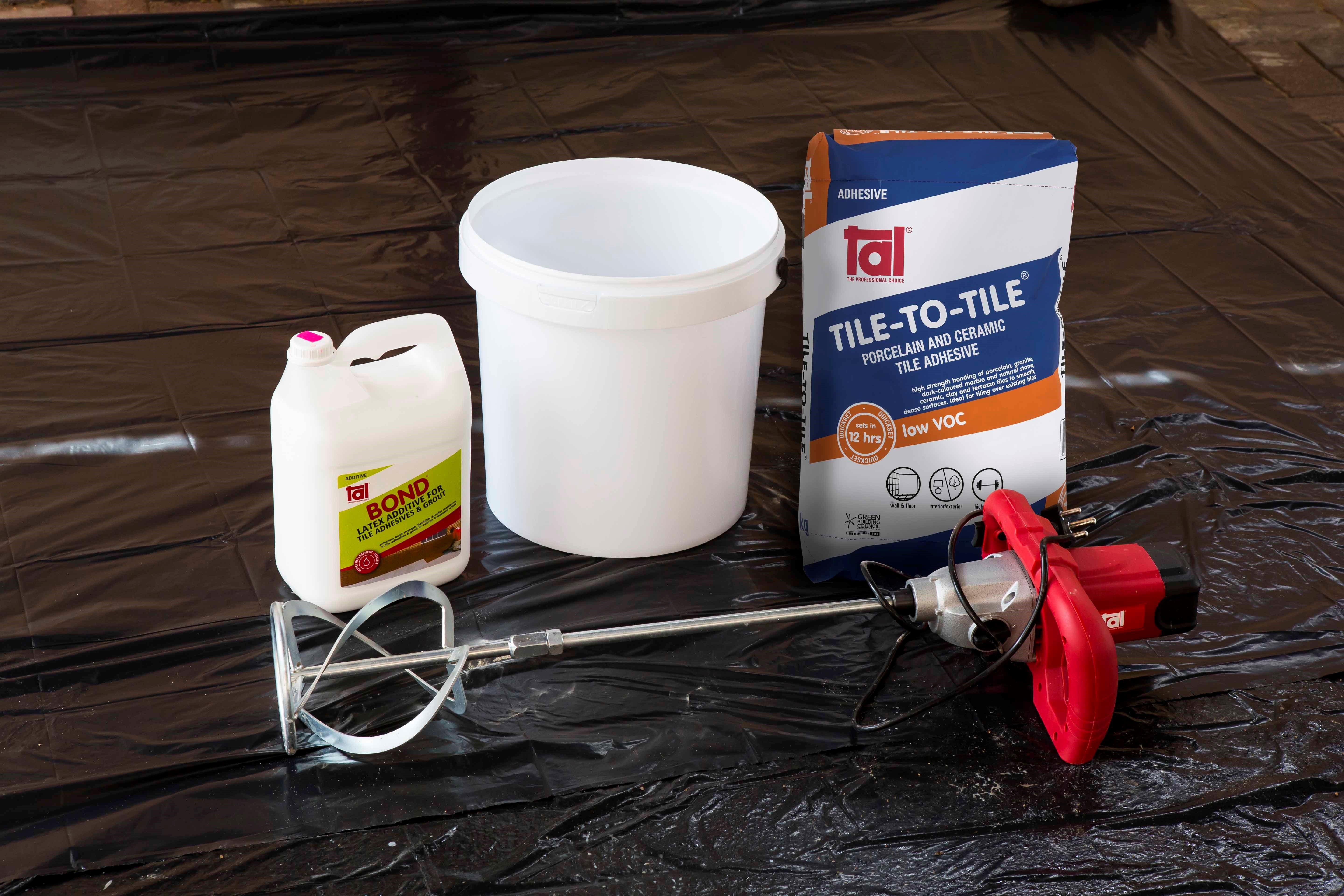
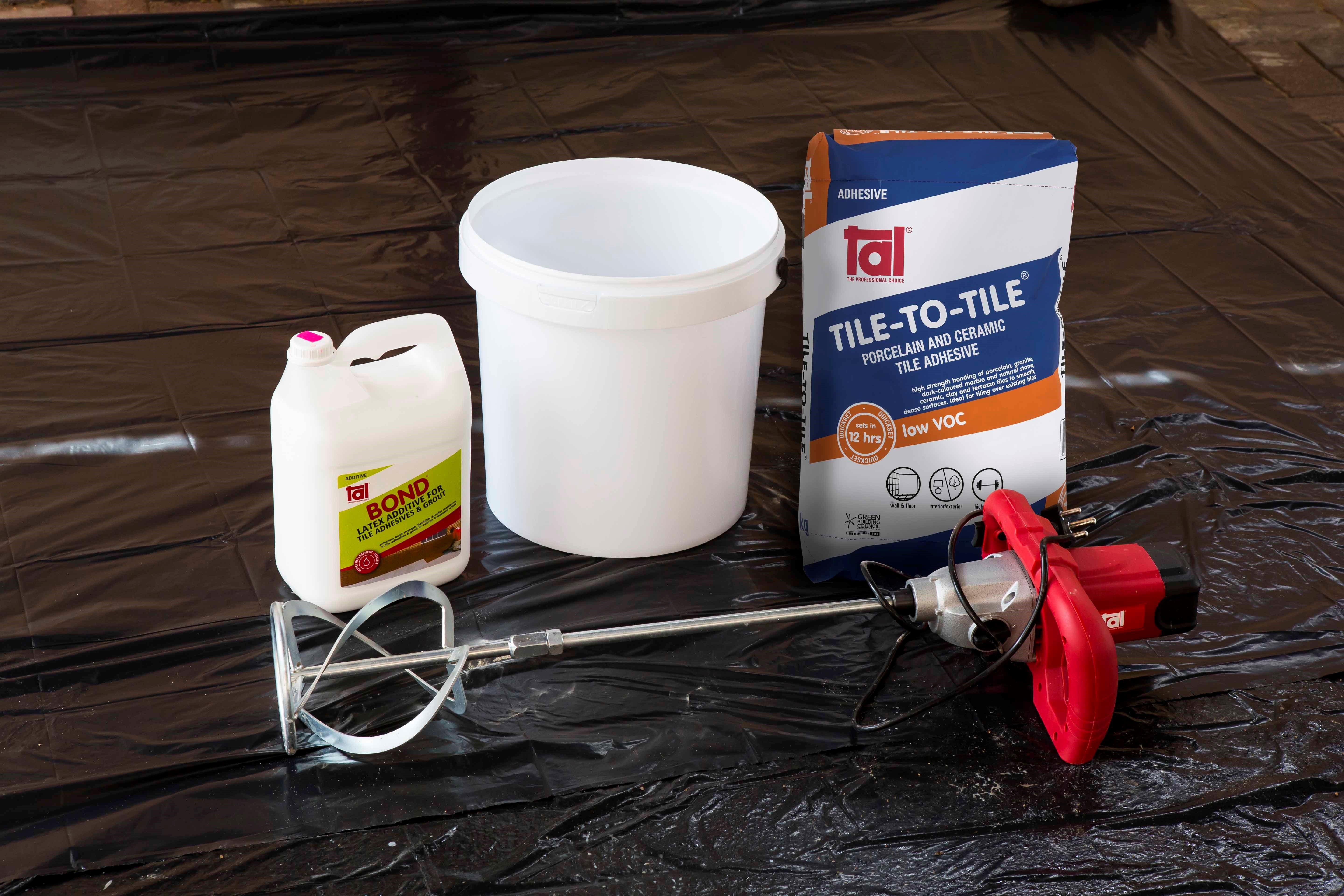
Ensure that there is a solid bed of adhesive at least 6 mm thick beneath each tile.
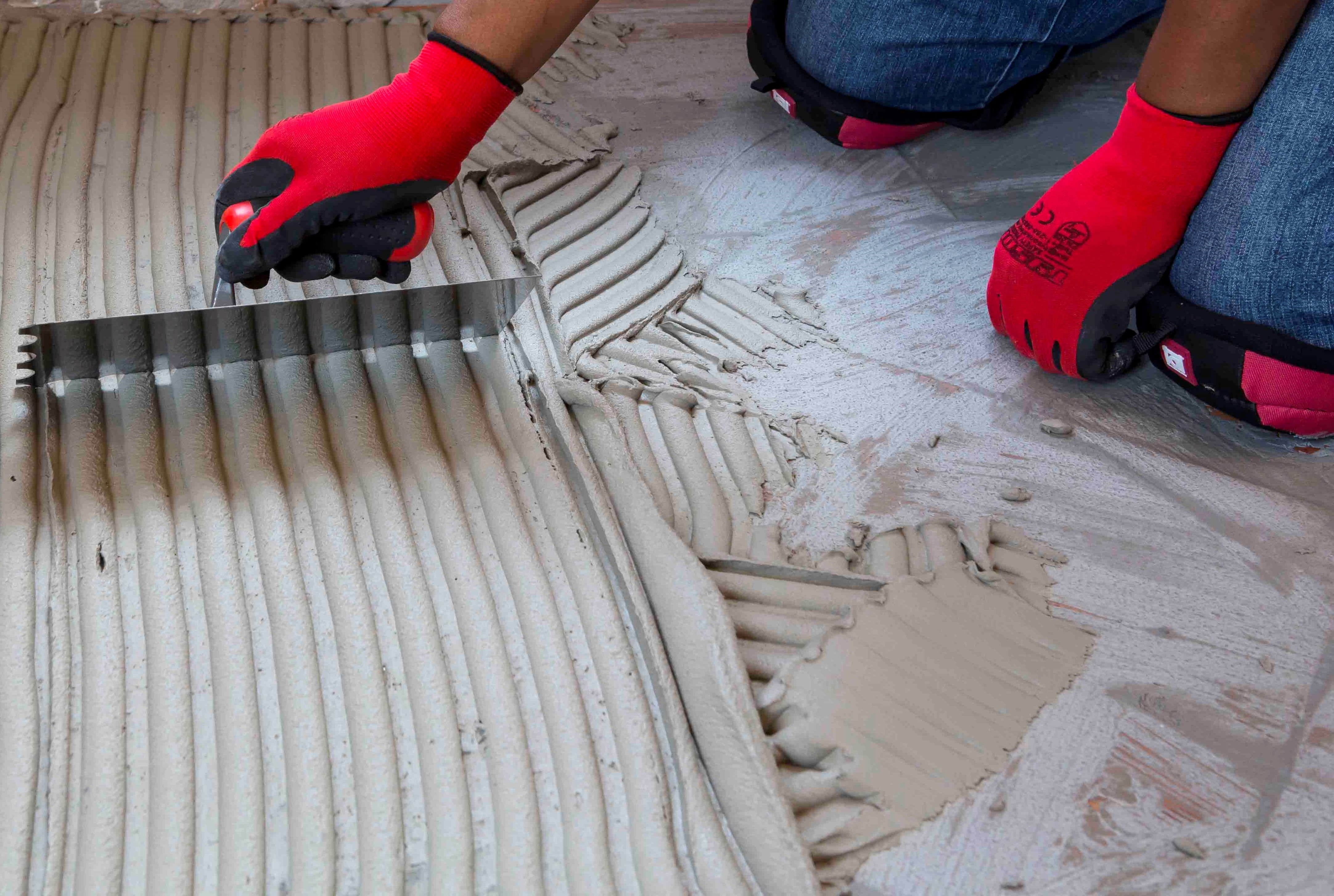
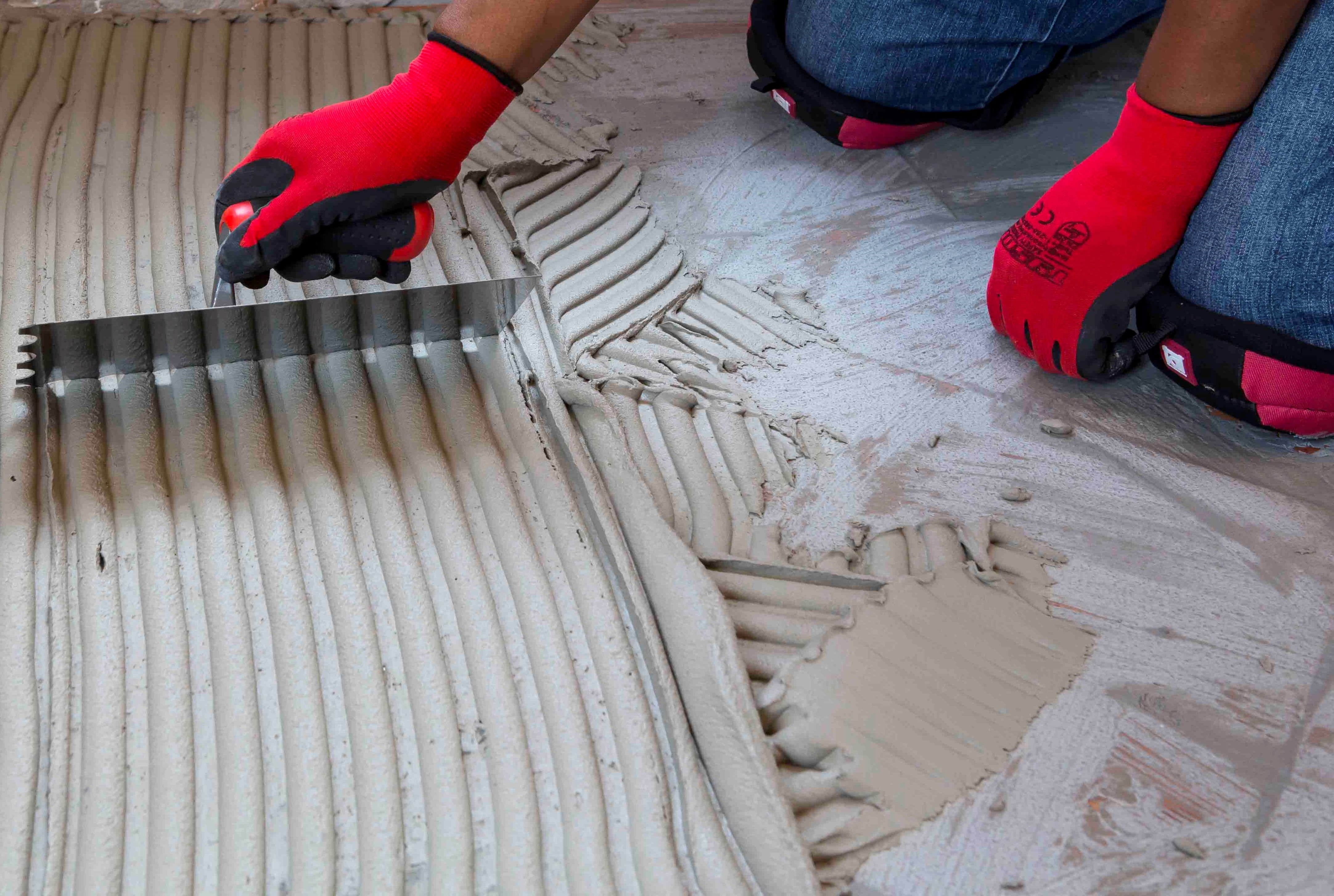
Back buttering with a thin coat of adhesive may also be required when using large-format tiles to ensure full contact with the adhesive bed.
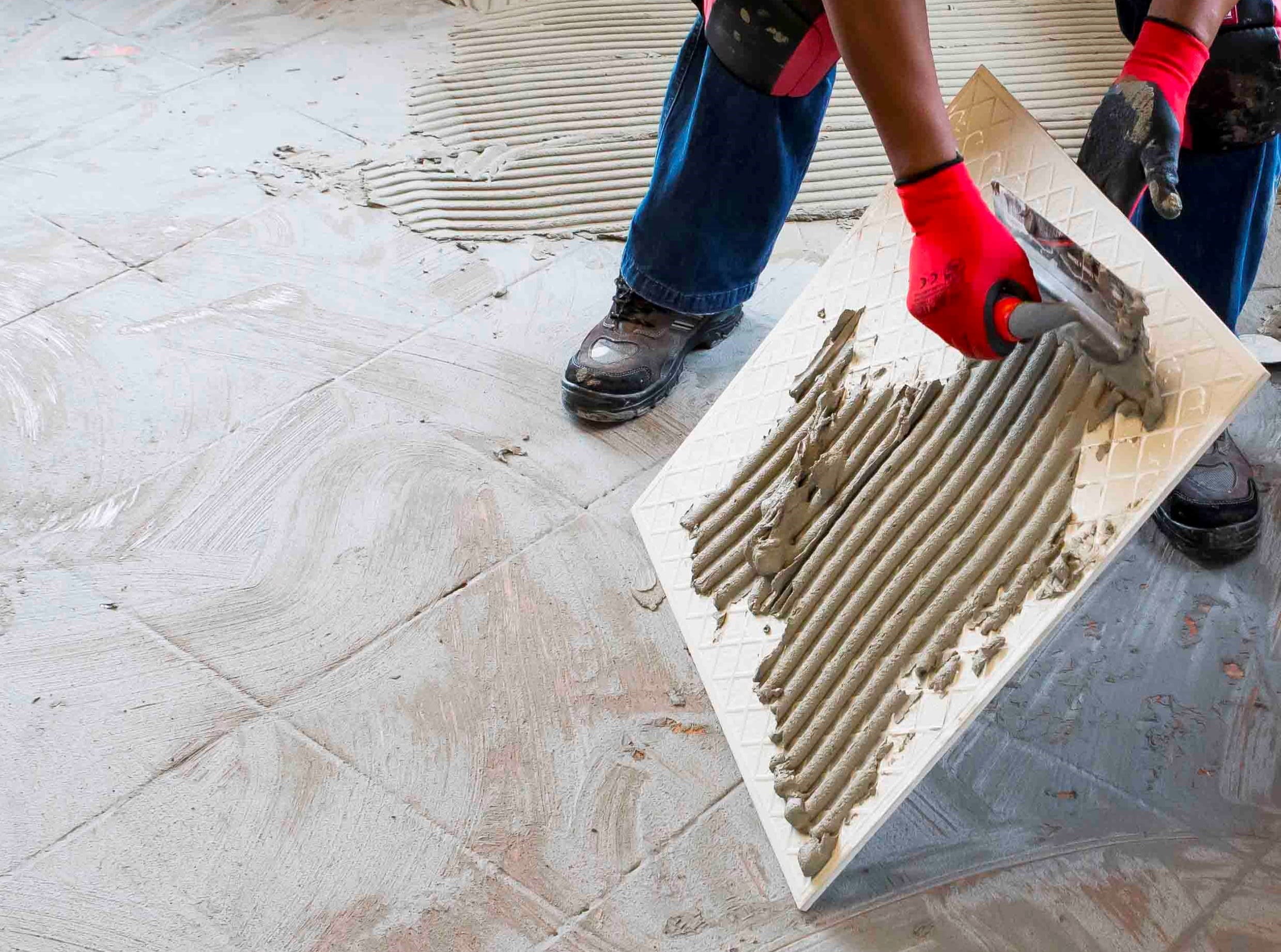
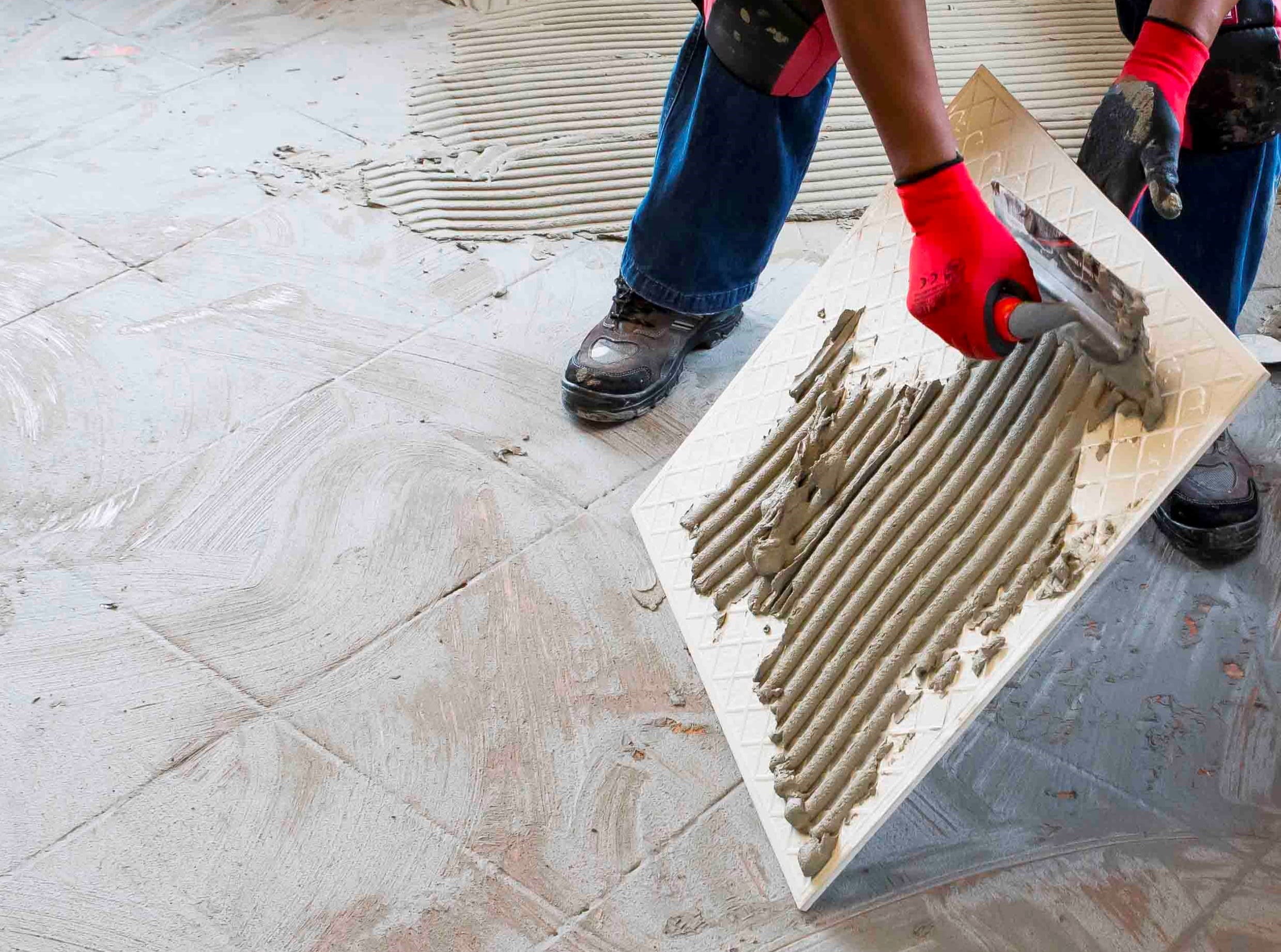
Grouting
Grouting should not be carried out until the adhesive has set sufficiently to prevent the tile installation from being disturbed during the grouting operation (always refer to the adhesive packaging for setting times). When using TAL TAL Tile-To-Tile, allow a minimum of six hours before grouting.
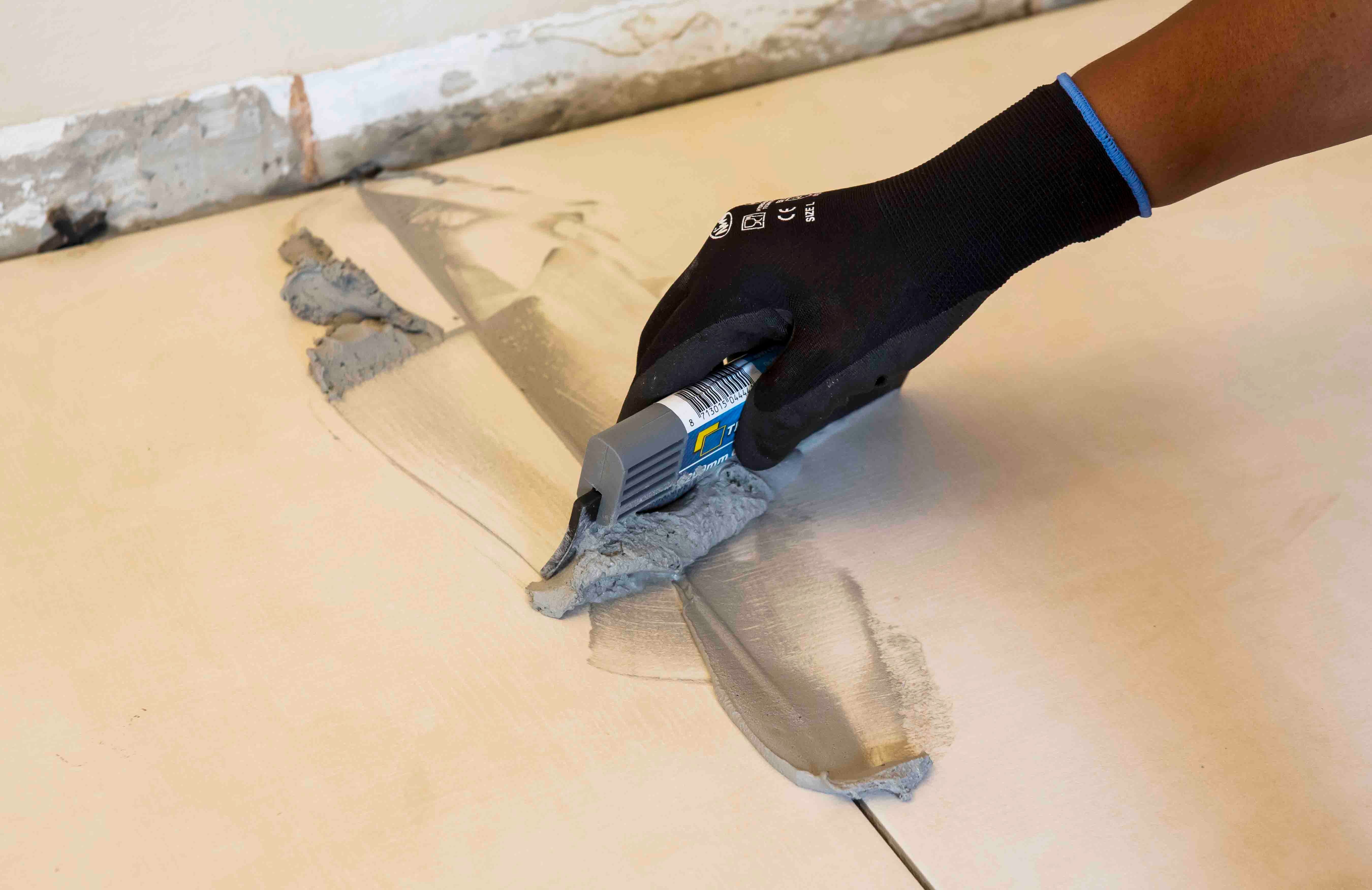
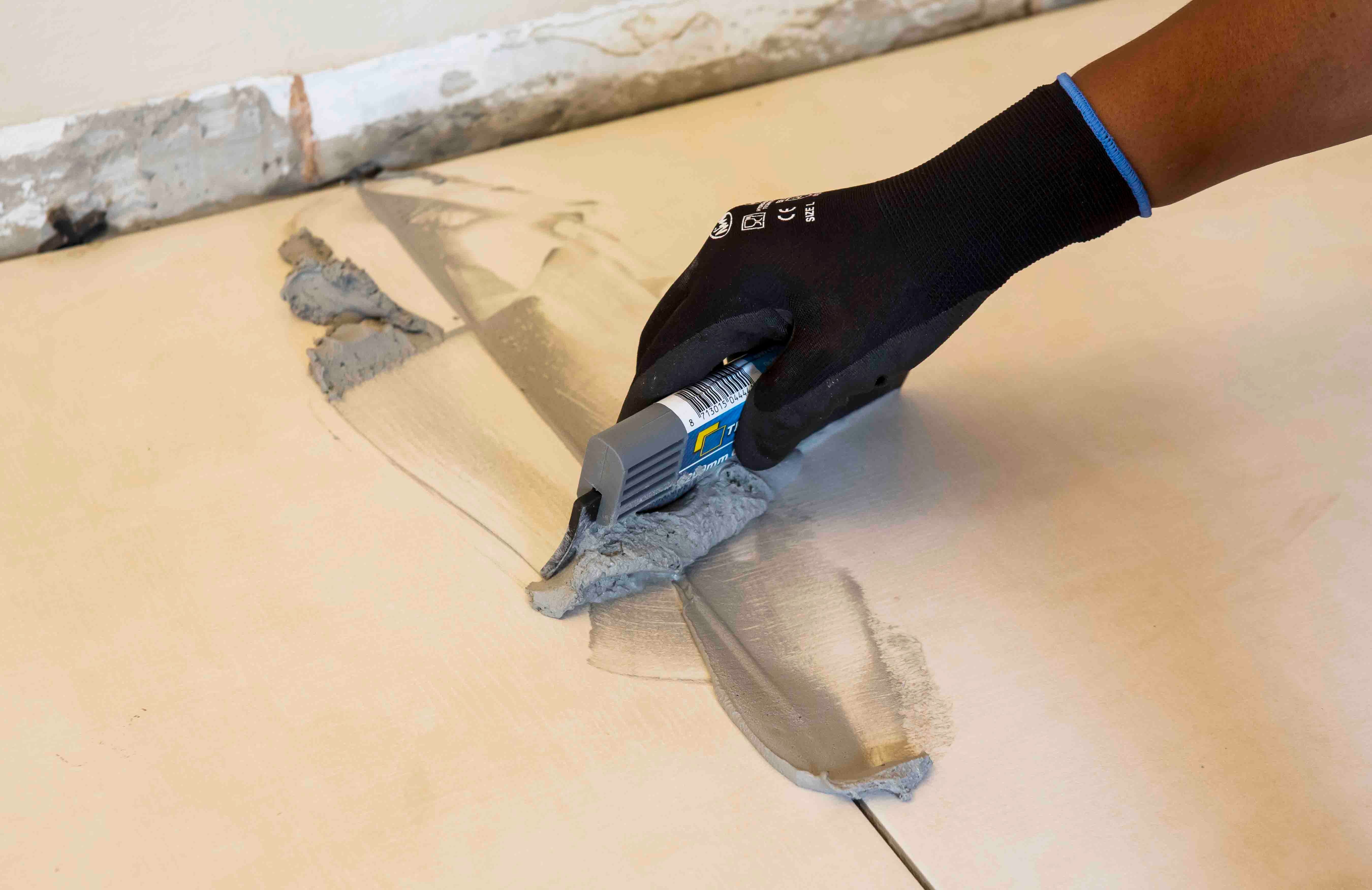
For interior surface beds, use TAL Wall & Floor Grout for filling tile joints up to 8 mm wide. TAL Quarry Grout can be used in wider joints up to 25 mm wide. On suspended slabs and for external installations, replace the water in the grout mix with TAL Bond, or add TAL Bond Powder to the grout mixing water.
Particular care must be taken to clean the grout off the tile face before it hardens completely. This is especially important when an additive such as TAL Bond or TAL Bond Powder has been used. A tile sample should be tested beforehand to ensure that no grout is absorbed through the glaze or into the tile body, thereby staining the tiles permanently.
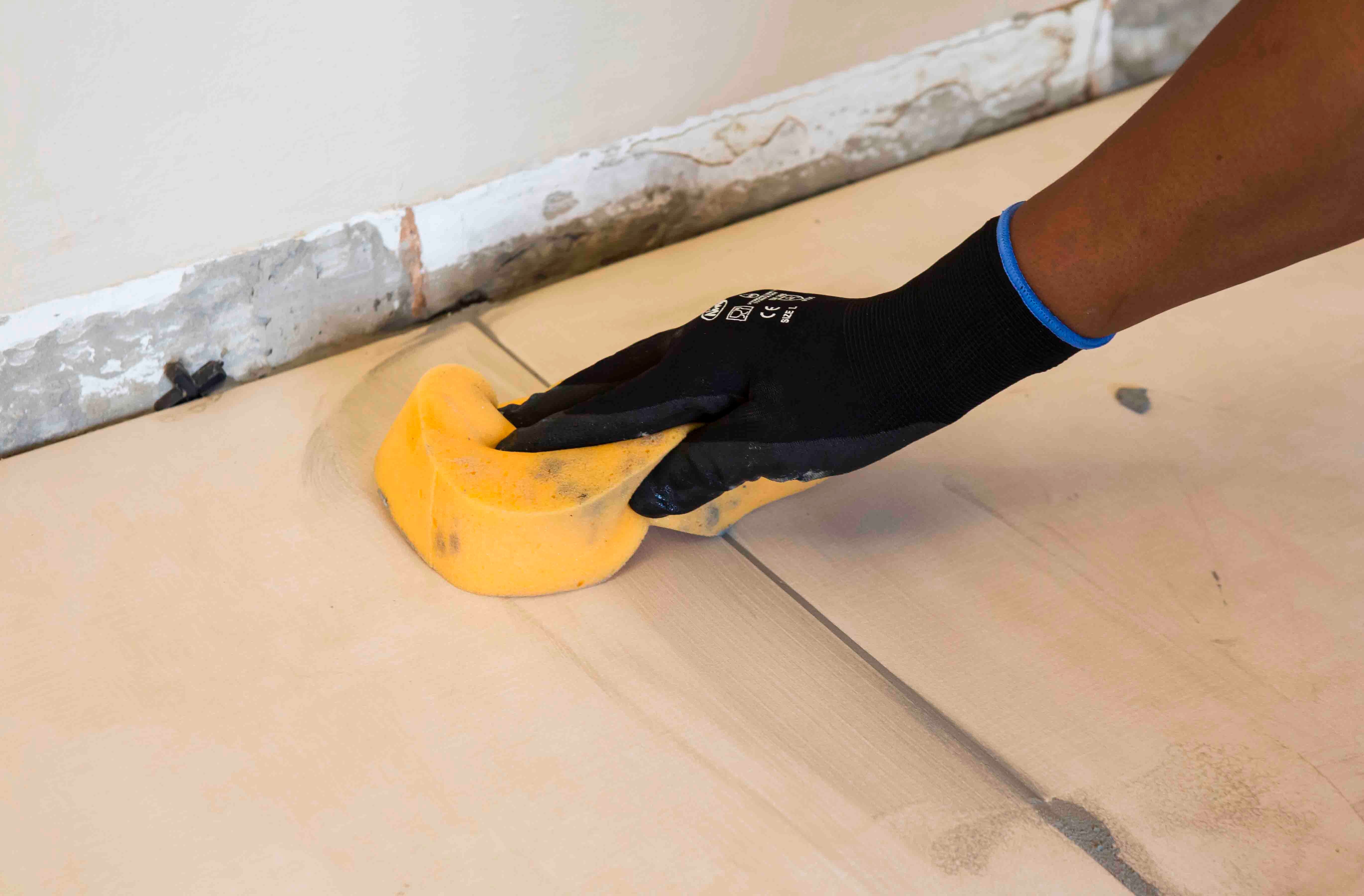
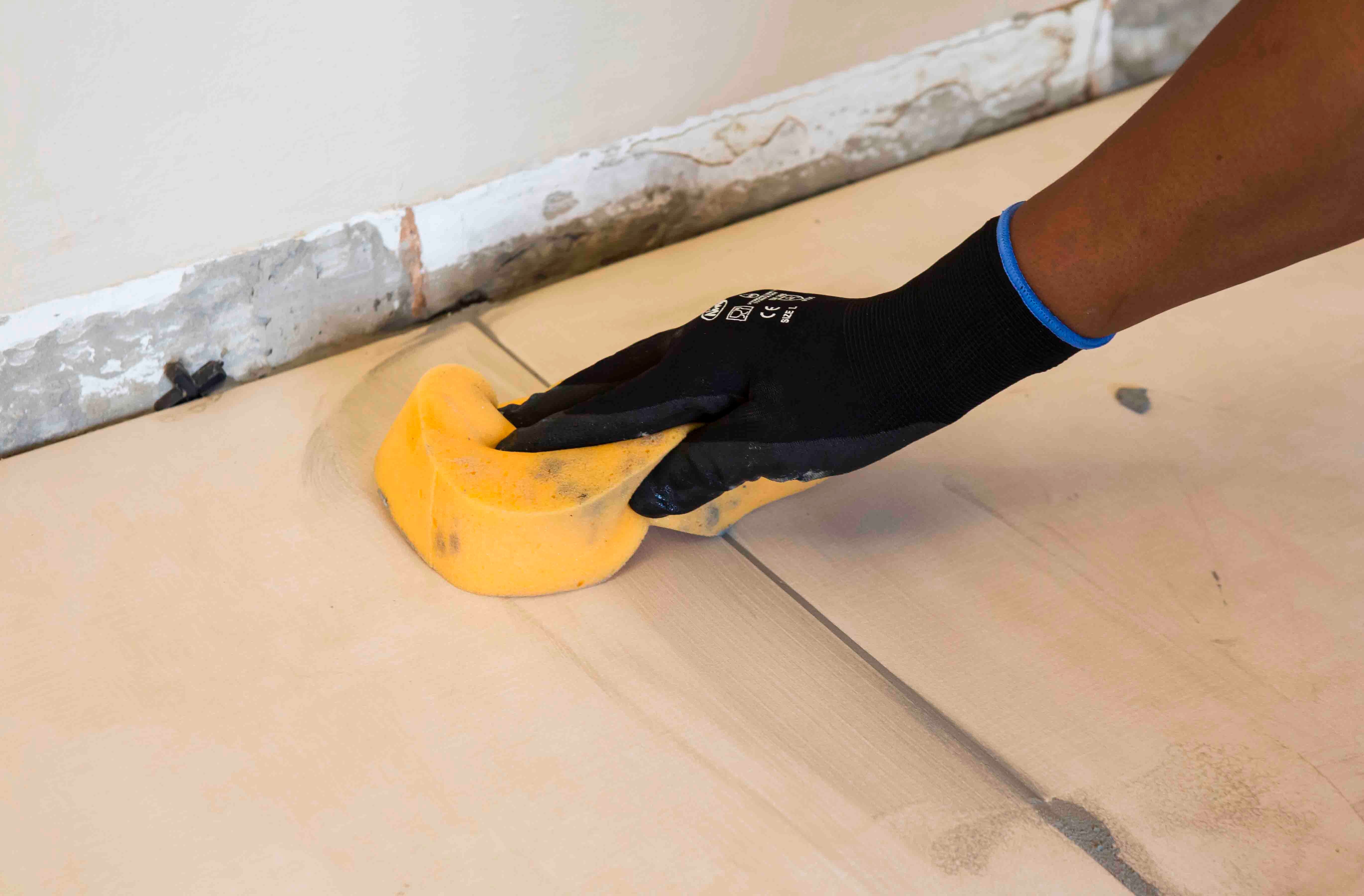
Movement joints
The lack of movement joints in tile installations is a major cause of tile failure. When tiling over existing tiles, the existing structural and movement joints must be maintained in the new tile installation. The movement joints should be at least 5 mm wide and extend through the adhesive and both tile layers.
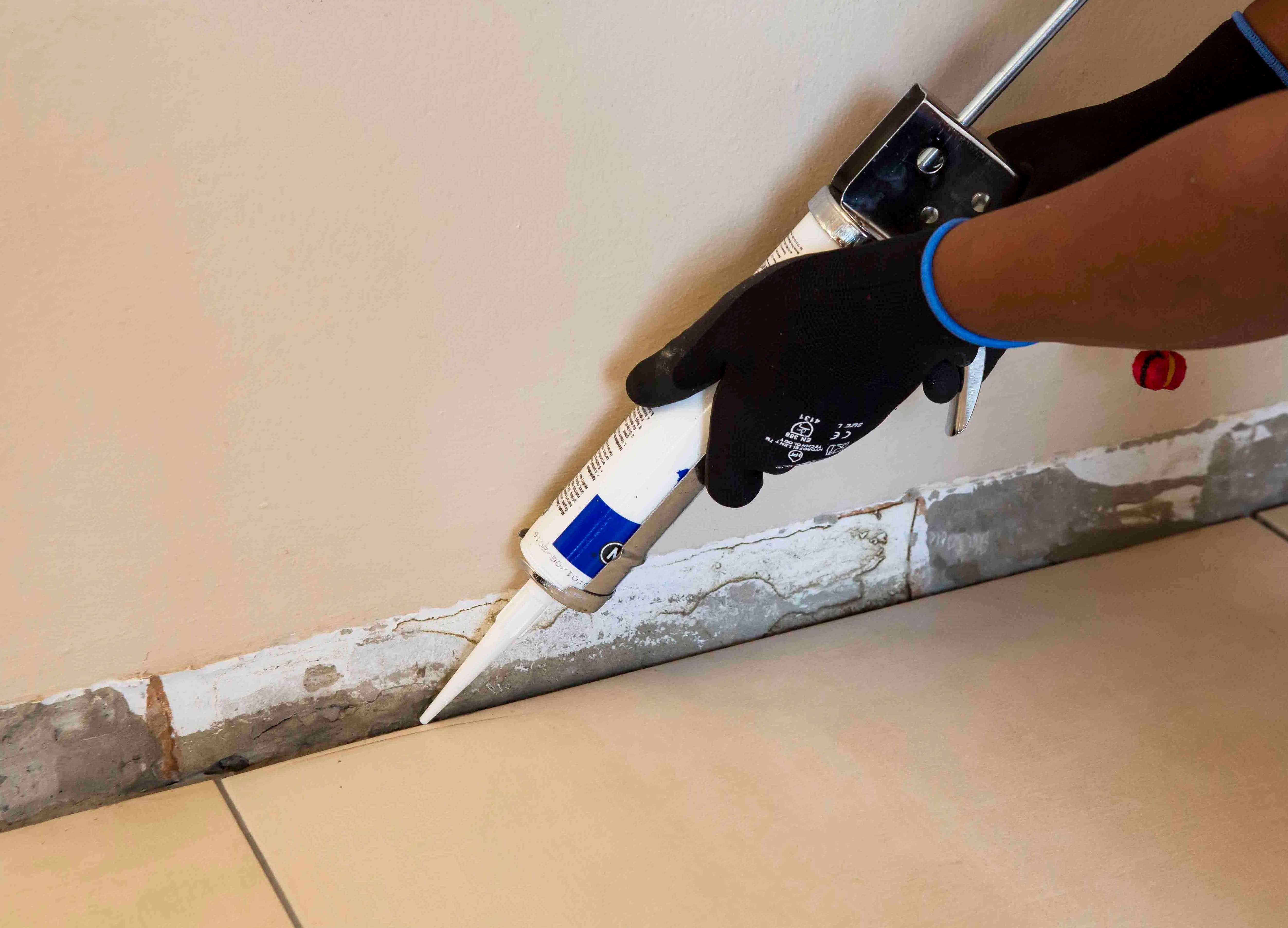
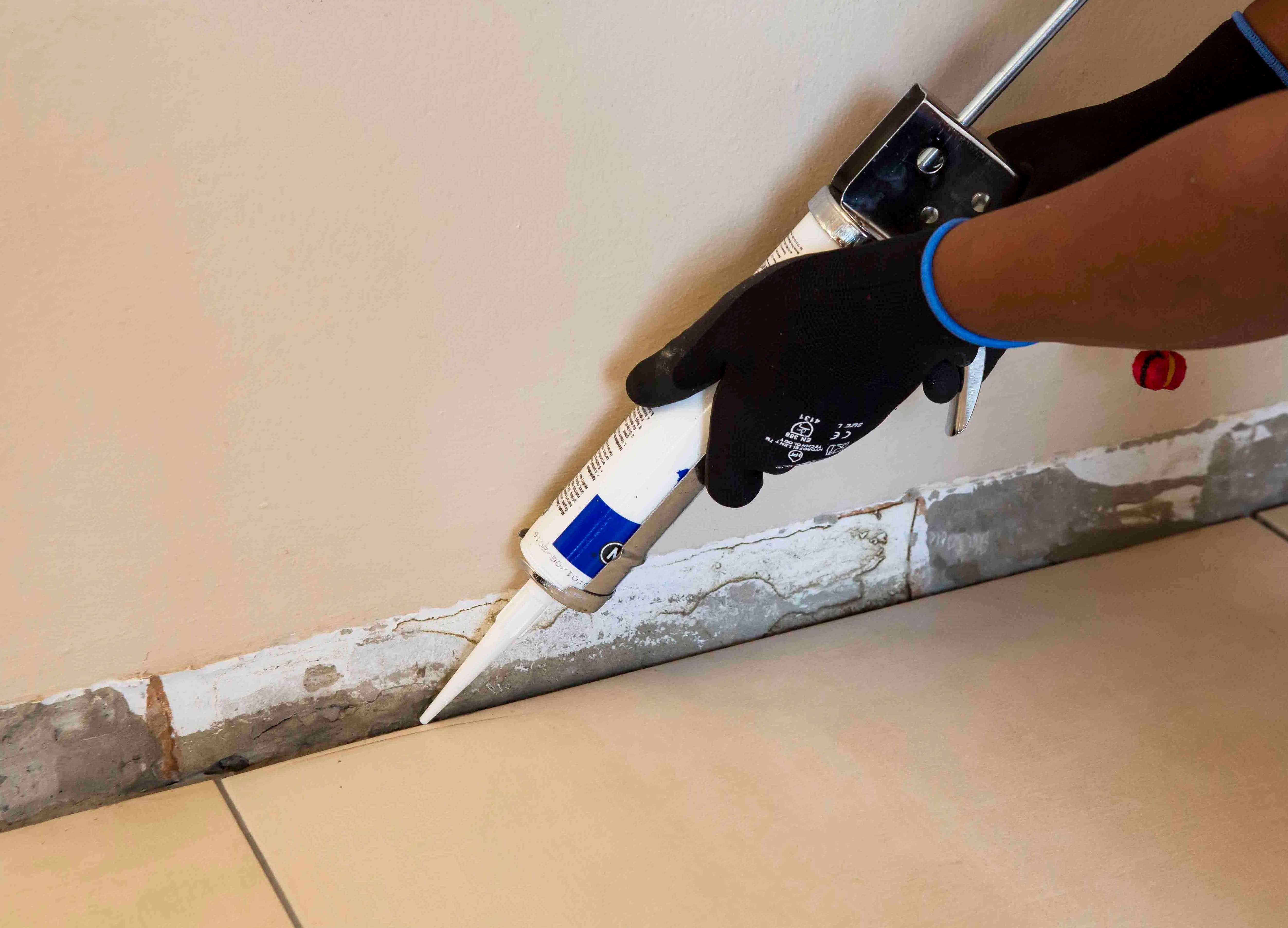